Holistic Control Strategy: From ICH Quality Guidelines to Pharma 4.0™

The fourth Industrial Revolution (also known as Industry 4.0) is the era of smart machines, storage systems, and production plants that can autonomously exchange information, trigger actions, and control operations free of any human intervention. To ensure future success in the delivery of therapeutic medicines to patients, it is imperative that the pharmaceutical industry move deeper into the fourth Industrial Revolution and embrace increasingly advanced levels of digital maturity through Pharma 4.0™. This article discusses how holistic control strategy can be a bridge from established industry guidelines (ICH Q8–Q12) to the Pharma 4.0™ operating model.
Pharma 4.0™ responds specifically to the question, “How does the pharmaceutical industry embrace and apply Industry 4.0?” The objective is to improve quality and efficiency and make compliance an automatic and seamless part of the quality system. Holistic control strategy is a key to achieving this goal because the holistic approach uses digitization (converting information into a computer-readable format) to enable real-time evaluation of the entire value network and optimize management decisions.
What Is Holistic Control Strategy?
Holistic control strategy1 has a wider focus than the manufacturing control strategy described in ICH Q8, Q10, and Q112, 3, 4 or the Pharmaceutical Inspection Convention/Pharmaceutical Inspection Co-operation Scheme’s “Good Practices for Computerised Systems in Regulated ‘GxP’ Environments.”5 ICH Q103 defines “control strategy” as a strategy to ensure that the final product will meet the acceptance criteria of the approved product for patient safety, product efficacy, and quality. The product control strategy controls what is critical to ensure product quality, such as critical quality attributes (CQAs), critical process parameters (CPPs), and critical material attributes (CMAs).2, 4 However, to maximize the advantages of connectivity, digitization, monitoring, control, and real-time data-driven decisions across the entire value network—including pharmaceutical operations, planning, sourcing, patient feedback, regulator feedback, and market feedback—organizations must move from product control strategy to holistic oversight of product quality and performance.
“Holistic” means the complete view of something, including all influences and all possible contexts. Holism in science is an approach to research that emphasizes the study of complex systems. Systems are approached as coherent wholes, whose component parts are best understood in context and in relation to one another and to the whole.
Thus, holistic control strategy incorporates GMP and Good Distribution Practices (GDP) and defines the controls from a holistic perspective that will ensure product quality and clinical performance, product availability, and product improvement. These controls include material supply controls beginning with the original sources, safety and environmental controls, product distribution controls, and patient and regulatory feedback necessary to respond to quality, supply demands, and life-cycle management.
Such a holistic overview of the control strategy can only be established if the supply network or chain is well understood and digitized so relevant data can be exchanged among the different parts of the supply network. Therefore, holistic control strategy is a systematic and controlled approach for generating, monitoring, controlling, and managing data throughout the life-cycle management of a product. It involves the identification of factors critical to the success of the Pharma 4.0™ operating model, such as organizational structure, resources, culture and information systems, understanding of company internal processes (e.g., development, manufacturing, and business), and awareness of in-house knowledge needed to perform the business.
Holistic control strategy enables data-based (electronic) decisions on all aspects of the pharmaceutical product life cycle while maintaining product quality and efficacy for the patient. Furthermore, holistic control strategy includes performance control of product life-cycle management regarding regulatory, operations, and distribution. Its scope covers supply chain and market surveillance issues, including drug demand, drug shortages, and clinically relevant activities of change management.
An organization can achieve a holistic control strategy when the appropriate, desired digital maturity level is achieved across the organization. In a holistic approach driven by digitization, a pharmaceutical quality system (PQS) becomes more effective and more efficient by creating and using real-time information for data-based decision-making.
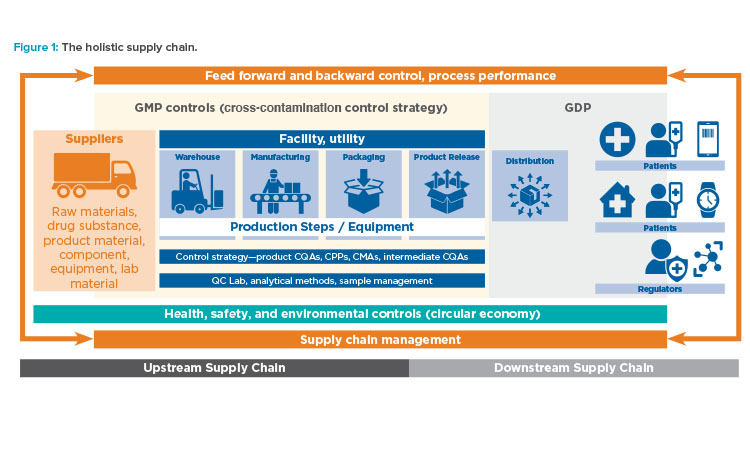
Holistic Supply Chain
As noted, the holistic control strategy includes managing the entire supply chain, which encompasses both the upstream and downstream supply chains (Figure 1).
Upstream Supply Chain
The upstream supply chain links suppliers, their suppliers, raw materials, and manufacturing of the finished product. Drug safety, impurities in starting materials up to the original source of material, detection of unknown impurities, and medical devices and their constituents are some matters to consider when mapping the upstream supply chain for a holistic control strategy. Therefore, the suppliers of all materials used for manufacturing the product, including drug substances, excipients, single-use equipment, filters, chemicals for analytical methods, packaging material, storage containers, and so on, as well as the suppliers of the suppliers, must be covered by the control strategy for the upstream supply chain.
An example of why the upstream supply chain is relevant to the control strategy is the manufacture of a raw or starting material. Although the term “raw material” might imply otherwise, the material must be produced, and in some cases, production occurs in a non-GMP environment.6 Pharmaceutical manufacturers must therefore strategically anticipate how a change in the raw material manufacturing process might impact the raw materials they buy. Many drug shortage issues have been caused when the supplier, or the supplier’s supplier, changes the production process in a way that affects raw material properties, without informing customers in the pharmaceutical industry about this change.
Supply interruptions for long-lead materials, such as resins, and the safety implications of raw materials in relation to manufactured materials are other examples of high-risk concerns in the upstream supply chain. Also, the outsourcing of many pharmaceutical processes or subprocesses in the upstream supply chain to contract manufacturing organizations (CMOs) makes the supply network very complex. If the holistic control strategy accounts for this complex upstream supply chain, the impact of a change in any of the involved steps on the manufacture of the final product can be evaluated and managed in real-time.
Downstream Supply Chain
The holistic control strategy’s objective for the downstream supply chain is to link manufactured products, distribution, and end users (patients) in a safe manner to ensure product availability, minimize the risk of product mix-up, avoid interruption of the supply chain by falsified medicines, and control distribution to the end of the product life cycle, including environmentally safe destruction of excess products and their delivery systems.
The downstream supply chain incorporates storage and distribution, including product protection and traceability to wholesale outlets, health service providers, regulatory authorities, and, in some cases, patients directly. If the product is a connected health product, the downstream supply chain will also cover connectivity of patient data with treatment response and decisions for healthcare management. This connected health focus is wider than GDP and contributes to product life-cycle management, such as next-generation formulation based on data from the entire value network.
The holistic control strategy links the complex downstream supply chain back to manufacturing, so feedback from patients, regulators (e.g., quality issues, inspections, assessments), healthcare providers, patient associations, and payers can be used by the manufacturer to continually improve the process and control strategy, plan supplies based on real-time demand, and enable proper product life-cycle management activities in line with ICH Q12.7 For example, in personalized medicine, information about patient responses can be used for product and process improvement, or even for defining the treatment and product demand.
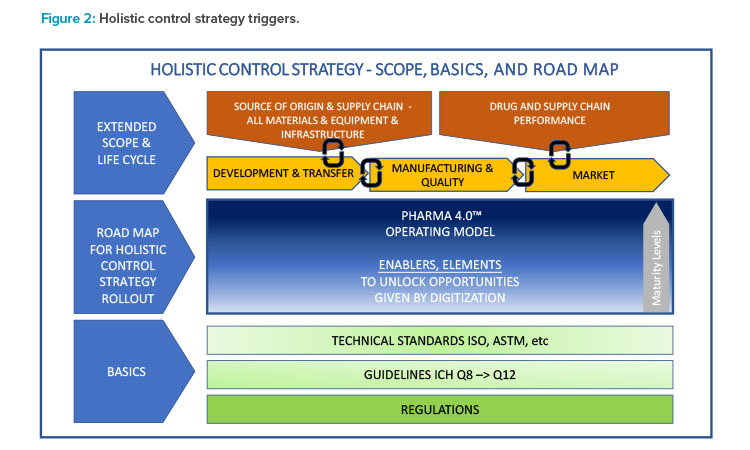
Designing a Holistic Control Strategy
The design of a holistic control strategy (see Figure 2) requires a monitoring, control, and decision-making system to address key questions such as:
- Who needs what information, when, and why?
- How can regulators be enabled to make effective and efficient oversight of such a complex system?
- How can decision-makers be supported? For example, in the future, what types of decision-making can we delegate to computers, and where will human accountability for decisions start? Will regulators ever authorize computers to make decisions without human interference?
The ICH quality guidelines serve as a starting point and the Pharma 4.0™ operating model (Figure 3) is a framework for designing the holistic control strategy.
ICH Quality Guidelines
The ICH quality guidelines define science- and risk-based principles. Of particular note, ICH Q82 and Q11 4 focus on pharmaceutical drug product and drug substance development, ICH Q103 addresses the PQS, and ICH Q127 covers product life-cycle management. Together, these guidelines can be the foundation for a new, digitization-enabled industrial control strategy with a wider scope. Additionally, when establishing a holistic control strategy, ICH Q98 remains a helpful method for evaluating the associated risks, determining the level of formality and documentation commensurate with the level of risk, and supporting risk-based decisions. The overall goal is to come closer to real-time and data-based decisions.
The holistic control strategy helps implement the science- and risk-based principles effectively by using digitized data in a transparent environment. Digitization allows organizations to better apply the approaches of the ICH guidelines mentioned here.
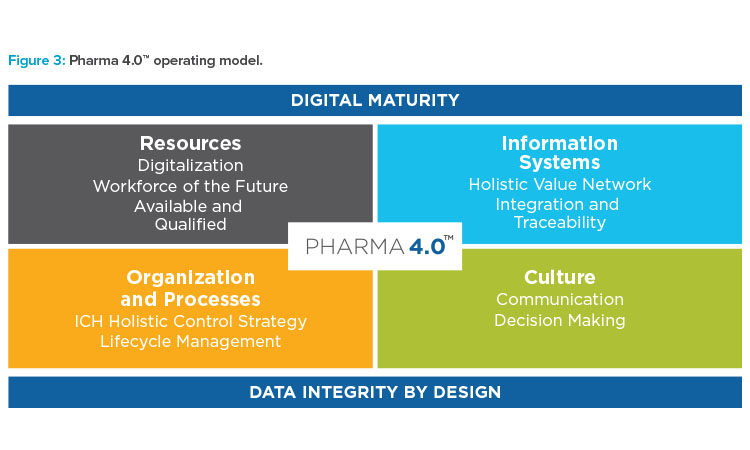
Pharma 4.0™ Operating Model
The “how to” steps of holistic control strategy are embedded in the Pharma 4.0™ operating model (Figure 3). In the following sections of the article, the individual elements of this model—resources, information systems, organization and processes, and culture—and related success factors are discussed.
Creating an overall picture of trigger points for a holistic control strategy helps strategists visualize connection points and synergies, thereby creating transparency for all stakeholders involved. This enterprise view may lead to “blueprints for technology” or dosage form–specific holistic control strategy templates that help build a common understanding and provide insight about why the organization is doing what it is doing in the area of product development. Ultimately, these efforts will aid the organization in achieving an integrated-network mindset that may further advance organization-wide digital maturity.
Resources
When applying the Pharma 4.0™ operating model to holistic control strategy, cross-functional, multiskilled teams considering the entire scope of the product life cycle are essential. In a digitized environment, the human element remains a key success factor.
For product development, qualified cross-functional teams should be defined and made available from the beginning of the life cycle. The optimal makeup of such teams will include experts in the following areas: development, manufacturing, quality, engineering, regulatory, supply chain, digital technology, connected health, statistics, market feedback, and sales. Experts in other areas should be added to the team as appropriate.
The primary task of this cross-functional team is to holistically define the scope and trigger points for performance control of a pharmaceutical product, as shown in Figure 2. A major benefit of having a cross-functional team is team members can provide different perspectives and thoughts on possible risks involved with a process. It is important to assemble this team and identify the roles and responsibilities of team members early in the risk management process.
The commercial manufacturing process needs to have performance attributes during the commercial life cycle, including feedback loops. Those attributes should be considered as early as possible. The needs of patients and customers should be transparently integrated into the performance attributes.
Knowledge management and systems should be designed to ensure employees have information digitally available at the right time, at the right quality, and as completely as required by the purpose, in the right system for decision-making processes.
It might be useful to identify product sponsors who have a holistic view of product development and the technology landscape, leadership experience, and communication skills to negotiate with key stakeholders during development and life-cycle progression.
The provision and distribution of resources within a company are ensured through management commitment. For the PQS, it is extremely important to distribute available resources across functions to ensure all necessary tasks can be performed in compliance with regulations. Highly qualified personnel are needed in all areas, and the following must also be provided:
- Sufficient human resources
- Enough money to fund performance of the assigned tasks
- Necessary infrastructure
- Sufficient time to accomplish the work
- Priorities aligned with quality risk management (ICH Q9) principles8 and knowledge management
As noted earlier, in a digitized environment, some aspects of the PQS will be taken over by computerized systems, making the interface between machines and people crucial. To carry out activities and decisions in the desired way, the computerized systems must be fed the right information by humans. Therefore, a holistic control strategy should carefully consider how this will work.
For product life-cycle management, providing a framework to facilitate the management of post-approval chemistry, manufacturing, and controls (CMC) changes in a more predictable and efficient manner should result in a win-win situation for both industry and regulatory authorities. For example, as a part of the holistic control strategy, different approaches can be used alone, or in combination, to identify established conditions (ECs) for manufacturing processes, as defined by ICH Q12.7 The performance-based approach to identify established conditions is only possible after the organization invests in resources to develop data-based models, preferably during R&D for new products and in commercial operations for legacy products.
Organization and Processes
Integrated end-to-end processes across the organization, without silos, are needed to enable the creation of transparent and effective workflows. Business processes are subject to the holistic control strategy, and they need owners with clearly defined holistic roles and responsibilities to ensure that all parties involved collaborate and are aligned with common goals and targets.
Integrated (computerized) systems are connected to these business processes. Therefore, the business owner’s responsibility should be flexible and allow easy and reliable change management to accelerate development and time to market, in accordance with quality risk management principles, such as the ultimate priority of patient health.
Because systems are subject to the holistic control strategy, it is important to have proper input from the end-users and stakeholders of the systems within the strategy’s scope. The first step is to determine the needs of the end-users throughout the organization early in the development stage of the process. Additionally, the organization should implement a “sandbox” platform where cross-functional users of the system can provide input into both the design and relevant outputs from the system to ensure appropriate data-based decision-making at all levels of the organization.
For example, the business processes and integrated computerized systems should facilitate proper knowledge transfer between development and commercial operations because holistic control strategy starts with having the appropriate information available at all steps across the value network. To institute a lean digitalized environment, the documentation and approval requirements should be standardized and minimized as much as possible based on the related risk for systems and/or equipment of similar types.
Access to high-quality data is a key success factor in product development, and robust and well-run data management is required to consistently deliver high-quality products throughout the product life cycle. It is essential for the organization to have optimal systems to collect, store, clean, and sort data. Wherever possible, the data management should be automated to avoid the risk of variance or errors related to human interventions.
The organization should also eliminate “automation islands” (automated systems that can’t communicate with other systems) wherever possible. When automation islands are absolutely needed, strategists will need to determine how to manage their operations within the integrated digitized environment. If a process requires human intervention, the strategy should clearly establish clear and standardized data creation principles so that information may be leveraged easily, via automation wherever possible, throughout a product’s life cycle.
For all these organization and process measures, an integrated and automated self-inspection process can be supportive. Additionally, it may be prudent to define a business process for establishing a product’s holistic control strategy itself. A critical element of this business process is collecting, consolidating, and making available incoming information and then driving data-based decision-making at all levels of the organization.
Overall, the holistic control strategy will include the product view, the process view, and the systems view. All work is reflected in data.
As an organization advances its digitized operations, most of the data used during a management review of products, processes, and systems will be-come compiled by computerized systems. Data can be prepared and made available very quickly, which will allow senior management to react in a timely manner and make data-based decisions in a transparent, logical, and real-time way.
All these activities are guided by the application of best practices in quality risk management and knowledge management. These techniques are necessary to assess the robustness of the created data that becomes the basis for making further decisions, made today by managers and in the future by machines. These aspects will also be part of a holistic control strategy.
In product life-cycle management, the details of established conditions and the associated reporting category will depend on the extent to which the company can apply knowledge from product and process understanding (i.e., development and experience accumulated throughout the product life cycle) to manage risks to product quality. To enable a holistic control strategy, the organization should transition from a parameter-based approach to a performance-based approach for identifying established conditions.
Many postapproval CMC changes could effectively be managed by the company’s PQS, reducing the need for extensive regulatory oversight prior to implementation. However, this requires a mature PQS to accommodate such changes. Organizations can benefit from using an automated and standardized risk-based process to determine which changes could be managed through PQS and which changes would require regulatory submissions.
Information Systems
Similar to the organization and business processes, the requirements for information systems, as part of the organization’s computerized systems, should be designed prospectively and aligned with process and digitization requirements to enable an optimal digitalized environment. In this environment, information systems will capture experimental, study, and analytical data in addition to process information, and sophisticated information systems will be responsible for automating most PQS maintenance. Also, timelines will be adhered to as programmed; documents can be automatically updated according to the available data of the entire computerized system; manual documentation will be reduced to a minimum; and information systems can be programmed by humans to make some decisions on their own. All of this will lead to a higher degree of compliance with regulations and accelerate processes.
Additionally, a new concept of connected databases and computerized systems will address questions regarding who needs what data, when, and why. This connectedness is needed to structure the big data management capabilities of computerized systems used in quality systems of the future.
During the early stages of information system development, IT stakeholders should help evaluate how data will be stored, reviewed, backed up, and retrieved throughout the life cycle of the system. A risk evaluation early in the process should be used to identify and understand the critical data points to capture and review to make product quality–based decisions. Subsequently, the critical data should be readily available and accessible to all appropriate stakeholders in the organization; this demonstrates an appropriate level of digital maturity.
Furthermore, technical processes should be designed to have the capability of a “digital twin” as early as possible, reflecting the product and process control strategy. Input, output, and controls, as defined by the control strategy, should be digitized through a qualified interface embedded in a valid (technical) process. All of the organization’s standard operating procedures (SOPs) should be digitized and available online at all times. Also, a system architecture connecting all functions relevant for the product in development, including a master data management architecture, should be available.
In an organization that has optimally advanced along the digital maturity spectrum, the collective (product and process) data platform should be readily available and accessible to all appropriate experts. From the technology perspective, a major strategic task is determining, in a holistic way, what types of systems, platforms, and interfaces are required to connect all engaged functions and to collect, store, clean, and prepare the process and product data. This will be a hallmark of a state-of-the-art holistic control strategy. A common set of user requirements and enterprise functionality, including interface standards, might convince industry stakeholders of the value of developing such systems.
Among the systems typically included in a manufacturing facility are the overall process control system, site data historian, manufacturing execution system, laboratory information management system, enterprise resource planning system, and computerized maintenance management systems. These systems typically require some level of integration. Building information management systems (e.g., systems using environmental monitoring data, room classification systems), electronic laboratory notebooks, and digitized SOPs are additional systems that can be included the integration strategy. Integration among all systems is very important for achieving the desired level of digital maturity.
Effective integration among systems has multiple benefits. It allows operators and users to have access in an organized manner to data from various systems, and it permits regulators to access data as required for review, with remote access a possible option. Such external engagement would be de-fined by established protocols based on defined criteria or content readily available to
regulators through routine means (electronic common technical documents, PQS and annual product quality review documents, etc.). In these ways, system integration may also help accelerate the submission approval process by providing transparent access to application data during a regulatory preapproval inspection.
Culture
Though digitization creates new opportunities for implementing a holistic control strategy, an organization cannot achieve its holistic control strategy goals if the cultural environment is inadequate. Specifically, creating a culture of transparency and trust within an organization is a key aspect of implementing a holistic control strategy.
In general, cultural changes are driven from the top down. Breaking down organizational silos is a critical part of the cultural change needed to support a holistic control strategy, and this is best accomplished with support and endorsement from senior-level leadership.
When operations and systems are digitized, a company no longer needs classical multi-level departments. Instead, it needs trained and multi-skilled employees who can function as experts and decision-makers in a process-oriented lean organization. For example, in the future, the quality unit will no longer need staff to review batch records because this work will be done electronically. However, the quality unit will need workers with high levels of statistical competency to evaluate and assess the robustness and reliability of available data. Furthermore, these employees will need to understand the process and take ownership of it.
Another cultural change required for a holistic control strategy implementation is greater transparency between organizations and regulators. Sup-ported by big data technological applications that help facilitate mutual transparency, a culture of openness, trust, and confidence between regulators and industry could encourage regulators to reduce the frequency for inspections or shorten the time required for the submission approval process.
Trust-building factors include the establishment of clear rules for information sharing between companies and regulatory agencies, with a clear, shared understanding of why information is shared. This culture may be built intentionally through iterative demonstrations of mutual trust between marketing authorization holders and regulators. A natural starting point might be for the organization to grant health authorities limited access to the PQS to enhance transparency and speed of approvals; then, as the expectations of this exchange are normalized, the parties could consider expanding information sharing for other purposes.
When implementing a holistic control strategy as a risk-based system, it is important for leadership to communicate that this effort is embedded in a company-wide continuous improvement initiative to ensure quality, improve efficiency, streamline operations to make the daily work easier for employees, and make more real-time, data-based quality decisions.
Looking Forward
This article has outlined the rationale for adopting a holistic control strategy that covers the entire product life cycle and explained in broad terms what is required to achieve this goal. An important next step on this journey will be exploring use cases that detail how digitization and knowledge management affect the monitoring of holistic systems, as well as how to create the right management oversight. Additionally, we envision providing use cases about regulatory considerations.