Enabling More Efficient and Effective C&Q Through GEP

When the ISPE Baseline Guide Vol. 5, Commissioning & Qualification, 2 ed. was published in 2019, most of the attention was focused on the incorporation of quality risk management (QRM) into the integrated commissioning and qualification (C&Q) approach. That attention was merited, as the guide established the industry-standard approach, strategy, and rationale for science- and risk-based design and delivery of engineered systems. However, equally important from both a business and regulatory perspective, the guide established good engineering practice (GEP) as a key enabler for the integrated C&Q process. Just as QRM drives effectiveness of the integrated C&Q process, GEP drives the efficiency of that process.
The 2021 publication of the ISPE Good Practice Guide: Good Engineering Practice, 2nd ed., (GEP GPG) updated the definition and understanding of GEP within a regulated industry, establishing GEP as a life-cycle approach supporting the effective, efficient design and delivery of engineered systems and enabling the QRM-based integrated C&Q process.
An effective C&Q process results in systems that are installed and operating in a manner fit for intended use and meeting all user requirements and stakeholder expectations. For critical systems, fitness for intended use is defined by system critical design elements (CDEs) being installed and operating in a manner to deliver system critical aspects, which ensures system performance to control critical process parameters (CPPs) and process performance to produce product meeting its critical quality attributes (CQAs).
Aligning with the ISPE Baseline Guide Vol. 5, Commissioning & Qualification, 2 ed., the GEP GPG recognized GEP as a life-cycle approach, encompassing “all aspects of engineering related to the design, delivery, and operation of facilities and engineered systems, from conceptual design to retirement.” Maintaining the qualified state of critical systems with focus on CDEs throughout their operational lifetime is in the scope of qualification per good manufacturing practices (GMP), whereas maintaining engineered systems installed and operating in a manner fit for their intended use falls under the scope of GEP core concepts and practices. This article discusses the application of GEP to enable more efficient and effective C&Q primarily within the scope of the design and delivery of engineered systems (i.e., through system acceptance and release).
System Life-Cycle Processes
Application of engineering change management (ECM), engineering document management, and engineering issue management throughout the C&Q process can significantly reduce time, cost, effort, and risk. These systems ensure that management efforts are properly scaled to risk, complexity, and system life-cycle stage and that management decisions are risk-based and are led by appropriate SMEs. Appropriate ECM and document management ensures that proposed changes are identified, assessed for impact, implemented, and verified. Appropriate engineering issue management, including issues, punch lists, and discrepancies, ensures that observed issues are properly identified, managed, investigated, resolved, and verified (see Figure 1).
During the requirements definition and specification and design stages, ECM ensures that changes to key documentation, including user requirements specifications (URS) and the design development, are managed appropriately. Engineering issue management ensures that design issues identified through design review are tracked and managed to resolution.
During the build/construction, installation, and verification stages, project ECM ensures that changes to design and implementation are managed appropriately, with quality oversight focusing on CDE-related changes only. Punch list management ensures that issues observed during build, construction, and installation are managed appropriately. Discrepancy management during verification ensures that verification testing and documentation discrepancies are documented and resolved appropriately.
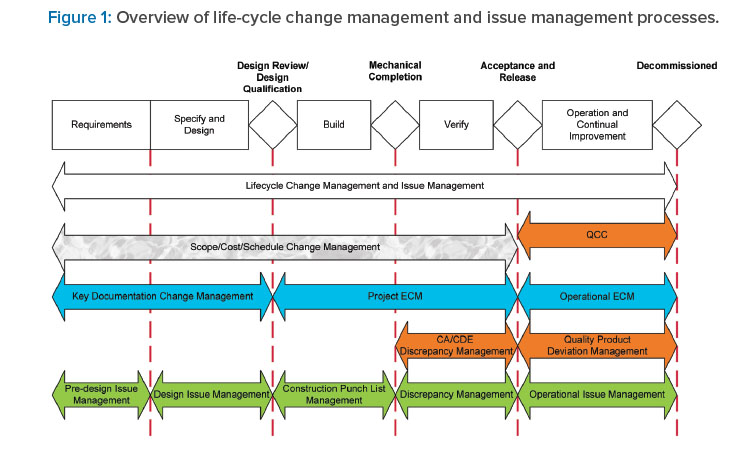
Documentation of these changes and issues provides traceability of the system state throughout the design and delivery process and as such is critical to eventual acceptance and release of systems. The acceptability of documented engineering management of system and documentation changes and design/build/verification issues represents a key driver of system acceptance and release to manufacturing by the quality unit, which ultimately defines the effectiveness and efficiency of the C&Q process.
Project Engineering-Related Practices
Robust application of risk management through the project execution plan, including use of a project risk register, can help identify, prioritize, and control project risks to scope, schedule, and budget, as well as risks to the quality of the delivered system. Risks identified early in a project are generally easier and mostly less costly to control. Rigorous control, monitoring, and reporting of project costs drives cost-effective delivery of engineered systems.
System Design-Related Practices
Since rigor of system design and delivery must be commensurate with risk (particularly risk to product quality and patient safety), correct identification of systems and process functionality that potentially impact product quality and patient safety play a significant role in ensuring that overall effort and documentation of the C&Q process is right sized in terms of scope, schedule, and cost. Accordingly, determination of system boundaries and appropriate definition of system user requirements directly impacts the strategy, effectiveness, and efficiency of the C&Q process. System boundary definitions should consider inclusion/exclusion of CDEs, system intended use, anticipated future system modifications, physical interfaces to other systems, and linkages to automation, control systems, and data handling and storage.
A typical industry example is design of cleanrooms and the HVAC systems that supply them, where the cleanroom is the quality impacting system and the HVAC system is a separate system with a terminal HEPA filter at the system boundary. Where the system boundary can be defined such that the HEPA filter is included in either the cleanroom or the HVAC system, the boundary decision will have significant impact on the scope, schedule, and cost incurred in design and delivery of the two systems. This typically is decided in an early stage of the project. Including the HEPA filter with the cleanroom ensures that all CDEs for the two systems are contained within the boundary of a single, direct-impact system (the cleanroom), resulting in the HVAC system not being direct-impact and significantly minimizing the rigor and documentation required to design and deliver the HVAC system. Alternately, including the HEPA filter with the HVAC system results in CDEs being included within the boundaries of both systems, which are then both direct-impact systems, significantly increasing the rigor and documentation required to design, deliver, and maintain the HVAC system.
System requirements definition through the URS should align with system boundary definitions. The URS then becomes the driver for demonstrating that a system is fit for intended use through verification activities that document system installation and operation conform to the URS. Well-defined user requirements thus drive the effectiveness and efficiency of the C&Q process.
What is specified in the URS must generally be demonstrated and documented through the C&Q process; therefore, the efficiency of the C&Q process can be significantly impacted by the scope and quality of the URS. The URS should include system/equipment CPPs traceable to product CQAs delivered or impacted by the system. Requirements should focus on key stakeholder requirements—what is required of the system—and should generally not include engineering standards/specifications, design definitions/assumptions (how the system will be implemented) or vendor contractual obligations. Requirements should be differentiated between those that potentially impact product quality and patient safety and those that do not, such as business- or safety-related requirements. Requirement specifications should be SMART: specific, measurable, achievable, realistic, and traceable. SMART requirement specifications lead to SMART design specifications and SMART verification acceptance criteria, and therefore directly impact the scope, time, and cost associated with system design and delivery.
Design review plays one of the most critical roles in driving effectiveness and efficiency of the C&Q process. A robust design review process ensures that the design definition satisfies both the quality impacting and non-quality impacting user requirements, identifies and manages design discrepancies to resolution through application of engineering issue management, and therefore minimizes the time and cost associated with resolution of design issues, particularly when compared to the cost of issue resolution during verification of systems following build/construction and installation.
System Delivery Practices
Applying risk management to vendor selection and management can have significant impact on delivery of systems meeting user requirements and on the suitability of vendor documentation to demonstrate system fitness for intended use. Appropriate vendor management can significantly impact overall time and cost for system design and delivery. Ensuring vendors follow GEP for system design and build, including vendor document, change, and issue management, will reduce design/build time and cost, will minimize issues that must be resolved later in the project (such as during factory acceptance testing or post-delivery/site acceptance testing), and will increase the likelihood of suitability of vendor documentation to contribute to the overall verification effort and documentation. Where vendor documentation is suitable for verification, non-value-added redundant verification testing and its associated costs, schedule, and resources can be significantly reduced or eliminated.
Established GEP procedures for construction, handover, and startup similarly ensure that documentation produced during these activities can contribute to the overall verification effort while minimizing rework and testing redundancy.
Engineering Quality Process: The Enabler
Finally, development of an engineering quality process (EQP) ensures that the quality unit is aligned with application of GEP to design and deliver critical systems and that engineering documentation produced through the C&Q process is suitable to accept and release systems for use in manufacturing. The EQP provides a means for the quality unit, through auditing and other appropriate oversight, to develop trust in the established and maturing GEP processes used to design and deliver engineered systems through the C&Q process.
Unlike in the legacy C&Q process, where direct quality oversight (review, pre- and postapproval, and use of “quality” protocols) was required to “leverage” engineering verification testing and documentation into qualification, the QRM-based integrated C&Q process applies the principle that engineering testing and documentation produced by appropriate subject matter experts and following appropriate, established GEP procedures stands on its own. The EQP provides the critical linkage between established GEPs that yield engineering verification testing and documentation and the requirements of the quality unit to accept it. As stated in the GEP GPG, “The purpose of establishing an EQP is not to introduce quality oversight and control of engineering activities performed under established GEP, but rather to provide a mechanism for quality to provide appropriate oversight of engineering management and control of GEP processes, so that those GEP processes can be applied by engineering in the delivery of critical (quality impacting) systems through the C&Q process.” (Good Practice Guide: Good Engineering Practice 2nd Edition, Chapter 13, Enablers–Engineering Quality Process [EQP], Section 13.1.1, Purpose).
Conclusion
The effectiveness and efficiency of design and delivery of engineered systems and facilities play a crucial role in speed to patient. Applying GEP ensures that design and delivery efforts are commensurate with risk; engineered systems and facilities are delivered in a state of installation and operation fit for intended purpose; and unnecessary overhead, oversight, testing and documentation redundancy and overall scope, schedule, and cost are minimized.