FOYA Category Winners & Honorable Mentions for 2020: Examples of Excellence

Each year, ISPE celebrates innovations and advances in pharmaceutical manufacturing technology with its Facility of the Year Awards (FOYA) program. This year, we added a new category, Social Impact, to recognize companies that developed new standards and practices to prevent drug shortages and increase patients’ access to medicine, designed new tools or techniques that reduced the cost of drug products, or accelerated a shift to sustainable facility design that has significantly reduced environmental impact.
You can learn more about this year’s winners at the FOYA Virtual Education Sessions on Tuesday, 3 November, during the 2020 ISPE Annual Meeting & Expo. Each company will give a 15-minute presentation about the challenges and successes of their project. For more information or to register, visit ispe.org/foya
The 2020 Facility of the Year Award winners include well-known names in the pharmaceutical world as well as a relatively new company. All award recipients and honorable mentions share the same dedication to serving patients worldwide.
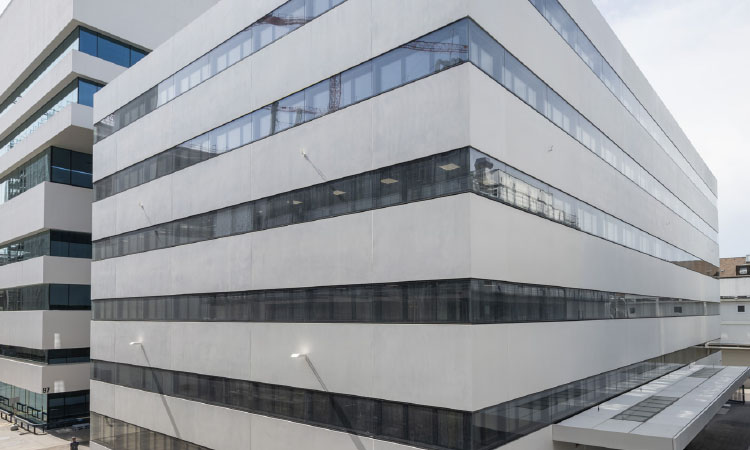
Equipment Innovation: F. Hoffman-La Roche Ltd
A Researcher’s Dream Come True
In most countries, it is a legal requirement that any new human medication be tested on animals. However, animal facilities are usually housed in the basement and not typically talked about or lauded. With their new in vivo facility in Basel, Switzerland, F. Hoffmann-La Roche has successfully reinvented animal research laboratories. Thanks to a team dedicated to exploring new ways to improve the status quo, Roche was able to discover clever and unorthodox solutions to common issues found at in vivo facilities and created a technological masterpiece that sets a gold standard for future laboratories.
To build a new facility, Roche had to demolish an existing building on their site and extend the pit. Before the new facility, Building (B098), was constructed, animal husbandry was split over various buildings of the Basel site, some of the infrastructure was outdated, and productivity and efficiency were not optimal. Roche found a way to allow natural light into the laboratory without affecting animals’ physiological rhythm. Intelligent ventilation and fully automated cage handling outside the barrier zones reduce researchers’ exposure to allergens and physical strain. All study and animal housing rooms have a modular structure and can be reconfigured from a small study room with anteroom into a large animal housing unit (or any type of room in between); these reconfigurations can be achieved within just two to three weeks, almost silently, and without disturbing adjacent areas. Roche completely redesigned automation and robotics for the building and merged third-party IT products with Roche-specific IT solutions to develop the Roche In Vivo Building IT System—setting new pioneering technological standards.
“The project demanded intensive collaboration and problem-solving skills from everyone involved,” said Christof Specht, Roche Project Manager “Our employees have told us that B098 is an in vivo researcher’s dream come true, even beyond imagination. Roche is proud to be leading a new era of novel therapeutic modalities.”
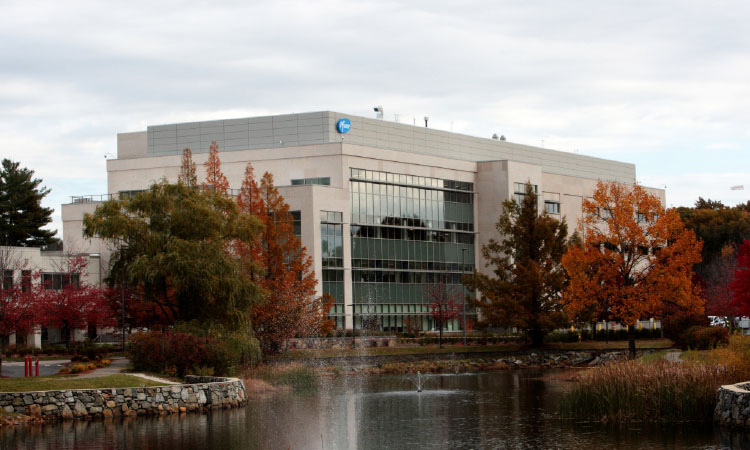
Facility Integration: Pfizer INC.
New Standard for Physical, Operational, and Intellectual Integration
Thanks to careful planning and astute attention to detail, Pfizer’s new Andover Clinical Manufacturing Facility (ACMF), built on their master-planned 70-acre Andover, Massachusetts, campus, looks as if was always meant to be there. Pfizer relocated existing manufacturing capabilities from Chesterfield, Missouri, to the new facility, which allowed them to integrate research and development (R&D) and expand biological products from 14 campaigns to a future maximum capacity of 21.
Pfizer was able to add the 175,000-square-foot clinical manufacturing facility to their Andover site without growing their carbon footprint. They did not have to add any new core utilities, support systems, or amenities to bring the facility online. The five-story building houses five independent manufacturing suites dedicated to the development of new biotherapeutics and vaccines to support trials in disease areas such as oncology, rare diseases, infectious diseases, hemophilia, and rheumatoid arthritis. Each suite operates completely independently of the others, and all five can operate simultaneously.
The project demanded intensive collaboration and problem-solving skills.
The ACMF runs both microbial and mammalian processes and deploys both single-use plastic and stainless steel technologies. Each suite can be re-configured to handle complex steps such as refold reactions and homogenization. Technology innovations include wireless tracking for equipment. Additionally, Pfizer has developed a space where R&D, clinical manufacturing, and commercial manufacturing professionals work together to share their knowledge and expertise.
“A project like this is really months of preparation for the day you will go live—the day you become a productive contributor to human health and wellness, and to Pfizer’s mission,” said Lauren Gomes, Director, Clinical Manufacturing, Pfizer. “As of June 2020, all suites within the facility are fully operational. The flexibility of the facility and the ensuing relationships with collaborating teams have enabled us to complete technology transfer of complex processes within two months. One of our upcoming projects will be producing a drug substance for pandemic supply of the COVID-19 mRNA vaccine.”
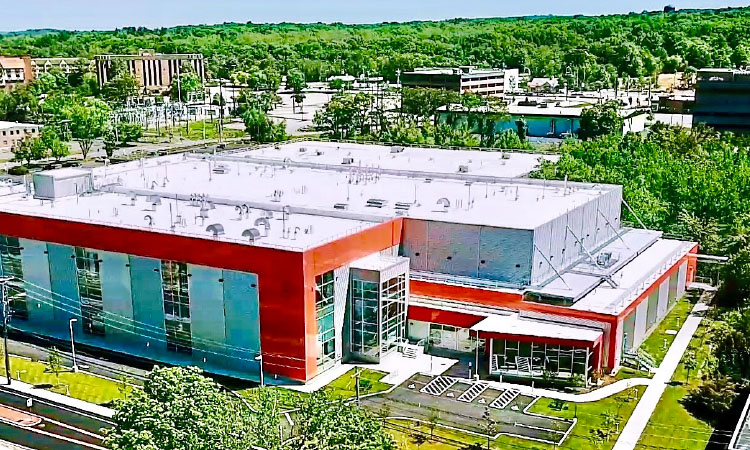
Facility of the Future: Sanofi
Facility Flexibility Reaps Rewards
Sanofi is a pioneer in continuous biologics processing and has several rare-disease enzyme replacement therapies that are produced using large-scale perfusion reactors and novel cell separation technologies. For its digitally enabled integrated continuous biomanufacturing facility in Framingham, Massachusetts, Sanofi used a wide range of cutting-edge manufacturing technologies to develop an efficient, flexible, and sustainable manufacturing platform. One of the most significant aspects of their design is the commercial implementation of integrated continuous biomanufacturing (ICB), which made it possible for them to adopt a modernized perfusion-based cell culture process where smaller, single-use technologies replace traditional large-scale stainless steel reactors and capture equipment.
Ultimately, the ICB process results in improved product quality and consistency, increased process robustness, the generation of massive process da-ta analytics with 770 million data points sampled each day, and reductions in the facility’s processing footprint, raw material usage, and energy consumption. Sanofi developed new and innovative ways to use single-use technologies, many of which had never been commercially implemented. The facility was designed for flexible operations, rapid changeovers, and multiproduct operations. Sanofi created a digitally integrated, paperless ecosystem, and the facility is equipped with large touch-screen displays that help maintenance and operations staff accomplish their daily activities.
“The facility includes many of the traditional concepts of flexible facility design, including single-use technology and flexible ‘ballroom’ designs, accommodating a wide variety of equipment design and scale. Utilizing digital technologies enhances the flexibility of the facility, enables reconfiguration in response to changes in produce demand, and creates a shop floor experience that is intuitive to the operator. We believe that we have pushed these concepts to new levels with our novel processes, deployment of technology, and digital integration,” said Navin Tiwari, Head of Digital Shop Floor and Automation for Sanofi.
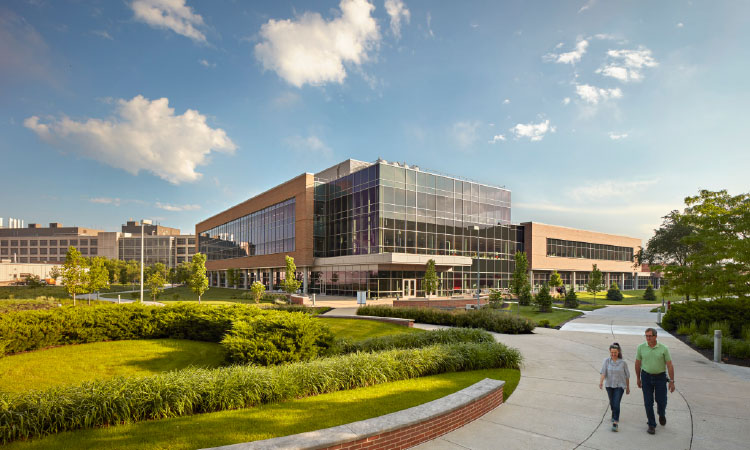
Operational Excellence: Eli Lilly and Company
Improving the Drug Discovery Process
As a global healthcare leader, Eli Lilly and Company strives to discover and bring life-changing medicines to those who need them. In support of this mission, Lilly spent several years examining the traditional, industry-accepted belief that drug development is a drawn-out, time-consuming process characterized by complex challenges and long delays, and set out to determine what facility factors could help improve the pharmaceutical development process. They analyzed many of the basic assumptions of the development process and, as a result, implemented leading-edge improvements throughout their new facility, the Innovation Development Center.
Located at the center of Lilly’s Indianapolis, Indiana, campus, the new center brings modeling, analytical, and formulation scientists together with organic chemists and engineers in a collaboration-centric workspace and enables Lilly to effectively accelerate traditional time scales—reducing the development time from years to mere months. One of the most common delays development teams face is the need to reconfigure a laboratory to support a new approach. Sometimes, the progress of the candidate compound is put on hold while the team works to design a new lab, which then has to be constructed before the development process can continue. Lilly’s Innovation Center was designed to allow researchers to transform their laboratory to support new or revised processes in a matter of days. As with the laboratories, the workspaces were designed to be flexible and easy to configure based on the users and their needs. There are no assigned workspaces at the Innovation Center; employees can work wherever is best suited for their current activities. Teams are able to organically formulate project groups on a day-to-day basis in areas that match and support what is happening in the lab.
“Since we moved to the Innovation Center, we have seen time and time again how it has allowed colleagues across multiple functions to co-locate and interact directly with each other, ultimately helping to further accelerate development of our new medicines. It truly is a very special place to work,’’ said Sarah O’Keeffe, Lilly’s Vice President of Small Molecule Design and Development.
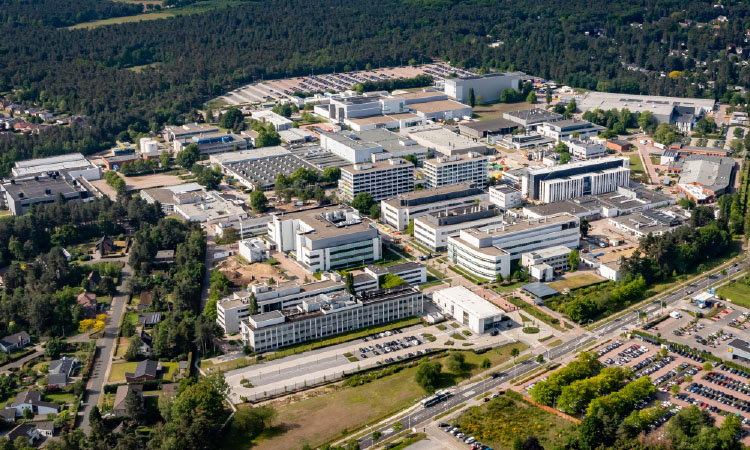
Process Innovation: Janssen Pharmaceuticals, Belgium Campus
Changing Strategy to Change the Future of Drug Delivery
Until recently, Janssen Pharmaceuticals developed and manufactured all tablet formulations in a multipurpose batch facility. However, as the company formulated a mission that focused on making the patient the center of all decisions, improving quality, reliability, and control, and reducing development and scale-up cycle times, they found that the batch platform did not support their vision. Janssen decided they had to completely change strategy to support their new mission and embarked upon an end-to-end (E2E) strategy that included investing in continuous manufacturing (CM) as their preferred technology platform for all future oral solid dosage formulations. To support their new E2E strategy and commitment to CM, Janssen designed, installed, and qualified a new CM line, Mirror 1, at their drug product pilot plant in Beerse, Belgium.
Mirror-1 will be used to support all development and clinical manufacturing activities, and an identical CM line, Mirror-2, is under construction at Janssen’s commercial site in Latina, Italy. Since Janssen planned from the beginning to build an exact copy of Mirror-1 at a different location, they had to consider the requirements and limitations of both facilities when developing the line. Together, the two identical lines will enable seamless one-to-one tech transfers, without additional scale-up efforts, resulting in overall benefits such as shorter timelines and reduced active pharmaceutical ingredient (API) consumption. Janssen not only developed a new CM line but also set up cross-functional initiatives to make sure the company was ready to start developing new compounds once the Mirror-1 line was complete. Janssen collaborated with academics, partnered with other pharmaceutical companies, and established connections with health authorities worldwide to help them formulate renewed development strategies and best practices and establish new methodologies.
“We strongly believe that our unique strategy will accelerate the development of new medicines, with a significant increased level of process understanding and controls, providing more robust processes and delivering better and safer products,” said Luca Russo, Global Head, Clinical Supply Chain, Janssen.
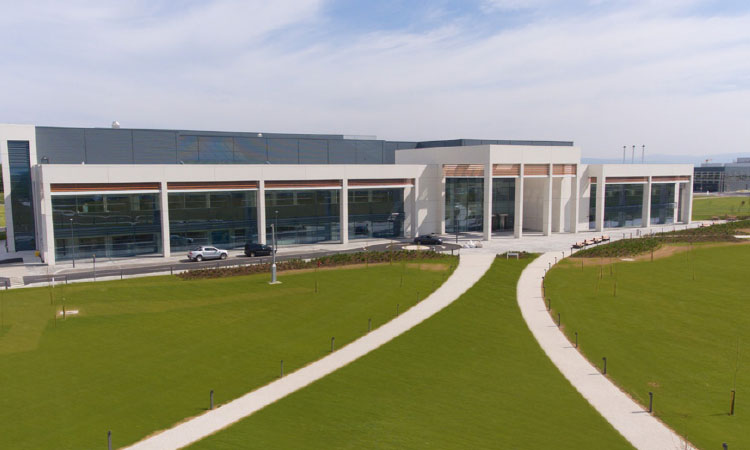
Project Execution: Bristol Myers Squibb
Billion Dollar Commitment to Biologics
The biopharmaceutical industry is thriving in Ireland, and Bristol Myers Squibb’s Cruiserath Biologics is at its forefront. In 2014, BMS closed their Dub-lin-based API site and announced a $1 billion commitment to building a new, world-class biologics manufacturing facility in its place. The investment helped BMS increase their biologics manufacturing capacity and played a central role in the company’s global manufacturing network. At the time, the project was the largest single investment by BMS outside of the United States and the second largest life sciences sector investment in the history of the Irish state.
The result of this $1 billion investment is a new biopharmaceutical campus where immuno-oncology medicines are manufactured for patients worldwide. The large-scale site (with six 15,000-liter bioreactors) will produce multiple biologic medicines annually on a rapid-turnover, campaign basis for high efficiency and throughput. It is designed for future expansion into a concurrent-campaign multiproduct facility. Innovative concepts were applied to the facility design to facilitate higher throughput and rapid product changeover while minimizing equipment redundancies and maintenance shutdowns. The manufacturing execution system design integrates with the production automation system and collectively utilizes flexible and lean recipes. This allows for easy and quick configuration of the system for the next product to be produced.
“The Cruiserath campus represents the largest ever capital investment for the company and is the first Bristol Myers Squibb biologics manufacturing facility in Europe. We set out with a vision to build a world-class biopharma campus and state-of-the-art facility; to receive this highly coveted award and industry recognition indeed signifies we are well on our way in this endeavor,” said Noel Heaney, General Manager, Cruiserath Biologics, and Executive Director, EU Biologics.
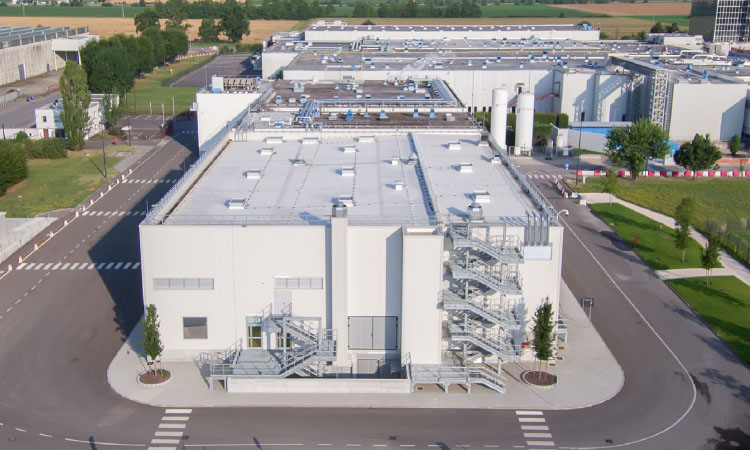
Social Impact: GSK—Glaxosmithkline
Accelerated Delivery to Meet Critical Need
GSK has a broad portfolio of innovative and established medicines. When they partnered with ViiV Healthcare to develop a newly acquired investigational HIV product, fostemsavir, one of the first things they needed to do was develop a new facility to handle production of the first-in-class HIV treatment. Because the drug is typically used by patients with previous viral failures who have limited or no treatment options remaining, time was of the essence. GSK met the challenge, and in just 15 months, the project team constructed and commissioned a greenfield NPI facility for high containment in Parma, Italy.
Meeting the accelerated schedule required a highly integrated program including concurrent design, construction, and commissioning. For the first time in the Italian industry, an integrated project delivery approach was used. Designers, contractors, and suppliers from diverse backgrounds and experiences worked together to capitalize on the talents and insights of everyone on the team. The GSK team reduced the overall design time by overlapping the design, procurement, and construction phases, thus changing the inherently iterative nature of the design process. Interactive and decision-making workshops were held to evaluate different layout, facility, and process manufacturing options. The team also used three-dimensional building information modeling from the early stages of design, developed a strategy to develop user requirement specifications so that equipment could be ordered at the end of concept design, and divided the building into three separate construction zones, each operating simultaneously.
“In December 2019, we filed for FDA approval for fostemsavir, after our fastest-ever project build,” said Mike Mungall, Vice President, Global Capital Projects, GSK. “The project team, the Parma site, and everyone who had a part in making this happen is proud to be involved in developing a new treatment that could help people living with HIV who are not able to suppress their virus with other medicines and who could be left with few or no treatments available.”
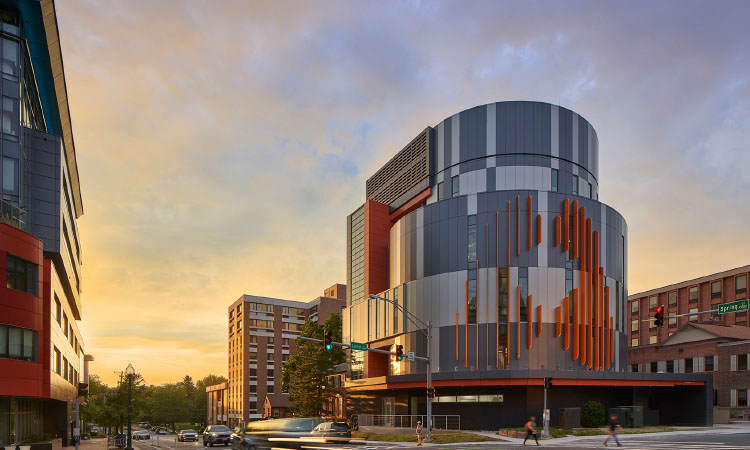
Social Impact: United Therapeutics
A Company Built from Love
In 1994, Dr. Martine Rothblatt learned that her seven-year-old daughter had pulmonary arterial hypertension, a life-threatening orphan disease, with no viable medicine on the market. Because orphan diseases affect a small percentage of the population, cures are not typically a research priority—so Rothblatt took matters into her own hands and made it her life’s mission to find a lifesaving treatment. She and her team at United Therapeutics were successful, and several years later, they expanded their focus to include the development and commercialization of unique products to address more unmet medical needs, including those of children with chronic and rare life-threatening conditions. One of those products is Unituxin (dinutuximab), which has proven effective in treating and reversing high-risk neuroblastoma, a rare form of cancer that typically forms on immature nerve cells in children under the age of 5 years and affects approximately 800 children a year. The company’s manufacturing and research capability was limited due to their existing biologics manufacturing capacity. To treat more pediatric patients, conduct research on other life-threatening illnesses, and bring hope to more families, United Therapeutics knew they had to expand their operation, and so they decided to build a new facility, the Dinutuximab-Dedicated Oncology Medical and Analytical Laboratory (DDOMAL) in Silver Spring, Maryland.
Space was the first obstacle, so the company partnered with local government to pass legislation that exempted the floor area housing mechanical, engineering, and plumbing equipment required to support the drug manufacturing process from the total gross-square-feet calculation. This legislation not only made the project feasible but also will promote the future development of the life sciences industry in Montgomery County, Maryland. Additionally, United Therapeutics stayed connected to the local community during construction. Throughout the project, the team went above and beyond to create a positive experience for those around them by installing covered walkways; organizing social events for the local community to discuss the project; installing a project signboard to inform neighbors of what they should expect to see, hear, and smell; and providing noise-cancelling headphones to residents of a nearby nonprofit organization.
“DDOMAL was born of a mission to improve the lives of patients,” said Patrick Poisson, Executive Vice President, Technical Operations, United Therapeutics. “Against all odds, the DDOMAL team showed an unparalleled commitment to getting Unituxin into production and to market, building strong local relationships, and executing the project to an outstanding level. It is an exceptional example of how a valiant team effort across the board can lead to an innovative and well-functioning pharma manufacturing facility that respects all stakeholders and quickly produces medicine that saves children’s lives.”
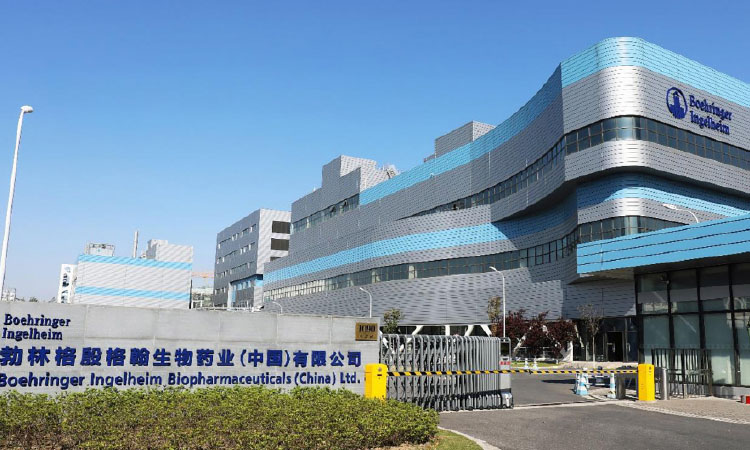
Honorable Mention: Boehringer Ingelheim Biopharmaceuticals China Ltd.
Boehringer Ingelheim’s commitment to bringing lifesaving medication to China to meet increasing needs included not just building a new facility but also working with local government to change regulations. In 2013, Boehringer Ingelheim began supporting efforts by the China National Medical Products Administration to revise relevant regulations. After years of hard work and diplomacy, China’s Standing Committee of the National People’s Congress approved in 2019 a significant revision of the Drug Administration Law pertaining to the Marketing Authorization Holder (MAH) system. The new system makes it easier for drug developers to bring new drugs to market, while increasing their responsibility to ensure the safety of those drugs. In addition to its efforts to reform Chinese regulations, Boehringer Ingelheim built in Shanghai a modern facility that incorporates environmentally friendly systems and can be expanded to meet patient, business, and market needs.
The OASIS GMP facility, which is located directly in the heart of Zhangjiang Hi-Tech Park, is set up in a modular approach: module 1 covers first bio-reactors, including an auto-isolator fill-and-finish line, and module 2 has an expansion option. The entire production is based on single-use equipment to be put together following a toolbox concept, which allows for various combinations and can cope with the requirements of different processes. The bioreactors and vessels are connected through a flexible tube system, instead of pipes, offering options for putting together equipment independent of hardware installations. Additionally, the site is the only biopharmaceutical site of a multinational company on the Chinese market to offer contract manufacturing that meets global standards.
“We were very proud to become the first company starting commercial biopharmaceutical manufacturing under the MAH model in China,” said Jiali Luo, General Manager and Site Head of Boehringer Ingelheim Biopharmaceuticals China. “The trial project was smoothly conducted and has now proven successful. The newly established model can be of great benefit for the Chinese healthcare system and can provide Chinese patients broader access to more innovative medicines.”
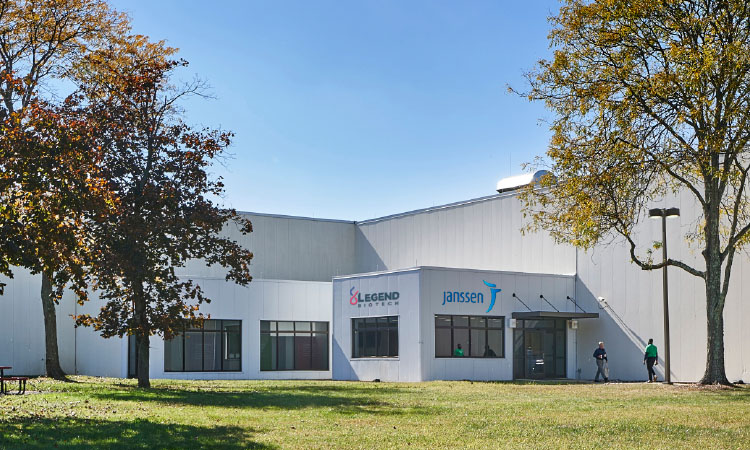
Honorable Mention: Janssen Pharmaceutical Companies of Johnson & Johnson and Legend Biotech, USA Inc.
Advancing a Next-Generation Cell Therapy for Blood Cancer
With the current treatment options on the market, the five-year survival rate for patients with multiple myeloma is approximately 50%. Although treatment may result in remission, most patients will relapse and there is currently no cure for the blood cancer. However, an innovative chimeric antigen receptor T-cell (CAR-T) therapy targeting B-cell maturation antigen, currently in global clinical development by Janssen Pharmaceutical Companies and Legend Biotech USA, is offering hope to patients with multiple myeloma.
CAR-T therapy uses the patient’s own immune system to identify and attack tumor cells. After collecting the patient’s white blood cells, the T-cells are genetically engineered to produce chimeric antigen receptors on their surface, which enables the T-cells to recognize tumor cells. The reengineered CAR-T cells are expanded and formulated in a cleanroom environment before being returned to the patient for infusion. The CAR-T cells attack the cancer and stimulate the immune system to recognize the cancer cells if they return.
Speed of implementation was the driver for the project to establish a CAR-T clinical manufacturing facility in Raritan, New Jersey, as Janssen and Legend Biotech wanted to provide this innovative therapy to patients as soon as possible with no compromise to the companies’ standards for quality. Two project design teams, one to design the cleanroom PODs and the other to design the stick-built modular facility, worked closely together to ensure both elements came together seamlessly. They used hybrid construction and a unique combination of on- and off-site modular construction to help them meet their timeline and were able to achieve mechanical completion in just nine months. At the conclusion of the project, a “hope bell” was installed within the open meeting space. Each week, employees ring it for each dose of CAR-T therapy being provided to a patient.
“Initially, the sound of the bell was rare. As a result of tireless efforts to develop personalized treatments for more patients, this bell ringing has become a weekly ritualized event where it is rung numerous times, and each time with deep, personal meaning for everyone involved,” said Eric Niebling, Vice President, Advanced Therapies, for Jannsen. “The sound of the hope bell is a celebration for every patient and for every employee who has worked passionately to develop each treatment.”
Special Section: 2020 ISPE Annual Meeting & Expo
2020 ISPE Annual Meeting & Expo: Driving the Future of Pharma
The 2020 ISPE Annual Meeting & Expo will be ISPE’s first completely virtual Annual Meeting. As always, there will be great learning and networking opportunities—in fact, the digital format offers greater flexibility for attendees.