Implementation of a Formal Energy-Efficient Design Process

Sustainability is a key principle for pharmaceutical companies in 2020. However, translating corporate goals into meaningful improvements can be a challenge, particularly when competing factors such as complex technical requirements or ambitious project schedules are involved.
This article describes a formal energy-efficient design (EED) process that has been in use across all industries in Ireland since 2014 and addresses the benefits of integrating this type of study into the design process. Improving efficiency in a highly regulated environment can be a challenge, but companies in even the most regulated industries in Ireland (e.g., pharmaceutical, biopharmaceutical and semiconductor manufacturers) are adopting the methodology.
This article was derived from the authors’ experiences across many projects and in the development of the Irish standard I.S. 399,1 which establishes energy-efficient design as a management system (complementing ISO 9001 and ISO 50001). It provides companies with a robust strategy for delivering energy, environmental, quality, and competitiveness objectives.
What Is Energy-Efficient Design?
An energy-efficient design study is a plan-do-check-act management method, much in the same way ISO management standards are; however, an energy-efficient design study can be applied by an organization for single projects or it can be used on an ongoing basis. The philosophy at the core is to benchmark the asset being procured, built, or retrofitted from an energy standpoint and to try to reduce energy use in a practicable and affordable way.
The energy-efficient design methodology works well for organizations that are used to management systems–type thinking even if they do not have formal certification.
When the project team adheres to energy-efficient design principles early in the project timeline, this often leads to significant capital savings, which, in some instances, can be greater then the energy savings from more efficient operation. A further benefit of energy-efficient design is that it often delivers improvements in plant throughput. For example, heat-recovery projects, especially when applied to the main process, can deliver reductions in heat-up and cool-down times in addition to energy savings.
The challenge and analyze parts of an energy-efficient design study are analogous to a hazard and operability (HAZOP) study—a methodical, logical process with clearly defined steps and outcomes.
Energy-Efficient Design in Ireland
In Ireland, energy-efficient design for industry has been developed by the Sustainable Energy Authority of Ireland (SEAI) over the course of the last 14 years. It was originally intended as a check on the project design from an energy- and water-consumption perspective.
Published in 2014, the Energy Efficient Design Management standard I.S. 3991 was developed by SEAI, the National Standards Authority of Ireland (NSAI), and energy-efficiency industry experts. It helps raise energy issues early in investment projects and aims to control energy consumption across the project’s life cycle. The I.S. 399 approach can be applied in all sectors, organizations, and projects.
Like other energy-management system standards, I.S. 399 certification is possible but not obligatory. Some organizations get I.S. 399 certification to demonstrate they have implemented an energy-management system; others decide to implement the standard solely for the benefits it provides.
In Ireland, implementation of the energy-efficient design process in line with the SEAI Excellence in Energy Efficiency Design (EXEED) program2 supports funding of energy-saving measures in large capital projects. SEAI has formally run the EXEED program since 2016. Before then, energy-efficient design was implemented by a small group of companies (e.g., Pfizer, Novartis, Leo Pharma, Astellas) on a project-by-project basis.
Project Stage | Typical Team | Comment | |
---|---|---|---|
1 | URS | EED team, designers, and client | Highest impact for lowest capital cost |
2 | Precontract | EED team, designers, client, and supplier | Still good commercial leverage with preferred supplier |
3 | Postcontract/detailed design stage | EED team, designers, client, and supplier | Usually carried out at piping and instrumentation diagram (P & ID) fi nalization/HAZOP stage |
The Irish Environmental Protection Agency Act of 1992 requires companies to adhere to the use of best available technology to reduce or eliminate emissions from an activity, and the use of energy-efficient design complements this requirement.
When Is Energy-Efficient Design Appropriate?
Energy-efficient design is appropriate in the following scenarios:
- There is significant energy use.
- There is planned investment that will result in energy consumption.
- Improved corporate image and credibility among customers, clients, and stakeholders are desired.
- There is planned investment that will result in an asset consisting of significant amounts of embodied energy in its manufacture.
- Value engineering is planned (energy-efficient design complements this process).
When Is the Right Time to Complete Energy-Efficient Design?
The earlier that energy-efficient design is implemented for a project, the greater its potential impact on both capital and life-cycle costs will be (see Table 1). Ideally, energy-efficient design should commence at the user requirement specification (URS) stage and be updated continually as new information becomes available.
It is important to note that the energy-efficient design expert (a person competent in the energy-efficient design process, technology, and target areas of the project) does not need to have all the information (i.e., a fully detailed design) to have a positive impact. The first energy-balance evaluation is often approached as a Fermi problem to determine the magnitude of energy consumption and demand, and to identify the significant energy users. This allows progression to the challenge and analyze steps in as short a time frame as possible to allow the maximum number of opportunities to be included in the project scope. Refinement of the energy-balance study can then follow, and the energy-savings register (a live document) can in turn be updated.
Other Sustainability Programs
Leadership in Energy and Environmental Design (LEED) and Building Research Establishment Environmental Assessment Method (BREEAM) are well-known rating systems for the certification of sustainable buildings. Leadership in Energy and Environmental Design was launched by the US Green Building Council in 1998 and has become increasingly popular internationally, including in Ireland.3
Because these rating systems were designed for construction of sustainable buildings, their processes do not include detailed process interrogation. For example, using Leadership in Energy and Environmental Design will help justify using the most efficient chiller in its class, but the Leadership in Energy and Environmental Design process will not lead to the question of whether glycol at –30°C is actually required. The expertise at the core of Leadership in Energy and Environmental Design is in construction, whereas the leaders of an energy-efficient design project will have expertise in the specific process area of the project. There is no reason that energy-efficient design and Leadership in Energy and Environmental Design cannot be used for the same project as they have very different areas of focus.
Renewables and Energy-Efficient Design
Renewable (and low-carbon) energy options should be reviewed after the initial design for energy performance review is completed (i.e., once all the opportunities that will reduce the asset’s energy consumption have been identified and the key ones put in scope); then, the most appropriate renewable energy technology can be selected and sized. If the order of these steps were reversed, the renewable selection might be unsuitable (e.g., biomass steam boiler instead of hot water heat pump/solar) or too big (if the baseload is substantially reduced, the turndown is not enough in the renewable technology and inefficient operation ensues).
Steps in the Energy-Efficient Design Process
The key stages of the energy-efficient design process are outlined in Figure 1.
Asset Definition
The asset being analyzed in the energy-efficient design process should be well defined and encompass all energy services associated with the project (i.e., desired outcomes that necessitate the consumption of energy). Also, where possible, it should be defined by a physical boundary. The defined asset can be extended beyond the specific project (e.g., it could extend to a whole building or site rather than the room in which new equipment will be installed).
Project Execution Plan
The project execution plan (PEP) is a revision-controlled document that provides a clear overview of the project. It should contain the requirements for design for energy performance and energy management, and list the energy-efficient design project objectives and requirements for energy measurement, monitoring, and reporting.
The PEP presents an initial energy-efficient design assessment of the project, including:
- Project timelines for the delivery of energy-efficient design objectives, with a schedule of meetings or reviews where the overall project design will focus on energy-efficient design
- The requirements for lines of communication between the energy-efficient design owner, expert, and project design team as well as other interested parties
- Varying operating conditions
- Criteria for identifying significant energy users
- Criteria for determining if energy-efficient design opportunities will be incorporated into the project scope and design, and how they will be proven to be successful
- Criteria for how the procurement and contracting strategy will support energy-efficient design
- Reference national policies or other mechanisms that could support the viability of energy performance opportunities
- Risks and opportunities related to the project
In particular, the list of identified risks and opportunities is a useful precursor to the challenge and analyze process. This analysis is the first chance to challenge the process design and is the earliest point in the process where meaningful change and the benefits of energy-efficient design can be achieved.
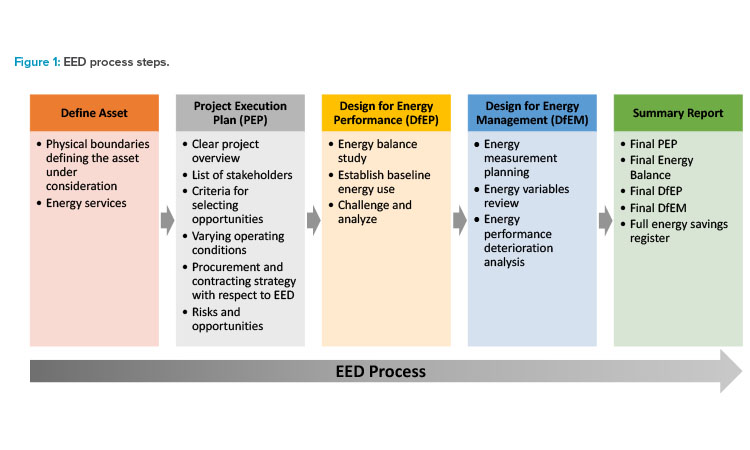
Design for Energy Performance
Design for energy performance (DfEP) is a process comprising an energy-balance study stage, a challenge and analyze stage, and an implementation stage for design projects.
The energy-balance study should be completed at the URS stage and updated continually as new information becomes available. It provides a baseline against which the energy-efficient design savings are usually recorded, and it should use whatever information is available to maximize return on the energy-efficient design effort. The point at which the baseline is taken depends on the type of project (e.g., Greenfield, Brownfield, or replacement) and at what stage energy-efficient design is implemented (e.g., pre- or post-URS, pre- or postcontract). In the analysis, the process is reviewed, and significant energy uses are identified—these will provide the focus for the challenge and analyze stage.
When carrying out the energy-balance study, the challenge and analyze phase should be kept in mind. Initial questions may concern the following issues:
- Storage—thermal storage, battery storage, etc.
- Heat recovery
- Plant turndown
- What grade of utility is required?
- What is the energy service for the project?
Identifying the correct energy service takes a particular skill set or mindset. The challenge and analyze work builds on the outputs from the energy-balance study. It is ideally completed as early as possible, over the course of several workshops. For each significant energy use, the energy service is established and then challenged as per each layer of the Venn diagram (Figure 2). The process and equipment layers could potentially have Venn diagrams of their own if it is deemed appropriate to analyze the system to this level of detail.
Key questions in the challenge and analyze process are as follows:
- What is the energy service?
- How can the energy service be met?
- What are all the energy uses and energy sources?
- What are the significant energy uses?
- What are the expected running hours?
- What is the annual consumption?
- What is the peak demand for each utility?
The energy-savings register is output from the challenge and analyze stage. The energy-saving opportunities are then assessed and accepted or rejected by the stakeholders. The best energy-efficient design analysis ensures opportunities can be disseminated outside of the project group to the relevant stakeholders.
Opportunities selected for implementation should be reviewed and integrated into the design, construction, and commissioning project stages.
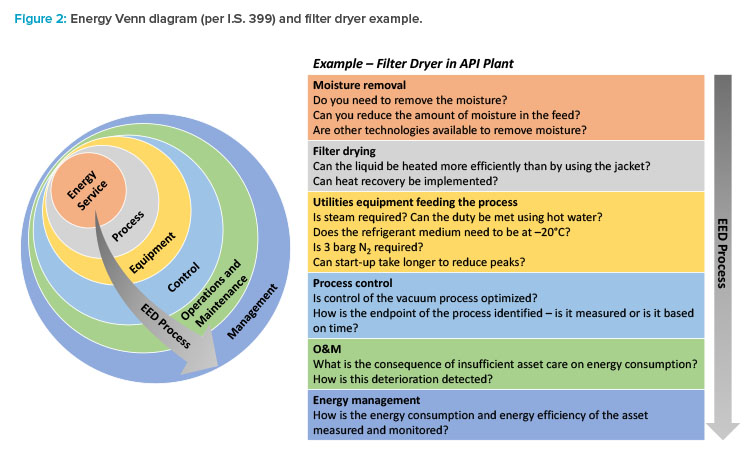
Design for Energy Management
The aim of design for energy management (DfEM) is to ensure that best practices in energy management are included at the design phase. Design for energy management ensures a systematic approach within the design life cycle to manage energy consumption in operations and is intended to support the energy management requirements of ISO 50001.
Design for energy management should broadly take place in the same timeline as DfEP. Design for energy management consists of energy-measurement planning, energy-variables review, and energy-performance-deterioration analysis.
Energy-measurement planning defines requirements for energy measurement and reporting and an energy-metering plan to deliver these requirements. This can be used to form the basis of measuring energy performance indicators (EnPIs) for project validation and postproject tracking (e.g., ISO 50001 management system).
Some common mistakes in energy-measurement planning include:
- Setting EnPIs and key performance indicators (KPIs) that are difficult to measure
- Basing EnPIs on peak plant output even though the plant never achieves that peak
- Selecting meters with insufficient accuracy or turndown
- Not considering parasitic load from services
- Not considering heat from pumps into liquid, which has a negative impact on cooling consumption
- Not considering heat load from lighting into the environment
- Not setting benchmarks for “baseload” operation
- Potentially missing the opportunity for economy mode
- Using too many meters, which makes analysis cumbersome
An energy-variable review of the significant energy uses is completed to understand how energy performance is affected by varying operating conditions. An energy variable is defined as a “quantifiable variable that impacts energy performance.”1 These variables include production parameters (production, volume, production rate), weather conditions (outdoor temperature, degree days), operating hours, and operating parameters (operational temperature, light level). In this review, the design is challenged to ensure that it will operate efficiently under expected or planned variability in operating conditions.
Energy-performance-deterioration analysis examines the potential for deterioration in energy performance during operations and ensures that appropriate measurement and mitigation of this potential deterioration shall be considered during the design stage. Examples of deterioration include fouling in heat exchangers, blocking in HVAC filters, and bearing wear. The output of this analysis may include design changes, metering, and operations and maintenance (O&M) procedures.
Ideally, the outputs of the design for energy management are implemented in same time frame as those from the challenge and analyze stage, and the outputs are captured in the energy-savings register.
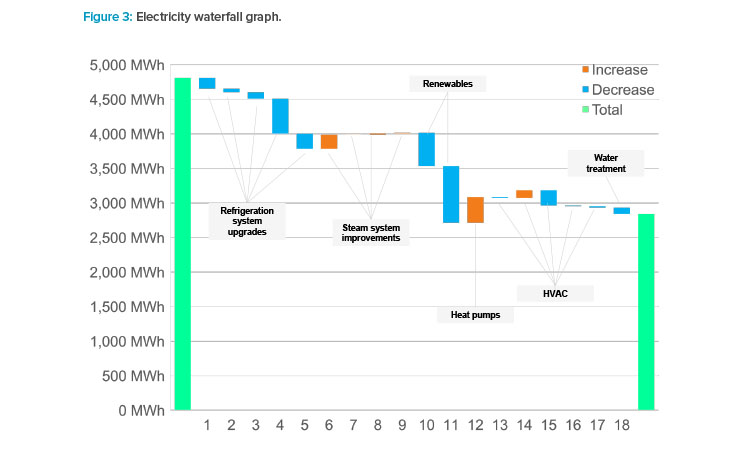
Summary Report
The energy-efficient design summary report should include the following sections:
- Executive summary
- Project description and asset definition
- Comparison of the energy-efficient design design process to baseline
- Energy-savings register, noting opportunities identified and which opportunities were implemented
- Savings achieved or projected
The report appendixes should include:
- Final PEP
- Final energy-balance study
- Final design for energy management
- Final design for energy management
- Energy-savings register
Case Study 1: API Plant
In 2019, an energy-efficient design study was completed for an active pharmaceutical ingredient (API) plant in Ireland. The asset was defined as the entire site, including all production and nonproduction buildings and utility systems. The aim of the study was to provide a framework to ensure energy efficiency was maximized for upcoming capital projects.
An energy-balance study was completed for the site and two challenge and analyze sessions were held. Opportunities that seemed to be feasible were scoped and costed for review by site management.
The feasible electrical and thermal savings identified are represented in waterfall graphs (Figures 3 and 4, respectively). The initial baseline (annual energy usage) is shown as the bar on the left, and the incremental change associated with implementing each opportunity is shown. The bar on the right side is the calculated site baseline if all opportunities were implemented. In some cases (e.g., introduction of a heat pump or changing from a steam-driven condensate return pump to an electrically driven one), a thermal energy–saving opportunity will result in an increase in electricity consumption. These increases are also included in the waterfall graphs.
Refrigeration system improvements (including a more efficient plant and a control upgrade) are expected to result in a 20% reduction in site electricity consumption. Chiller replacement is under consideration for the site because the present refrigeration system may be obsolete, but the energy-efficient design exercise identified several refrigeration-related efficiency measures that would have a substantial impact on-site energy use. A suitable heat sink (suitable baseload, physically close to the chillers, and already using hot water as a heating medium) has been identified for a heat pump, which can be installed in conjunction with the new refrigeration system. Thermal savings of 20% for the site are expected from this upgrade. The overall refrigeration capacity that will be installed is likely to be reduced as a result of the study, which will lead to a capital saving.
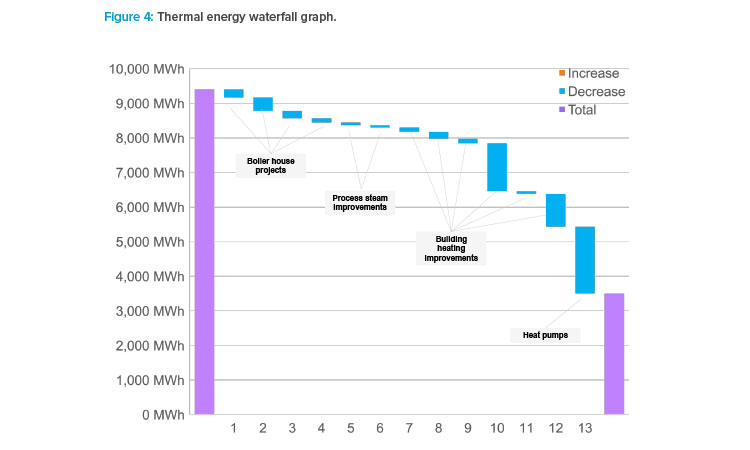
The plant currently uses glycol at –25°C for all process cooling. The requirement for this temperature was challenged. The lowest temperature pro-cess application on-site at present is –3°C. The annual saving available from moving to a higher-temperature system was estimated at €120,000. In practice, this change may be difficult to achieve—for example, additional heat transfer area may be required to fulfill the same process loads, and there may be additional validation requirements. The scale of saving, however, means that this is something that will be explored prior to any refrigeration up-grade.
Boiler house upgrades (metering upgrade, automatic firing control, economizer) are expected to result in a further 10% thermal energy saving for the site. One of the two boilers is maintained on “hot standby” to quickly provide steam in the event of an issue with the lead boiler. The energy cost for this was calculated to be at least €6,000 per year. An alternative recommended for consideration was the installation of a steam generator, as that type of generator can provide steam from cold start-up (assuming a charged hot well is available) in under five minutes.
If all the opportunities were implemented, site energy usage would be reduced by more than 50%. Suitable opportunities will be selected based on practicality of implementation, capital cost, carbon saving, and investment per tonne of carbon saved, and in line with the site’s strategy. The site masterplan will be updated to include these projects.
Case Study 2: Tableting Plant
In 2017, I.S. 399 was implemented for a tableting plant in Ireland as part of the development of its new pilot plant facility. The company’s stated rationale for the energy-efficient design project was as follows:
- To use the methodology to ensure that new infrastructure is efficient and low cost to run
- To use the project as a way to test out the methodology so that perhaps it can be used in future projects and/or become a corporate standard for new capital expenditure projects
- To ensure that the pilot plant is efficient, which will allow it to be fed from the existing site utilities, which (for some services) were almost at maximum capacity
The pilot plant was built in a corner of the existing facility that was fallow and was to be supplied with the existing utilities. A meeting took place during the predetailed design phase to discuss the impact of this on the current facility. The energy-efficient design project looked at the following utilities: chilled water, low-pressure hot water (LPHW), hot and cold process water, purified water, and ventilation (HVAC).
In addition to applying the principles of energy-efficient design and I.S. 399, the goals of the project were as follows:
- To assess the impact of the pilot plant on the existing utilities
- To limit the pilot project’s impact on these utilities by using the principles of energy-efficient design
- To ensure that staff understand the I.S. 399 process, and to be able to replicate this process, if desired, in future capital expenditure projects
The designer completed a high-level demand estimate for the pilot plant’s utility consumption, and this was scrutinized in detail as part of the energy-balance study.
The calculated annual energy-consumption figure included thermal energy (LPHW, steam, and clean steam) from gas consumption and electrical energy consumed directly by process equipment and indirectly through utility provision (purified water, process water, compressed air, and chilled water).
In addition to this, a study of the baseload energy consumption was also completed. A large part of the energy consumption in the baseload design was found to be the consumption outside of production hours. Thus, one of the main interventions suggested and implemented was a setback mode for nights and nonproduction weekends, while still allowing the plant to operate within the GMP remit.
A large part of the exercise was the DfEM process, a review of the energy variables and energy-performance-deterioration analysis. In addition, it was important that all the utilities’ consumptions and demands were metered and visible for staff to understand the impacts of the extension.
Energy efficiency and lifetime cost were considerations in plant selection, and optional features offered in tenders from prospective contractors were assessed using the most economically advantageous tender (MEAT) criteria.
Factors that determined whether an energy-efficient design opportunity was progressed included:
- Simple payback (anything with payback of five years or less will be subject to detailed assessment)
- Health and safety
- Throughput (e.g., if the opportunity leads to improved operational efficiency)
- GMP requirements
The identified opportunities that qualified under these criteria had thermal savings of 148,000 kWh (43% steam saving, 57% hot-water saving) and electricity savings of 104,000 kWh. The annual operating cost savings were calculated as €17,000. The cost of implementation (largely associated with the additional automation scope) was €67,000, and the calculated payback was four years.
Case Study 3: Topical Products Manufacture, Filling, and Packaging Plant
In 2008, an energy-efficient design study was carried out for a planned combined heat and power (CHP) project. The initial proposal was to install a CHP system with electrical output capacity of 2 MW and providing heat and cooling (using a new absorption cooler) to the process.
One of the outcomes of the challenge and analyze stage was that onsite measurements were carried out to validate the existing heating and cooling baseloads, which had been used in the design.
The outcome of the energy-efficient design study was that electrical capacity of the system was reduced to 1 MW because the thermal demands used in sizing were overstated. Had this study not been completed, the plant would have run inefficiently after installation because all the heat would not have been used.
Capital savings of more than €500,000 were achieved through use of the energy-efficient design process.
Experience in Other Industries
Table 2 summarizes selected opportunities identified in recent energy-efficient design studies in other industries for sites in the EU and in Africa.
Conclusion
Although it is preferable to start energy-efficient design early, carrying out energy-efficient design at any stage has always been found to yield benefits, even on smaller projects. It can be difficult to ensure the energy-efficient design process is followed strictly in some circumstances (e.g., if a project has an accelerated schedule and opportunities to reduce energy consumption have been missed). However, once the process starts, there are usually opportunities to be unlocked. Barriers that may need to be overcome to maximize energy-efficient design benefits can include:
- Specifications
- Timelines
- Budgets
- Contracts
- Perceived “hassle” factor for client or supplier
From experience, the following factors are important for the success of energy-efficient design for a project:
- Having a client sponsor with influence on capital spending is a key criterion for success of energy-efficient design in any project.
- It is important to review the register of opportunities with the project manager before formally issuing the study. The project manager will ultimately be held to account for any proposed savings, so they need to be comfortable with the calculations and assumptions used.
- Energy-efficient design principles should be applied to a project as early as possible. Applying the principles early in the project life cycle affords greater opportunity to significantly impact the energy service. Sometimes, this can be difficult in practice—many projects do not get engineering funds approved until the business case has been approved, and by the time this happens, the URS may be “locked down.”
- Once the supplier understands energy-efficient design, they are generally positive—briefing them in advance of a workshop is a good idea.
- Capturing the energy-efficient design outputs from projects and applying them to subsequent projects is important. By doing this, energy-efficient design becomes as routine an element of the project life cycle as a design risk assessment or HAZOP.
- The key process requirements (energy services) must remain a priority. Opportunities must be practical and not have a negative effect on the required energy service.
- Peak calculations and future expansion allowances should be challenged to make sure that the right-size process and utilities will be installed.
Industry | Key EED Opportunity | Annual Energy Saving |
Capital Investment |
Other Impacts |
---|---|---|---|---|
Distilling | Use alternative source of cooling for process cooling | 26.5 MWh electricity 180 tonne CO2 |
€300,000 saving |
Security of cooling supply Instant cooling start-up Reduced noise |
Semiconductors | Dual setpoint chilled water | 398 MWh electricity 212 tonne CO2 |
€1,000,000 investment |
Greater redundancy |
Brewing | Modify heat recovery to maximize benefit, design steam out of conversion process | 5,000 MWh thermal energy 1,300 tonne CO2 |
€600,000 investment |
3 tonne/hour reduction in steam demand Water saving of 30,000 m3/year |
Shipping | Redesign of reefer metering and reporting | 300 MWh electricity 385 tonne CO2 |
€700,000 investment |
Allows inefficient container cooling to be easily identified |
Packaging | Alternative sourcing of raw materials and air recuperation from bottle blowing | 200 MWh electricity (EED study showed that raw material selection had the biggest impact on overall line energy consumption) |
€100,000 investment |
Changes in supply chain strategy |
Each of the steps described as part of the energy-efficient design process is common sense and part of good design practice; however, without a formal process, it is difficult to ensure that each will be completed for a project.
The advantages of implementing a formal energy-efficient design process can be substantial, ranging from large capital, energy, and carbon savings on the project itself to potentially significant opportunities outside of the core project scope. The process provides a useful cross-check and due-diligence tool for any project.