ISPE Pharma 4.0™ SIG & Its Working Groups

The ISPE Pharma 4.0™ Special Interest Group (SIG) launched in 2015 to provide a road map for new challenges of digitalization, Industry 4.0, and the smart factory. The Special Interest Group addresses how pharmaceutical industry stakeholders, including regulatory authorities, can achieve benefits from Pharma 4.0™ initiatives.
The Pharma 4.0™ Special Interest Group has established cross-functional working groups to collaborate in a matrix across all stakeholders in development, quality, manufacturing, engineering, and IT, as well as contractors, technical solution providers, consultants, and operators. The goal is to work on specific topics while engaging all stakeholders and breaking down industry silos.
The lack of cross-cultural thinking, working and acting in silos, and the lack of standardized and harmonized integration were identified as the biggest hurdles to establishing digitalization, which is the systematic digitization of the organization’s business processes by applying a digital transformation process. Overcoming these hurdles through the coordinated efforts of the Special Interest Group and its working groups enables data-driven and transparent decision-making as the key benefit for the organizations that implement Pharma 4.0™. The transparency needed to accomplish this can be uncomfortable for some stakeholders and involves shifting areas of responsibilities, so the SIG and its working groups take an interdisciplinary and cross-functional approach to create awareness, understanding, and respect. The goals are to engage the overall ISPE community and to contribute to ISPE projects with participation from all Communities of Practice (CoPs). Figure 1 shows the SIG’s mission statement.
Pharmo 4.0™ History
The idea of the Pharma 4.0™ Special Interest Group was born with ideas written on a napkin in a small restaurant in Basel, Switzerland, in 2015, as Christian Wölbeling and fellow ISPE D/A/CH Affiliate Board Member Marcel Staudt were discussing fundamental problems of automation, integration, and validation in commercial manufacturing. They identified harmonized integration of the shop floor equipment interfaces as one of the obvious and largest benefits of holistic digitalization, but they also understood that all stakeholders—the pharma industry, equipment suppliers, and software partners—needed to collaborate to create an efficient and effective integration scenario to successfully apply Industry 4.0 concepts being used by other industries.
It was also clear that the control strategy defined by ICH Q101 needs a holistic approach and holistic data-driven strategy along the ICH product life cycle. This holistic view derives from material sourcing and development via tech transfer up to commercial manufacturing. The perspective is patient-centric and spans the complete product life cycle, from the development supply chain to the production supply chain, the distribution supply chain, and, ultimately, the patient or customer. These three supply chains need a sound product and life-cycle data concept based on a clear data integrity by design-based approach as defined by the GAMP® RDI Good Practice Guide: Data Integrity by Design.2
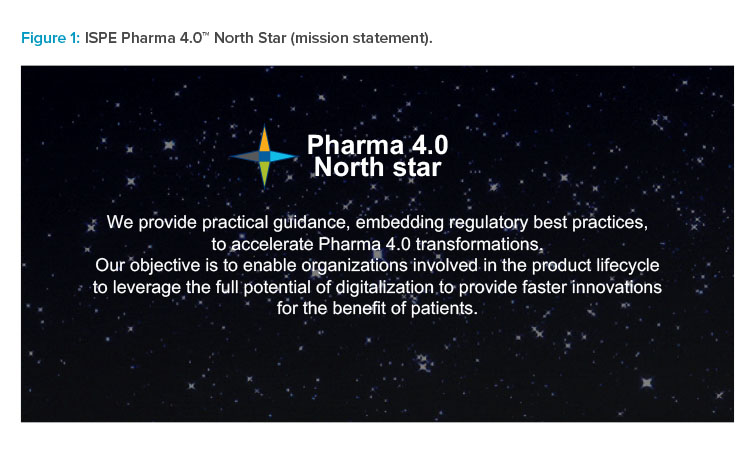
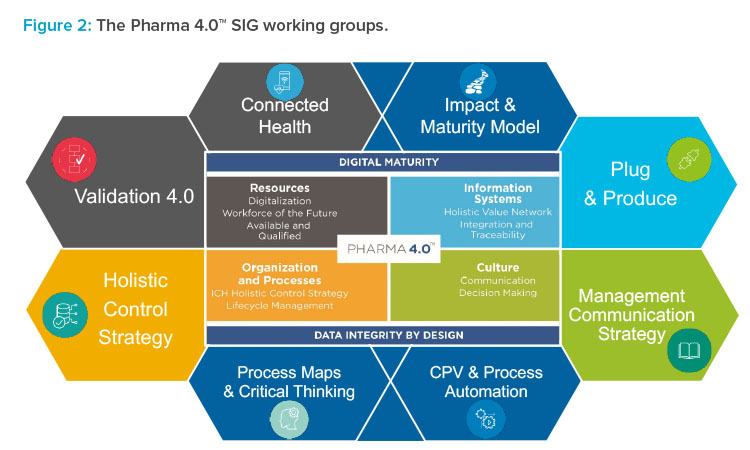
Working Groups
The following sections introduce the working groups within the Pharma 4.0™ Special Interest Group. Figure 2 lists all of the working groups.
Plug & Produce
Wolfgang Dedden, Klaus Sauermann, and Christian Wölbeling started the first Pharma 4.0™ working group, Plug & Produce, in 2017. Early on, Special Interest Group members identified harmonized integration of equipment interfaces from the shop floor up to the enterprise resource planning system and across the whole organization as one of the largest benefits to digitalization for pharma and biopharma companies.
In March 2020, leadership for Plug & Produce transitioned to Josef Trapl and Wolfgang Winter. Since then, the working group has restructured, re-fined its vision and mission (Figure 3), and recruited new participants.
The working group’s vision is to achieve a global Plug & Produce standard that enables end-to-end integration through vendor-agnostic connectivity, interoperability, and big data analytics. The mission is to define, in collaboration with other organizations, the user- and data-centered methodology for vendor-agnostic system integration, building on best practices, frameworks, and existing and emerging standards for interoperability. The key contributions and focus of the Plug & Produce working group are (a) the pharma-specific requirements that will make Industry 4.0 applicable across pharma and biopharma companies, and (b) being the guiding industry coalition to define Pharma 4.0™ best practices in close collaboration and alignment with other relevant consortia.
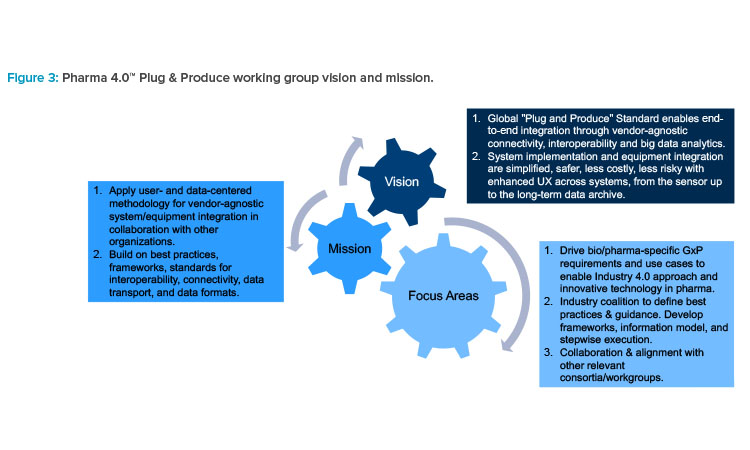
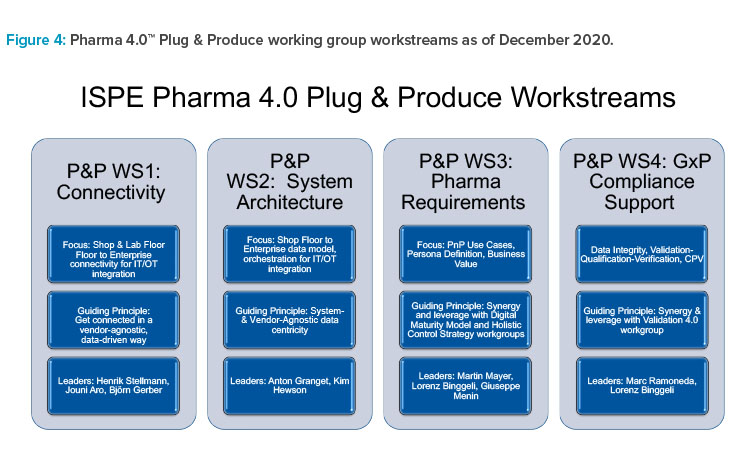
As of December 2020, the Plug & Produce working group had about 40 active members from pharma/biopharma, academia, consulting, and suppliers of automation and engineering, package machines, software, and analytical lab systems. The working group reorganized into four interactive, interdisciplinary agile workstreams (Figure 3).
Each Plug & Produce workstream drives a specific proof-of-concept (PoC) project for a specific equipment class to demonstrate the viability of the plug and produce approach. The PoC projects are chosen to enable higher-level use cases, including, but not limited to, drop-in (plug-in) deployment of prequalified equipment, system-wide audit trail review, and predictive prevention of quality-relevant incidents.
For further information, contact the working group leaders: Josef Trapl and Wolfgang Winter
Management Communication
The Management Communication working group launched during the 2018 ISPE Europe Conference in Rome to help key decision makers in middle and top management better understand how Pharma 4.0™ can create the appropriate conditions to achieve successful 4.0 projects. The group’s aim as de-fined in the working group charter is to “define, structure, and execute a compelling, lean, and management-focused communication strategy to promote Pharma 4.0™ initiatives” so that technical information is more understandable at the manager level.
The working group’s goals are to orchestrate communication among the Special Interest Group’s working groups; be available and open to non-ISPE members to show-case Pharma 4.0™ benefits; promote the adoption of innovative technologies and foster Pharma 4.0™ awareness; provide relevant business value and key performance indicators using communications suitable to the target audience; and share industry best practices and real-life use cases.
The working group uses LinkedIn to provide a larger professional audience with news, updates, and opinions. The ISPE Pharma 4.0™ LinkedIn group currently has more than 300 members.
The group also writes articles and creates presentations to highlight management-relevant aspects of Pharma 4.0™ and explain 4.0-enabling technologies to non-technical audiences. It issues awards to promote excellence in 4.0 projects, and it conducts periodic surveys to monitor the status of Pharma 4.0™ perceptions, challenges, and projects. The most recent survey had 10 questions and collected over 400 responses from around the world. Findings from the most recent survey were presented during the virtual ISPE Pharma 4.0™ Conference in 2020.
Ten volunteers are now active in this working group. For further information, contact the working group leaders: Davide Smaldone and Teresa Minero
Holistic Control Strategy
The Holistic Control Strategy working group supports a wider scope of traditional control strategies with the goal to have real-time information and allow data-based decisions. This objective is central to digitalization of data and Pharma 4.0™.
The working group first worked on a definition for holistic control strategy and described how it extended the scope of the traditional product quality control strategy defined in ICH Q8.3 The wider scope encompasses the full value network of pharmaceutical operations, covering the upstream as well as the downstream supply chain. It goes beyond the processes for which GMP rules are defined by also covering relevant safety topics, such as impurities from starting materials to the source of origin, and the market environment of a pharmaceutical product, such as its performance in the market (effectiveness of the product and market acceptance). The Holistic Control Strategy working group will also focus on issues related to market availability of drugs, such as installing early warning indicators for drug shortages and helping with anti-counterfeiting initiatives. As an essential tool, quality risk management according to ICH Q94 is recommended.
As a next step, the working group will focus on how to monitor holistic control strategies, including structural questions and principles to address before discussing the technical feasibility of implementation. For instance, who will need which information, when will they need it, and, most importantly, why? Another question concerns the appropriate roles of humans and machines/computers in the data-based decision-making process.
Further questions deal with regulatory oversight: What types of interfaces can be used between manufacturers and regulators, and can they be used for remote inspections? How can computers play a role in organizing quality oversight? How should a quality system operate when a holistic control strategy is implemented? Which level of “digital maturity” is needed to implement a holistic control strategy? Can a holistic control strategy be implemented through a staggered approach or used as a tool to fix weaknesses in an organization or product? Or must it be the starting point?
For further information, contact the working group leaders: Nuha Al-Hafez and Lothar Hartmann
Validation 4.0
Launched in 2019, the Validation 4.0 working group works with GAMP® Special Interest Groups, other ISPE groups, including CoPs, and the industry at large to develop and publish validation guidance for the pharma and biotech industry to maximize digital innovation while maintaining acceptable control and compliance.
The ultimate goal is to define a holistic validation approach to enable the pharmaceutical and other life sciences industries to realize the Pharma 4.0™ vision and support ongoing adoption of digital innovations in a controlled way. The goal is being achieved by describing and illustrating an approach that incorporates all aspects of validation in an integrated way and shifting the validation focus toward control strategies focused on process and data risk mitigation. Control of data risks means the process and products produced can be controlled.
The working group is seeking to use process and data flow knowledge from the full product life cycle, starting with data from product discovery and product and process development through postmarket activities. Using continuous flow data from all inputs can help verify in real-time that control strategies are in place and effective, as required by ICH Q12.5 This approach is based on many quality by design (ICH Q8) principles for product and process knowledge, using a risk management (ICH Q9) framework for risk assessment and risk control through three stages of validation.3, 4
The working group is also seeking outlets such as instructional, educational, and collaborative forums for engaging with the industry. The working group aims to bring together the various aspects of validation in a holistic view and help focus validation where value is continuously added, rather than in traditional and mostly serial approaches.
For further information, contact the working group leaders: Michelle Vuolo and Tony Margetts
Impact & Maturity Model
The Impact & Maturity working group is focused on how to identify barriers to Pharma 4.0™. As noted earlier, on the journey toward Pharma 4.0™, several barriers can significantly slow or even disrupt the progress of implementation. They exist in each element and maturity level of the Pharma 4.0™ model, and in each organizational level. Identifying these barriers as early as possible helps organizations build strategies to avoid or to address them.
For example, in the pharma industry, the huge amount of data collected by manufacturing and quality control equipment and within quality systems is underutilized. Analyzing all existing data and predicting potential risks will allow the industry to bring new products to the market faster and improve stability of the supply chain for marketed products.
For further information, contact the working group leaders: Manuela Gottschall, Jens Solsbacher, and Thomas Lee Johnson
Connected Health
The Connected Health working group advocates using the socio-technical model developed at the Tavistock Institute, London, for optimization of healthcare management and delivery of drug products, combination products, in vitro diagnostics, and medical devices, among other products. The socio-technical model marries people and technology to produce better outcomes. It focuses on how technology can advance healthcare services and collect feedback from patients throughout the product life cycle.
With the increase in technology and the greater accessibility of data to the general public and industry/healthcare systems and payors alike, bringing together these aspects of a product life cycle can help provide better patient outcomes.
This working group was formed to consolidate elements across the GxPs and incorporate aspects of real-world evidence and data to provide insights to facilitate improving patient experiences and outcomes. Although in its infancy, the Connected Health working group aims to provide guidance for digitalized healthcare management across the value network.
Colleagues joining the group will bring additional expertise across the GxP landscape to “connect the dots.” The Connected Health team looks forward to strengthening their team and providing first points for discussion in the coming year.
For further information, contact the working group leaders: Rebecca Stanbrook and Nuha Al-Hafez
Process Maps and Critical Thinking
The Process (Data) Maps and Critical Thinking working group is defining guidance for using critical thinking to create process and data maps. The objective is to harmonize and optimize information flows supporting attributable, legible, contemporaneous, original, and accurate (ALCOA) data, the data life cycle, and other principles that fit the integrated environments of the Pharma 4.0™ world.
Pharma companies are struggling with data exchange because of a lack of harmonized and consistent information flow supporting regulatory needs. Different standards and data formats require large amounts of resources (time, money) to provision, clean, and use the data in a fully useful way. This hinders the full realization of digital maturity and Pharma 4.0™ implementation.
The working group seeks to enable quality and data integrity by design by applying known standards (such as ICH Q8–Q10 and Q12),1, 3, 4,5 starting with current state processes and data. The group will define standardized ways of applying critical thinking with the target output to redesign and opti-mize the future state of process flows, data flows, and interfaces to harmonize data formats, reduce the amount of data, focus on relevant data, avoid media breaks, improve data availability, and implement ALCOA and findability, accessibility, interoperability, and reuse (FAIR) principles. The Reference Architectural Model Industrie 4.0 (RAMI 4.0) model is taken into consideration in critical thinking, with the intent to standardize what type of data is used and where it is visible.
For further information, contact the working group leaders: Emmie Heeren and Michelle Vuolo
CPV & Process Automation
The working group dedicated to continued process verification (CPV) and process automation was set up in 2020. Its 17 active members from pharmaceutical companies and technology providers offer multidisciplinary insights and experiences from engineering, IT, and automation, quality, and regulation perspectives. With this multidisciplinary approach, three working lines have been defined, each one assigned to a specific team.
CPV Subgroup
With 10 active members, this subgroup works on the application of the Pharma 4.0™ concept to ongoing/continued process verification, or continuous verification of the process. Specifically, the team will explore possibilities of integrating all the necessary data sources to have real-time process information, as well as standardizing the automated statistical treatment of data to simplify generation of CPV reports and evidence that processes are in a state of control. The group worked on a survey on current CPV practices, and the results will be published by ISPE in 2021.
Artificial Intelligence (AI) Use Case 1
Three active members are working on a real use case at mABxience (Leon, Spain). The use case involves applying machine learning to assess whether data generated by a water for injection plant can be effectively used for prescriptive maintenance. Specifically, the aim is to know in advance when the plant needs to be maintained based on the model-predictive indications (condition-based maintenance). A PoC was completed in 2020. Further mod-el-building and qualification of the results has been scheduled for 2021.
Artificial Intelligence Use Case 2
Four active members are working on a real use case at Almirall (Barcelona, Spain). In this use case, machine learning is being applied to data generated by a drying process, with the aim of optimizing energy efficiency and cycle times, among other goals, keeping a high-quality level. A PoC was completed in 2020, and industrialization and extension of the model to similar equipment has been scheduled for 2021.
For further information on the working group, contact its leaders: Alicia Tebar and Miquel Romero Obón
For More Information
The Pharma 4.0™ Special Interest Group working groups are always looking for new volunteers. The only prerequisites are ISPE membership and technical and/or managerial expertise to support the goals of the Special Interest Group. Contact the working group leads identified above.
ISPE Pharma 4.0™ Working Group Leads

