Pharma Facilities, Composable Tools, and Validation 4.0

The pharmaceutical industry stands at the precipice of a revolution as emerging digital technologies provide new opportunities to boost productivity through continuous process improvements. The Pharma 4.0™ framework, an adaptation of the broader Industry 4.0 movement, aims to transform how drugs are produced and delivered.
Fueled by a convergence of advanced digital technologies like Industrial Internet of Things (IIoT), big data analytics, artificial intelligence (AI) and machine learning (ML) 1, and cloud computing 2, this wave of digitalization promises to radically reshape and improve the landscape of pharmaceutical manufacturing.
As the industry drives to adopt Pharma 4.0™ and embrace digital transformation as a whole, brownfield facilities pose a unique set of challenges. These include the sheer complexity of integrating new technologies with existing systems to the cultural resistance to change that often comes with established working practices. Challenged by legacy systems and manual processes, brownfield facilities require a fundamentally different approach to adoption of the new digital reality that has transformation at its core.
The true challenge, beyond the buzzwords and lofty ideals, is real-world implementation for an existing site. Implementing Pharma 4.0™ necessitates a holistic approach that encompasses technological upgrades, organizational shifts, cultural transformations, and robust data governance strategies. By understanding the potential and practicalities of Pharma 4.0™ and adopting the associated practices, pharmaceutical manufacturers can make their operations smarter, safer, and more human-centric (see Figure 1).
FUNDAMENTAL CONCEPTS FOR DIGITAL TRANSFORMATION
Before we can break down how to successfully revamp facilities to meet the needs of today’s digital age, it is crucial to discuss a couple of key concepts. One of the main differentiators with digital technologies is ease of use that makes it possible to democratize work that previously required specialists. This is achieved with “no-code”, digital technologies that allow you to create solutions without a single line of code. Another concept called “composable” solutions provides unique and specific ways for frontline operators to interact digitally and enable them to be more productive.
A composable enterprise is defined by Gartner as an organization that delivers business outcomes and adapts to the pace of business change. It does this through the assembly and combination of digital content 3. This digital content needs to provide the operator with a digital interactive solution where the physical and virtual worlds are interconnected. This is a critical principle in achieving productivity gains and is inherent to the new digital reality3.
These novel concepts provide a transformative solution to the pharmaceutical industry and enable innovative solutions for digital content creation, including batch recording and GMP compliance. They allow the pharmaceutical industry to leapfrog from paper-driven processes (Pharma 2.0) directly into the new digital age (Pharma 4.0™). This is critical to revamping facilities and reaping the productivity gains of Pharma 4.0™.
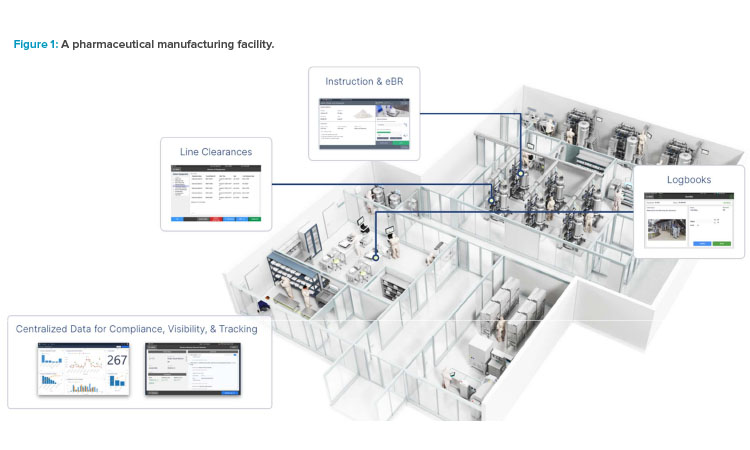
COMPOSABILITY
To truly understand what composable is, we need to first understand what it is not. The opposite of a composable solution is a monolithic solution (see Figure 2). These types of solutions attempt to provide a process-centric approach to digitizing manufacturing processes. They are a known quantity and have been widely used in the industry for the last 25 years.
They are monolithic because they take a one-size-fits-all approach with finite functionality. They serve all types of processes and modalities, in all scenarios, with any machine, for all operators, and with one complex, configurable system.
Overall, monolithic systems have the following characteristics:
- Long time to value: They take months to years and high effort to implement and deploy.
- Process-centric vs. human-centric: The operator serves the system vs. the more valuable alternative where the system serves the operator. This model inhibits productivity gains by not focusing on the operator.
- Complex customizations: They typically require customization to support the differing needs of each operation where they are implemented.
- Inherently complex and hard to maintain: They require a dedicated team with unique knowledge of the technology and the solution.
- Nearly impossible to extend: They do not extend nor scale well because they expect all operations to adhere to one standard data model.
- A strict top-down approach: They assume changes are minimal and are generally known.
These types of solutions are built to automate a process where humans have to play by a strict set of rules, ultimately robbing organizations of rapid time to value and exponential productivity increases.
On the contrary, composability is a framework through which solutions in the form of digital content, also called “apps,” are built in a no-code environment by the people closest to the process. At a high level, composable solutions offer flexibility in the face of evolving standards and requirements because they can be continuously modified. The main concept here is to build content, one app at a time, in an iterative manner. During building, real-world process knowledge and operator feedback are continuously used to steer the design. These continuous improvement iterations result in realizing value quickly and improving content over time.
When it comes to the manufacturing space, a composable architecture 3 empowers operators to interact with digital solutions where the physical and virtual worlds meet 4, ultimately enabling them to drive new process efficiencies.
Composable solutions are purpose-built, highly configurable digital content that can and should be continuously changed and adapted to the latest operational needs. These solutions provide added value in their ability to easily integrate and collaborate with other systems.
This is at the core of the IIoT, where different autonomous devices and systems easily communicate and interact. The composable solution is built from composable elements, or apps, that are uniquely integrated with operators and equipment. Each one provides a specific and unique operational environment in which the operator is augmented with the right data, at the right time, from the right source. They instrument the activity and operational processes by capturing granular data in the context of the operation. This all requires a composable approach where apps have specific flows and connections to the local physical world.
These apps can do the following:
- Digitize processes and activities
- Connect to production equipment via edge devices and no-code-friendly integrations
- Use advanced sensors and vision technology to drive new efficiencies and higher quality
- Leverage AI and ML to augment decision-making and implement improved error-proofing
Modifying or enhancing an app is the same as changing master data because they represent the physical process and activities. The digital tool that supports the frontline operations is a data and process management tool that connects people, things (machines and devices), and systems used in a production or logistics process. Manufacturers can manage these app changes through a governed, version-controlled life cycle process to ensure compliance.
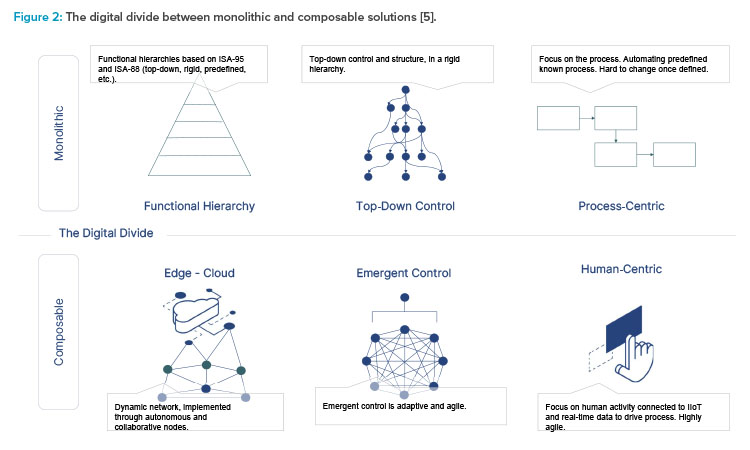
DEMOCRATIZATION
Democratization is defined as the process by which access to technology rapidly becomes more accessible to more people 6. It means empowering individuals with access and agency that transcend technology in Pharma 4.0™ and it translates to unlocking the potential of citizen developers 7.
Citizen developers bridge the gap between domain expertise and technical development, bypassing lengthy IT cycles and accelerating problem-solving. This boosts productivity through targeted solutions and fosters ownership and engagement, leading to a more agile and responsive manufacturing environment. Democratization, through citizen developers, empowers individuals to become active participants in shaping their work, driving both productivity and innovation within the pharmaceutical industry.
Process and quality engineers are equipped with no-code tools to create solutions addressing specific pain points and serving frontline operators. Imagine a process engineer building an app to optimize equipment use based on their deep understanding of its nuances. These solutions can range from streamlined data collection procedures to automated quality control checks, directly impacting productivity and quality.
With modern digital technology, everyone can become builders of digital content. We already do this when using office tools such as Microsoft Word and Excel. As an example, we can easily program our smart door—a home IIoT device—to open automatically when we get within range so we don’t have to take our key out. This is a big change compared to the high level of skills and expertise needed to build even simple automation tasks in traditional systems. No-code is a key enabler of democratization; it allows people with no programming or IT skills to build content that automates manufacturing processes in a simple and intuitive way.
The term “citizen development” might sound scary in a regulated environment or in larger companies that have separate organizations responsible for implementing technologies. Yet, it is a part of the cultural shifts that are a true success factor for a sustainable and engaged workforce in the digital age. Most of the new platform technologies provide accessible and transparent controls to manage content being created, distributed, and consumed.
THE PHARMA 4.0™ PARADIGM
Pharma 4.0™ is a framework for adapting digital strategies within the unique context of pharmaceutical manufacturing 5. In practical terms, this framework introduces more connectivity, increased productivity, simplified compliance, and the ability to leverage production information to respond to problems as they emerge.
The term was trademarked by ISPE to align four key target components (information systems, resources, organization and processes, and culture) and two enablers (digital maturity and data integrity by design) to this term. It also provides best practices for accelerating digital maturation across the pharmaceutical industry.
Pharma 4.0™ is more than just an approach to digital technologies: It’s a shift in mindset. Manufacturers need to find new ways to identify problems and implement advanced technology to increase efficiency and effectiveness in meeting compliance requirements. From connecting workers to introducing more human-centric workflows and driving shifts in company culture, humans are at the core of Pharma 4.0™. As such, companies must do more than automating processes.
To achieve this level of operation, the following should be considered:
- Eliminating paper-based processes and static, document-based evidence
- Eliminating data silos with better communication across the life cycle of drugs
- Improving data collection and sharing practices, allowing for less frequent interactions with and/or more visibility to regulatory bodies
- Shifting to a risk-based and integrated approach for validation
- Implementing a holistic control strategy tied to validation
- Increasing the focus on data for quality assurance and compliance
Pharma 4.0™ envisions a manufacturing paradigm that allows manufacturers to be agile, iterate quickly, connect resources and workers, and produce more quality products with better patient outcomes.
OPTIMIZING A DIGITAL TRANSFORMATION
It is evident with all the concepts introduced so far that digital transformation and adoption of Pharma 4.0™ are more than just a technology initiative. To truly embrace Pharma 4.0™ and realize its productivity gains requires having the right culture, processes, digital technologies, and resources in place across the organization.
The following steps can help deliver the ultimate balance between maximizing productivity, minimizing risk, and achieving compliance throughout your digital transformation journey.
Build a Digital-First Culture
Adopting a digital-first strategy is no longer optional for organizations in the pharmaceutical industry if they want to remain competitive. This means that pharmaceutical manufacturers must include digital as an integral part of their business strategy; they must define a data-driven business strategy. This is why building a digital-first culture is essential for long-term success.
Building this type of culture in today’s manufacturing landscape requires the following:
- Innovation is encouraged: Workers feel empowered to identify problems and implement solutions with new digital technologies.
- Data is seen as a valuable asset: Real-time production insights power informed decision-making. Therefore, digital data in all forms, from every process, is necessary.
- Continuous improvement is adopted as a core principle: Iterative feedback loops enable workers to drive real business impact through continuously adapting digital content and instrumentation of all activities.
These cultural components of the strategy must be in place before the transformation begins. They are foundational to align the operational and quality organizations and provide a unifying direction with buy-in from all levels of the organization. This is achieved with a coherent strategy that puts culture first. The next step is to build out an agreed-upon change management program.
This program should highlight the benefits of the change by communicating the specific value of this new technology for different team members. It should define the implementation timeline and process, which includes creating and distributing a schedule with clear next steps. Finally, it should provide any necessary training by ensuring the workers involved are equipped with the guidelines, tools, and resources they need to adapt to this new way of working. They will need to understand how to do their jobs in a digital way. One of these skills is to understand where to find data in this new paradigm to enable action and decision-making.
Leverage a Composable Platform
There’s a common misconception that going from paper-based workflows to a Pharma 4.0™ facility requires overhauling your systems—and a massive effort in implementing complex, monolithic software systems. However, the digital technologies with democratization and composability allow for more flexible, adaptable systems that can be implemented from the bottom-up 8. This approach simply means that the solution is built iteratively in small steps to solve one problem at a time. An added benefit is that it slowly can phase out existing systems while effectively digitizing all manual paper processes.
As previously defined, composable solutions enable a short time to initial value and a simple approach to real, continuous improvement. This is done in smaller increments if necessary. The resulting solution has a structure that allows modification and adjustment, big or small. This is advantageous because it reduces the risk; change can be implemented rapidly, and that enables operational agility.
When introducing new technologies into the facility, it is important to determine if they enable Pharma 4.0™ and are true digital technologies or if they are composable. If the technologies require customizations or point to solutions to fill in any functionality gaps, they are not suitable; they force processes to work around generic solutions. Oftentimes this leads to waiting to make changes or improvements and therefore stalling or even halting innovation.
Many composable systems tend to have no-code capabilities, which accelerate the solution development cycle and empower process experts to build solutions for specific use cases. This gives the power to those that understand the problems best. The composability provides a way for the process experts to start with one area of the facility and add use cases over time.
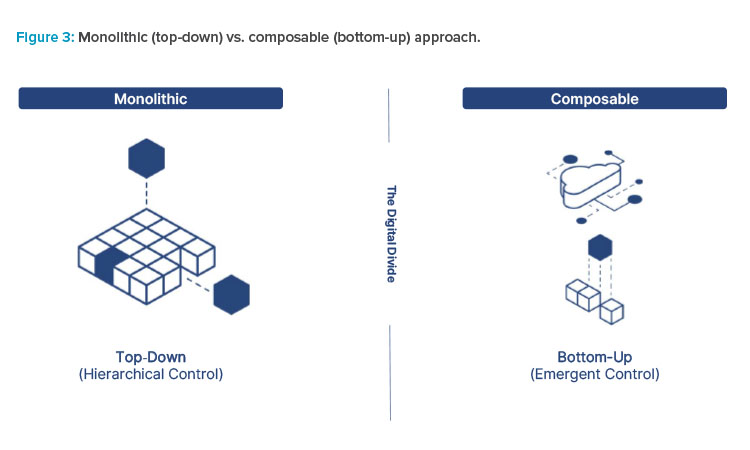
Consider tackling use cases for error-proofing work instructions that include compliant e-signatures or creating customizable dashboards to gain real-time operational visibility and enable better decision-making. In other words, prioritize GMP use cases that pose the highest risk or the area with the most opportunity to prove that compliance can be seamless.
Adopt a Bottom-Up Approach
Digital technologies are adopted most effectively in small steps, one app at a time. This bottom-up approach is critical and a core attribute of these technologies. Digital technologies differ in that processes do not have to be adapted to fit the solution. Rather, solutions are built that can adapt, which augments operators and facilitates processes.
Unlike monolithic systems that leverage top-down hierarchical structures to provide solutions that fit within certain constraints, composable architectures allows building solutions in a variety of ways. This drives rapid time to value and exponential productivity increases.
By adopting composable solutions that are built from the bottom-up in an iterative manner, you can digitize manufacturing operations in the most efficient way. This novel approach to designing and deploying solutions makes it easy to:
- Remove the difficulties associated with adhering to complicated standards and systems
- Free engineers to focus on building apps that fit the process and increase the rate of solution development
- Capture granular data about each discrete process and activity
- Easily adapt a solution with minimal impact to the overall system behavior
- Build apps starting with one use case and expand to cover the process, distributing complexity across apps so that they’re easier to maintain
- Align with lean continuous improvement principles, without sacrificing sustainable, decentralized innovation
- Set the foundation for continuous validation by digitizing risk controls that can capture data from processes, which is highly aligned with continuous improvement
PROJECT MANAGEMENT BEST PRACTICES
An agile project management style leverages short, iterative development cycles to achieve continuous improvement. When integrating new technologies with existing infrastructures, this methodology will empower an organization to respond more quickly to changes through cross-functional collaboration, rapid iterations, and a flexible, bottom-up approach.
Complementing composability, an agile approach further aids in achieving value and iterating to improve quickly. This is done by engaging the frontline operators who work on the manufacturing floor every day. Incorporating insights from the workers who know the processes best helps more easily determine the type of solution that meets your organization’s unique needs.
GOVERNED CITIZEN DEVELOPMENT
Democratization can happen organically as an output of no-code solutions and citizen development. It allows process engineers who have deep knowledge of the process to create digital solutions with quality in mind, or quality by design. This eliminates the need to translate the process and the supporting science to IT people to configure systems.
Recognizing that compliance is necessary, governance features are built into these modern operations platforms. The platform should implement a governance framework that includes granular access management, approval processes, and version control for the digital content. These capabilities are used to assure that the right data and audit trails are captured and the distribution and availability of the content are managed with ease. We recommend using this visibility into the digitized processes and managing the platform with data and governance.
The key component of governance is the enablement function that supports citizen developers and provides them with clear rules, best practices, and guidance. This can ensure quality solutions, which impacts business value and manufacturing productivity.
The enablement function requires a well-defined process and expertise to:
- Build and maintain a library of preapproved and prebuilt common content, templates, and technical solutions. This will guide reuse of common content. Doing so helps standardize key process requirements that ensure consistent quality.
- Create development and deployment best practices for content, including user interfaces (UI), functionality, data capture, and structures.
- Manage the ideation process so that a compliant content life cycle is started with a clear set of requirements. Here, it is critical to have a Validation 4.0 approach with defined user stories and process maps (see the following section for more information).
- Establish an effective review process to assess content for compliance, security, and functionality before deployment. This empowers the citizen developer while ensuring all applications meet regulatory standards.
- Create secure and isolated environments where citizen developers can build and test their applications without impacting live operations. This allows for experimentation and iteration while maintaining data integrity.
EMBRACE VALIDATION 4.0
We’ve provided the basic structure and points to consider when adopting a Pharma 4.0™ approach, focusing on the technological and organizational aspects required for success. Now we shift toward a focus on a critical operational change required to successfully deploy these approaches into the regulated space: validation.
The concepts around citizen development and composable solutions encourage engagement from the people who know their operations the best. However, these approaches to continuous improvement do not obviate the need for change management. Validation must be managed in a way that is risk-based and integrated with the changes to keep up with the iterative, continuous improvement cycles.
Whether the concern is the technology, processes, or people, we must always demonstrate control. Regulations are in place to assure this, and the root of the requirements is to demonstrate control around ensuring patient safety and product quality. This is especially true in terms of a brownfield implementation or overhauling an existing facility. We know that extensive change is required; workflows, processes, equipment, and systems are already in place.
The Validation 4.0 approach described in the ISPE Baseline® Guide, Vol. 8, Pharma 4.0™ includes fundamental considerations for pharmaceutical quality systems, quality by design (QbD) 9, and quality risk management (QRM) 10.
To revamp an existing facility, the product and process knowledge from the existing QbD framework can be used to map out the relevant process(es) into process maps that clearly identify data flows. If a robust QbD framework is already in place, process and data maps may already exist. Whether they need to be created or already exist, their value is foundational in understanding the appropriate controls strategy. The data flows provide a contextualized basis to perform risk management and explicitly identify critical parameters.
Once your critical parameters are identified, you will determine appropriate risk controls. For the areas that challenge the desired level of product quality, there will be more robust controls. These will use, where possible, technical controls based on the features available in the composable platforms. This approach provides an effective mechanism to control the solutions’ impact on quality. It might include mapping an entire process, defining a smaller unit operation, or homing in on a specific change to the process, facility, equipment, or system and then iterating in a QbD fashion. The iterations can either validate or invalidate that a defined control is successful in achieving the product quality indicators.
This approach to change implementation can yield validation as a de facto output. However, it does require product and process knowledge. It allows the right subject matter experts to be involved early and allows an agile approach so that companies are iterative on the continued increase of knowledge gained by this intentional approach to using QbD and QRM.
DIGITAL TRANSFORMATION IS NOT OPTIONAL
The age of Pharma 4.0™ is here, and those who do not transform their processes accordingly will be left behind. When starting your digital transformation journey, there are a few key concepts to keep in mind. Firstly, don’t forget the operational, organizational, and cultural changes that need to come with adapting the Pharma 4.0™ approach. Investment in the people aspect of this change is one of the primary success factors, especially in the case of revamping existing facilities.
Secondly, be ready to embrace composability. Doing so will enable you to start small and continue to grow and improve your efforts over time. Ultimately, this approach leads to a quicker time to value and provides the agility that you need to succeed in today’s fast-changing environment. Examples of manufacturers that have adopted this approach show how fast digitalization can be implemented with promising results. Implementation time is vastly reduced to 3–6 months from kick-off to first digital history (electronic batch record) app validated and in production. In addition, the digital data that is a result is used for operational improvements and not merely compliant batch recording 11.
CONCLUSION
Although the concept of citizen development can sound scary, it is critical. Adopting this methodology will empower organizations to effectively leverage the knowledge of those who know the operations best: the engineers and frontline workers. People are the key to productivity in the digital age. By leveraging the latest technology to provide workforces with the data-driven context they need, when they need it, companies can streamline operations while maintaining compliance.
This augmented lean 12 approach is particularly critical considering the ongoing manufacturing labor shortage13 and high workforce turnover rate 14. To attract and retain skilled workers, organizations need to provide an environment in which employees feel empowered to improve their workplace. This will enable them to grow professionally and become more efficient. It will also help maintain compliance and the shipping of quality products in an agile operating environment.