Automation Supports ESG Goals for Pharma Facility Conversion

Implementing advanced automation technologies is a strategic move that can amplify the positive outcomes of environmental, social, and governance (ESG) initiatives. By leveraging ESG initiatives, pharmaceutical companies can enhance their competitive edge and contribute positively to global sustainability efforts.
As pharmaceutical manufacturers transform their facilities to meet new operational demands and comply with evolving regulatory standards, a compelling opportunity emerges. The integration of cutting-edge digitalization technologies during facility conversions can serve as a catalyst for profound ESG advancement. It offers enhanced energy efficiency, waste reduction, and improved social governance. This approach can increase a manufacturer’s efficiency and sustainability commitments at a time when operations and ESG stewardship are increasingly linked.
ESG IN PHARMA FACILITY OPERATIONS
There is often a disconnect between the ESG goals set at the organizational level and determining how these goals will impact the operations or decision-making processes within a facility. Corporate sustainability policies in the pharmaceutical industry are driven by the evolving global regulatory landscape 1 as well as internal and external stakeholders 2. Although this provides a strong path for goal setting, alignment of these goals with day-to-day operations often leaves gaps.
At the facility level, the material key performance indicators (KPIs) mainly align with the “E” of ESG; the primary focus is the environmental impact of the facility, with less focus on the social and governance drivers of the company. The question is how to identify and leverage the opportunities on-site to make progress toward corporate ESG goals in carbon, energy, water, waste, and beyond?
Facility operations and ESG strategies have a shared goal of reducing operational risk and operational cost, which can both be achieved without negatively impacting facility operations. For example, heating, ventilation, and air conditioning (HVAC) currently account for approximately 65% of plant energy expenditures 3. Increasing HVAC efficiency can decrease operational cost and risk while also improving operational efficiency.2
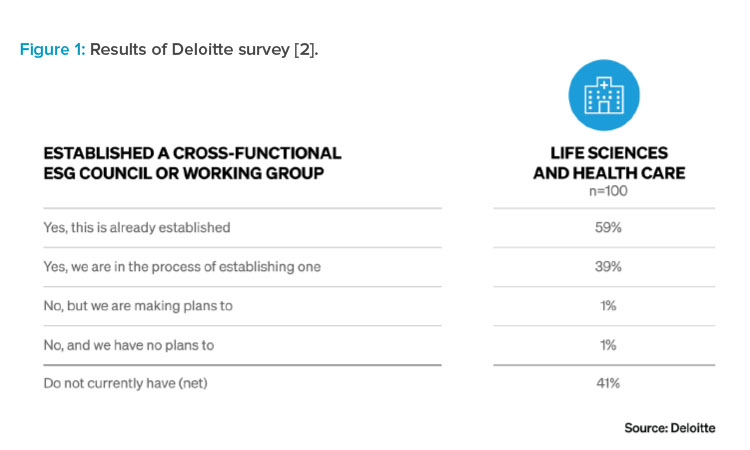
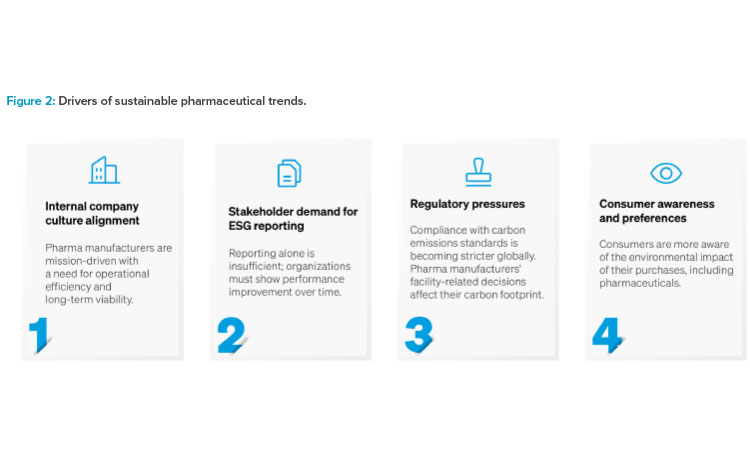
ESG goals are guided by data—at a minimum requiring utility data collection. The more granular and/or real time the data collection is, the more actionable the data becomes. As granularity increases, monthly or annual reporting moves to real-time identification of energy load as well as any anomalies or deficiencies in usage. This empowers the facilities team to better manage plant equipment throughout its life cycle.
Automation in data collection and equipment monitoring enables trend tracking in real time and, through this, the ability to adapt to environmental changes. This can be facilitated with the use of a digital twin, which acts as a performance twin that mirrors plant equipment operations. Digital twins can also provide feedback on performance that can be used to inform planning at the facility and portfolio levels, including operations budgeting, capital spend, etc.
ENERGY CONSUMPTION IN PHARMACEUTICAL FACILITIES
Having a clear understanding of a facility’s energy consumption is a critical first step in becoming more efficient and sustainable. Companies without an understanding of their energy consumption rates will struggle to define their financial and sustainability targets.
The pharmaceutical industry consumes approximately US $1 billion (about $3 per person in the US) worth of energy each year 4. Recent estimates have shown that approximately 65% of the energy consumed in pharmaceutical facilities is used by environmental control systems such as HVAC systems, chillers, and cooling systems. Additionally, another 25% comes from plug loads and processes (tunnels, washers, incubators, or sterilizers), with 10% of energy being consumed with lighting the facilities5.
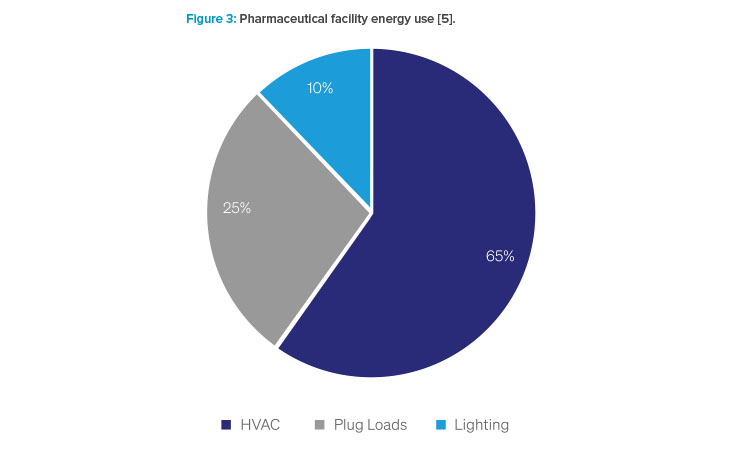
Historically, broad designs and systems are no longer viable options for facility designs, as they are key factors that increase pharmaceutical facility energy consumption. A low-energy-use facility instead requires improved facility, system, process, and equipment designs, and initiatives such as eliminating steam use, open loop systems, and heat loss.
Implementing digitalization through Pharma 4.0™ will decrease energy consumption and waste by creating a facility that is automated, predictable, and operates in an efficient and sustainable manner.
Understanding new technology and equipment options for the initiatives is also required to develop a facility ESG conversion plan. To understand facility energy consumption and efficiency, the facility owner will need to assess the facility’s current digitalization level and develop a digital plant-maturity model. New technologies include:
- Improved utility metering and reporting
- Facility digitalization and monitoring systems for peak performance
- Predictive maintenance systems to monitor and improve equipment and systems
Pharma 4.0™ refers to the adoption of the Industry 4.0 framework within the pharmaceutical manufacturing sector. It emphasizes the integration of advanced technologies such as the Industrial Internet of Things (IIoT), artificial intelligence (AI), big data analytics, and cloud computing into pharmaceutical production processes. Implementing digitalization through Pharma 4.0™ will decrease energy consumption and waste by creating a facility that is automated, predictable, and operates in an efficient and sustainable manner.
FRAMING ROI IN AUTOMATION AND DIGITALIZATION
Automation in pharmaceutical manufacturing facilities is a rapidly evolving field, subject to nondisclosure agreements on facility designs. It also presents a challenge to pinpointing return on investment (ROI) with traditional, lagging metrics. This section delves into the pivotal indicators that define the current ROI landscape and offers suggestions for evaluating success in automation and digitalization strategies.
Efficiency and Innovation
Automation technologies such as robotics, smart workflows, advanced analytics, data visualization, natural language processing, and cognitive agents are driving efficiency and fostering innovation 6. The major pharma manufacturers are already deeply invested in digitalization, leveraging machine learning (ML) to accelerate time frames for compound discovery, precision medicine, and optimization 7. Other innovations in pharma digitalization include measuring energy usage and leveraging data to offset peak power usage8.
Applications
Research estimates that with every 2.2 pounds (lbs.) of drug manufactured, a staggering 220.46 lbs. of waste is produced 4. Automation has been applied to quality control, process optimization, and data analysis 9. This increases the speed and accuracy of processes such as filling, packaging, and inspection 10. Industries outside of pharma are leveraging sensors and IIoT-enabled software to precisely monitor elements like compressed airflow. This allows manufacturers to identify leaks, optimize process, and improve efficiency. Examples include Colgate-Palmolive reducing energy use in several packaging lines by 15%11.
Reduced Administrative Expenses
General and administrative (G&A) expenses in the biopharma industry equal about 7% of total revenue, 1.5%–2% higher than in comparable sectors. Automation can break the linear relationship between workload growth and cost. The potential impact is significant. McKinsey reports that best-practice pharma companies, which have fully automated tasks, report G&A spending as low as 3.5% of revenue 6.
Risk Management
Pharma 4.0™ initiatives support augmented manufacturing, personalized medicine, additive manufacturing, localized 3D printing of treatments, and even a future where humans are no longer intimately involved with production. This can substantially improve the challenges with aseptic manufacturing 12. Leveraging IIoT reduces risks through data-driven preventative maintenance, controls the drug manufacturing environment, and facilitates supply chain monitoring13.
Regulatory Compliance
Deploying automation can help pharmaceutical companies follow stringent regulatory and compliance standards, in addition to reducing operational costs10. The recent Securities Exchange Commission’s ruling on Climate Disclosure 1 signals an increasing focus on climate risk as financial risk, heightening the need for ESG reporting as regulatory compliance.
AUTOMATION’S ENERGY OPTIMIZATION
Automation’s role in energy optimization intersects with areas such as modeling usage, improving efficiency, reducing waste, and enhancing overall energy management. For instance, monitoring fuel and steam usage to detect anomalies offers the potential for multiple system improvements. This can collectively yield savings of up to 10%–15%. The project payback period for implementing monitoring systems is generally under two years 14.
Digitalization connects facility utilities through smart facility plans. This connectivity enables key personnel to make faster decisions in real time and while maintaining control over energy consumption and optimization. Graphic interfaces and process monitoring transmit data to relevant staff for benchmarking and identifying system issues and malfunctions. This flow of information can lead to efficient, controlled, and stable energy usage and optimization.
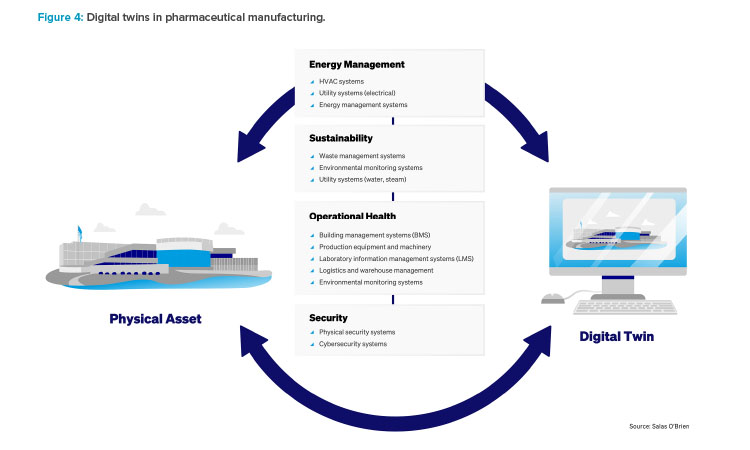
Leveraging Digital Twins: Energy Optimization
Digital twins are virtual replicas of physical entities or systems, created to simulate real-world objects, processes, or systems. These digital models are used for analysis, to predict the performance and issues of their physical counterparts, and to optimize operations or processes before applying changes in the real world. They integrate IIoT, AI, ML, and software analytics with spatial network graphs to create living digital simulation models that update and change as their physical counterparts change.
Although digital twins have been around since the 1970s, they have recently taken on a heightened importance for many life science manufacturers, from simulation and what-if analysis to life cycle management and energy optimization. They can provide a basis to clearly showcase what the facility will look like after conversion before any physical modifications take place.
A digital twin is a digital representation of a physical system and can take on many forms (asset twin, performance twin, and simulation twin). Many manufacturers have used a performance or simulation twin to model their factory and help drive energy reduction through optimization of operations. This can include real-time modifications to equipment settings or production schedules to maximize production during low-cost energy periods.
However, there is a greater potential in harnessing the power of digital twin technology with energy optimization through active modeling and settings: One can expand the power of a digital twin by modeling both the building and energy sources, using data inputs to recommend the most efficient energy sources for specific time frames.
Picture this: Based on energy profiles, a ground pump is set as the primary heat source for the next four days, strategically aligned with favorable weather conditions rather than relying on steam. This sophisticated strategy leads to substantial cost savings and makes significant contributions to carbon reduction efforts. The foresight provided by this approach allows for a more informed ESG conversion plan, seamlessly integrating sustainability into the facility’s design during conception and then extending to operations. This approach focuses on more than just energy flow visualization and IIoT sensor integration; it actively shapes energy consumption patterns for maximum efficiency and environmental impact mitigation.
Digital Twins for AI and ML
As described previously, a digital twin foundation coupled with IIoT sensors lays the groundwork for harnessing the power of AI and ML. The integration of IIoT sensors with digital twins enables the continuous collection of real-time data from various assets and processes within a manufacturing facility. This information becomes a valuable resource for AI and ML algorithms, which then analyze patterns, detect anomalies, and predict potential equipment failures.
The synergy in a facility that uses digital twins, IIoT sensors, and AI can facilitate precise energy optimization.
In addition to energy optimization, AI algorithms can forecast when equipment is likely to experience issues, allowing for proactive, predictive maintenance interventions. This reduces unplanned downtime and extends the lifespan of equipment, furthering energy optimization.
The synergy in a facility that uses digital twins, IIoT sensors, and AI can facilitate precise energy optimization. This approach reduces overall energy and enhances the reliability and efficiency of manufacturing processes.
Cybersecurity for Operational Technology
As pharmaceutical manufacturers navigate the integration of advanced digitalization strategies, it is imperative to develop a comprehensive cybersecurity framework. This framework should encompass regular security audits and vulnerability assessments to preemptively identify and mitigate potential threats. Additionally, the adoption of a zero-trust architecture is crucial, ensuring that access controls are strictly enforced. Network segmentation further fortifies this approach, allowing for controlled access and minimizing the risk of lateral movement within the network.
Integral to this cybersecurity matrix are robust firewalls and sophisticated endpoint security measures, forming a multilayered defense that safeguards critical infrastructure against evolving cyberthreats. This strategic approach to cybersecurity is not just a safeguard but a fundamental pillar supporting the integrity and resilience of pharmaceutical operations as digital automation is increasingly integrated.
Facility Conversion Roadmap
Facility conversion necessitates a structured and thoughtful approach. This will allow seamless integration of new automation technologies and digital capabilities to achieve the desired energy savings goals. The process includes the following six steps.
- Map and audit to assess the current state of the facility’s digital maturity model.
- Define the facility’s digital maturity model vision and goals.
- Implement and connect the facility’s digital maturity model action plan and roadmap.
- Monitor digital data systematically to uncover insights and identify any irregularities.
- Share relevant data and insights with key stakeholders.
- Leverage the collected data to make informed decisions and enhancements; turn information into outcomes.
LEVERAGING ESG INITIATIVES
ESG reporting and goal achievement are increasingly prioritized, whether it be through ties to executive compensation or a consideration during budget allocation. Facilities must use new tools to communicate the need for capital project spending. Greenlighting funding for a facility improvement is no longer based solely on cost and ROI. The change in environmental impact must be documented and communicated in line with corporate ESG goals. The more granular the on-site data collection, the more accurate these projections can be. In the case of digital twins, the current and proposed project can be modeled to provide this data with the upmost accuracy.
By leveraging digital twin technology for precise data collection and project modeling, companies can make compelling cases for their digitalization initiatives by showcasing the expected ESG benefits in a language that resonates with stakeholders. This approach not only facilitates the approval and funding of vital facility improvements, but also positions the company as a leader in sustainable innovation, enhancing its reputation with investors, customers, and the public.
CONCLUSION
Through smart factory initiatives, pharmaceutical facilities can optimize energy consumption across processes, from research and development to manufacturing and packaging. This aligns with ESG goals by significantly lowering carbon footprints and propels facilities toward achieving greater economic sustainability. There are many benefits of integrating environmental considerations and automation into operational strategy, including efficiency, regulatory compliance, risk mitigation, and reduction of waste and administrative expenditures.
Leveraging ESG initiatives to fund digitalization projects is a proactive financial vehicle to support sustainability goals. By doing so, pharmaceutical companies enhance their competitive edge and contribute positively to global sustainability efforts. This approach fosters a culture of responsibility and innovation, encouraging stakeholders at all levels to commit to environmentally and socially responsible practices.