A New Pharmaceutical Equipment Exposure Measurement Database

This article describes the Pharmaceutical Equipment Exposure Measurement Database (PEEM-DB), which was launched in July 2019 by the ISPE Japan Affiliate for its members. PEEM-DB is offered as a tool for rationally advancing optimal containment equipment settings by collecting exposure measurement results for pharmaceutical product manufacturing equipment and statistically analyzing the data.
The March 2015 revision of cross-contamination prevention requirements in the EU GMP guidelines1, 2 states that manufacturers must identify, assess, and control cross-contamination risks in buildings and equipment for manufacturing pharmaceutical products; these efforts are essential to optimize equipment and facility design and ensure product safety. In the manufacture of high-potency active pharmaceutical ingredients (APIs) in particular, companies must adopt appropriate containment equipment for the specific manufacturing process. However, unless the containment performance expected from the proposed equipment is quantitatively defined, equipment selection is difficult.
As stated in the ISPE Baseline Guide: Risk-Based Manufacturer of Pharmaceutical Products,3 four exposure routes can trigger cross-contamination in the manufacture of pharmaceutical products: mix-up, retention of parts that come into contact with products in shared equipment, mechanical transfer, and airborne transfer. Containment equipment for airborne transfer and mechanical transfer should be adopted in pharmaceutical product manufacturing lines. To analyze and evaluate the cross-contamination risks caused by airborne transfer and mechanical transfer, the basic principle is to evaluate the containment performance of the containment equipment. To quantitatively implement such evaluation, the exposure measurement data for the containment equipment must be statistically organized.
Exposure measurements for containment equipment have frequently been conducted by the methods described in the second edition of the ISPE Good Practice Guide: Assessing the Particulate Containment Performance of Pharmaceutical Equipment.4 Presenters at the ISPE Japan Affiliate Annual Meeting have reported cases in which pharmaceutical companies have organized the measurement results and applied them to configure settings in containment equipment. However, because the measurement results are limited and companies’ measurement approaches vary, such meth-ods have not been adequate for sharing information across the industry.
In response to these circumstances, the PEEM-DB working team in the ISPE Japan Affiliate’s Containment Community of Practice (CoP) has developed a platform for widely collecting and analyzing exposure measurement data from pharmaceutical product manufacturers, equipment manufacturers, engineering companies, and other companies related to the manufacture of pharmaceutical products. The platform thus enables implementation of quantitative methods to assess risk of airborne transfer.
Moreover, during the prototype development stage, the CoP surveyed ISPE Japan Affiliate members’ companies to determine what the companies require from this platform. We distributed a questionnaire to participants in the Containment COP workshop organized at the 2017 ISPE Japan Affiliate Annual Meeting.5 About 50% of the 70 respondents expressed the desire to use this platform, and a similar percentage requested that it be shared online for direct access by users. Also, nearly 90% of respondents expressed interest in the platform’s future development.
As a result of these efforts, PEEM-DB was created. The ISPE Japan Containment CoP administers the PEEM-DB.
Data Set
PEEM-DB is a database of the results of airborne transfer exposure measurements in containment equipment. It contains measurement data of airborne concentrations (μg/m3) of substances using lactose and other surrogate materials in manufacturing processes for drug substances and products.
For containment equipment, these data mainly target the glove box/isolator (GB), flexible glove box (FGB), fume hood/draft chamber (FH), and localized exhaust (LE) stand-alone products and assemblies. Details such as environmental conditions during equipment operation, work processes, types of powder, handled amounts, and airborne measurement locations are added to support the data analysis.
The data stored in PEEM-DB include test data results from containment performance evaluations implemented by ISPE Japan Affiliate members’ companies, mainly based on the ISPE Good Practice Guide: Assessing the Particulate Containment Performance of Pharmaceutical Equipment.4 Furthermore, the database contains results from trial exposure measurements. In total, PEEM-DB currently makes approximately 300 data items available to ISPE Japan Affiliate members.
The ISPE Japan Affiliate and the Containment CoP receive permission for use from the companies that own the data. To encourage companies to share their data, detailed data are disclosed to ISPE Japan Affiliate members only.
For data reliability, the PEEM-DB working team checks and confirms data before inputting, and the ISPE Japan Affiliate currently manages the database by linking companies, data providers, and the PEEM-DB working team. This system efficiently brings together users and participants, while maintaining security and protecting data from unrestricted modification.
Database Format
PEEM-DB uses general spreadsheet software (Microsoft Excel), and users can download the database from the Japan Affiliate website. Excel was chosen because the system is reliable and easy to use. During the selection of registered items, convenience for users and comprehensiveness of data were emphasized. Items in PEEM-DB are divided into four categories (Tables 1–4).
Item | Data Type |
---|---|
Data registration date | Date |
Containment equipment | Notation of equipment name: GB, FH, LE, RTP (rapid transport port), SC (safety cabinet), other |
Detailed equipment specifications | Notation of equipment name: TM (tableting machine), FC (film-coating machine), ML (mill), GL (granulator), other Combination notations |
Differential pressure set (negative pressure or positive pressure, kPa) | Numerical value |
Air velocities at point of use (meters per second) | Numerical value |
Item | Data Type |
---|---|
Handling form | Text: Powder, liquid, tablet, etc. |
Product process | Text: Tableting, grinding, screening, other |
Item | Data Type |
---|---|
Evaluation powder | Text: Lactose, acetaminophen, API, other |
Pharmaceutical ratio (%) | Numerical value |
Handled amount (kg) | Numerical value |
Item | Data Type |
---|---|
Data source | ext: Equipment manufacturer, pharmaceutical company, engineering company |
Work process | Text: Equipment operation, insertion, removal, washing, other |
Airborne measurement location | Text: Worker, window, port, other |
Measurement time (min) | Numerical value |
Suction pump flow (L/min) | Numerical value |
Air suction flow (L) | Numerical value |
Airborne measurement actual value (μg) | Numerical value |
Airborne concentration at measurement (μg/m3) | Numerical value |
Baseline (background) airborne measurement actual value (μg) | Numerical value |
Baseline (background) airborne concentration at measurement (μg/m3) | Numerical value |
Data Uses
As already mentioned, PEEM-DB is compiled in Microsoft Excel. The filtering feature in this software allows users to extract only required information, and the results of analysis can be visualized as graphs (see Figure 1 for examples).
A general database can be used for managing equipment-related data. For example, appropriate maintenance time can be checked and confirmed on the basis of the trend of changes overtime at the same measurement point (Figure 1, top). Because measurement conditions vary from company to company, it is difficult to compare such performance data between companies.
Despite the differences in company data, there is still considerable value to be obtained from conducting verification. Therefore, PEEM-DB actively stores various data from many companies, such as the private data held by equipment manufacturers, comparative data for equipment (Figure 1, bottom left), operating data and process-based measurement data from pharmaceutical manufacturers (Figure 1, bottom right), and other data.
Figure 2 shows examples of actual analyses implemented using PEEM-DB. Example 1 shows an airborne concentration plot for each type of equipment. It can be seen that airborne concentration from FH, SC, FGB, and GB is largely distributed within the specific occupational exposure band (OEB). Moreover, by focusing on a field with the target occupational exposure band, it can readily be seen which equipment satisfies the target. Further, an understanding of airborne concentration distribution zones containing numerous plots provides a guide for determining the appropriateness of equipment for the design occupational exposure band. Example 2 shows whether there is a correlation between measurement time and amount of recovered powder. It is confirmed that extending the measurement times does not always lead to an increase in the amount of powder.
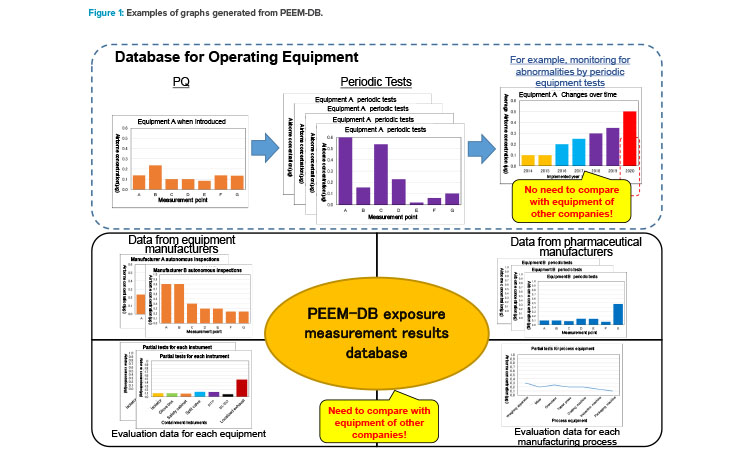
In addition to these analyses, we have attempted to conduct statistical risk evaluation through application of the process capability index (Cpk) method. Cpk is a standard indicator in the quality control field used to quantitatively evaluate the process capability of manufacturing processes. In PEEM-DB, when focusing on any equipment type, Cpk is used to quantitatively evaluate the performance stability simulated for the target occupational exposure band. For example, when Cpk is 1.00 or less, the probability of deviation is 0.3% or more, and it is assumed that the target occupational exposure band is unlikely to be met. If Cpk is 1.67 or higher, it means that the deviation occurrence rate is equal to or less than 1/1,000,000. It is also possible to reverse-calculate the extent that performance can be forecast, based on the deviation occurrence rate. Even if the target data count is small, trends can be evaluated by this method.
By filtering data for each equipment and measurement point, localized airborne concentration trends in certain equipment can also be forecast. For example, it is possible to ascertain the size and variance of airborne concentrations on the external door of the pass box, glove port, bug-out port, or other parts of the glove box.
As mentioned, because the test data stored in PEEM-DB are not based on unified conditions (e.g., target performance, purpose of use, operating method, operating time), numerical values cannot be compared. PEEM-DB is simply a collection of test data that can be used to analyze trends and generate suggestions for risk assessment and equipment design choices. It does not guarantee the performance of individual devices, nor does it provide data relevant to compliance with legal or regulatory requirements. Users must be aware at all times of patient safety, product quality, and data integrity when drawing on PEEM-DB as a resource. However, such analysis does make it possible to see trends in certain evaluation items for the equipment.
The goal is to collect a large amount of widespread data from differing measurement conditions so that PEEM-DB can be treated as “big data.” By integrating large quantities of diverse data, the analysis results obtained through statistical processing provide more accurate values, making it possible to also conduct quantitative analysis. Thus, it is expected that PEEM-DB can be used in various ways. One example is to provide base values in risk assessment.
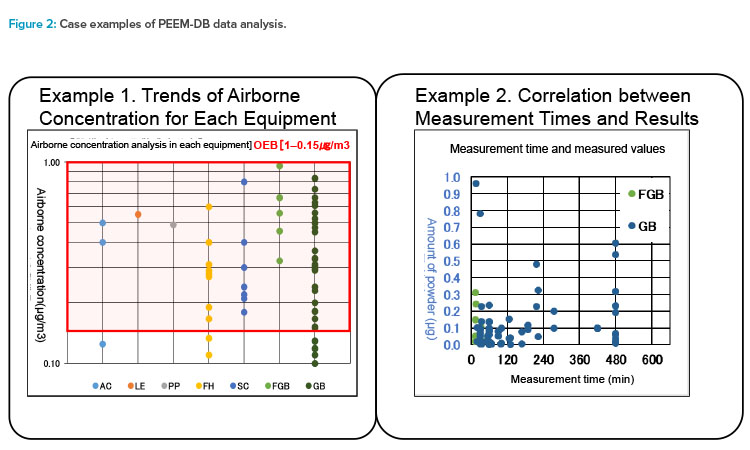
The goal is to collect a large amount of widespread data from differing measurement conditions so that PEEM-DB can be treated as “big data.”
Access
The ISPE Japan Affiliate Containment CoP has published a webpage that offers general information about PEEM-DB, and Affiliate members can download the database through the dedicated members-only page. Figure 3 shows the scope of disclosure by layer. Overviews that can be freely viewed by anyone are distinguished from detailed data that are disclosed only to Affiliate members.
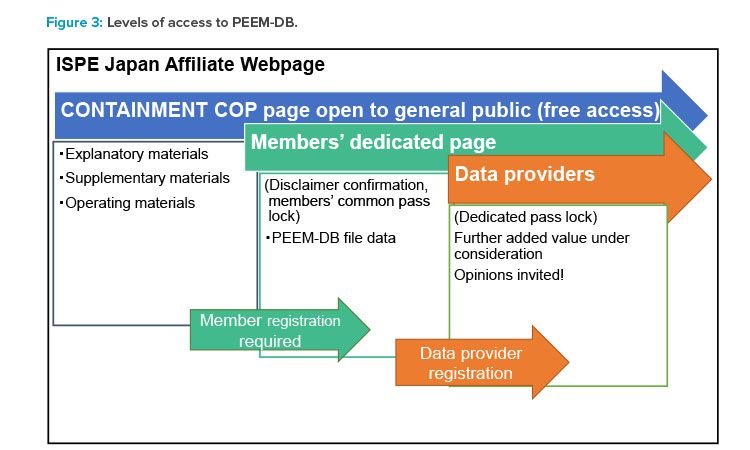
Conclusion
PEEM-DB was only very recently released and is still a limited database. From a risk assessment perspective, we believe PEEM-DB will be useful as a data-base of measurement values that can be qualitatively or quantitatively analyzed to help with containment equipment and system selection and the setting of control values. However, many issues cannot be evaluated using airborne transfer–related data alone. Therefore, it will be necessary to add data from mechanical transfer exposure measurements in the future.
The working team members are convinced that a fully developed PEEM-DB can be effectively and flexibly used. We are actively acquiring measurement test data to expand the database. Our aim is to include case studies of analysis and evaluation on the website and at the ISPE Japan Affiliate Annual Meeting, with a view to promoting and sharing PEEM-DB with ISPE members and others.
We will continue to discuss methods for acquiring and analyzing data for the effective use of PEEM-DB. Our wish is to include the participation and opinions of many from our industry in our activities.