Process Architecture and Integrated Design in the Pharmaceutical Sector

Large engineering companies specializing in the industrial production sector have increasingly been adding process architects to their teams to address the need for expert designers in this specialized field. Process architects play a key role in designing industrial plants, particularly for pharmaceutical production facilities.
In fact, these sites must meet architectural criteria while addressing complex technological needs with particular attention to integrating various disciplines, such as Process Engineering and Mechanical, Electrical, and Plumbing (MEP) Engineering, while ensuring compliance with Good Manufacturing Practices (GMP) and Health, Safety, and Environment (HSE) regulations.
Architects are accustomed to working in multidisciplinary teams, and on intricate projects. They have strong three-dimensional thinking and act as design integrators, collaborating across the diverse disciplines involved.
A process architect can play a significant role in making designs more sustainable and help reduce environmental impact (e.g., water and energy consumption, emissions, and solid waste). By using a “Value Engineering and Cost Reduction” design approach, they reduce the consumption of water and energy, reduce emissions, and manage solid waste more effectively. Additionally, they can integrate sustainability principles into the design process, aligning with the concept of the “Facility of the Future,” which focuses on innovative, efficient, and sustainable facility designs.
Background
Process architects are becoming more important in the life sciences industry because their evolving role as systems integrators aligns with the demand for modular solutions, promising enhanced quality, reduced costs, and expedited project delivery. There is not a specific degree and educational path for this professional role—it is an expertise that would be achieved and consolidated through years of professional experience. This is why it is usually hard for engineering societies to find a process architect within the job market, especially considering that specialized professionals are usually only motivated by certain types of projects.
Process Architect Role and Responsibilities
The responsibilities of a process architect consist of the following: assessing the site; planning the facility; establishing a benchmarking repository to define parameters and objectives; managing project development and process analysis; defining material and personnel flow; overseeing feasibility studies; completing presentations and processing documentation for approval; issuing construction drawings and producing specifications; estimating cost, reviewing and approving workshop drawings; and managing and supervising construction.
At the beginning of a project, it is essential to define the role and responsibilities of the process architect on the team. That definition leads to better building and process as well as better customer and user outcomes.
Equipment
When developing the layout, it is essential to address the integration of the equipment in the early stages of the design process. Once equipment is selected—usually together with the clients—then operating heights, maintenance access, flows, and delivery logistics are addressed. Initial design is typically based on generic equipment drawings or, if parameters are unknown, using worst-case scenarios. In particular, personnel and materials into and out of the production area determine the room adjacencies.
Contamination Control
Developing strategies for clothes changing and washing should be defined and simplified according to the local customs and clients’ internal procedures, always keeping contamination control in mind. Concerns about sterility should be reviewed with all interested parties, including the HSE. One interesting example case relating to general lockers is the idea of flexible lockers. These lockers could have mobile partitions between dedicated changing rooms for men and women, with the possibility to move these partitions according to a facility’s employee numbers.
The process architect often works in the modernization of existing plants. Modifications and renovations represent a different set of challenges. These include feasibility studies and constructability reviews, aiming to define new move in/out of equipment, and definitions of temporary partitions for process segregation.
Circulation spaces for transferring materials and personnel within the facility require large amounts of expensive space. Planning an adequate number of airlocks requires accurate information on the current required current GMP (cGMP) zone classifications, biocontainment, and required pressurization.
Other Design Criteria
Other design criteria to examine include the ergonomics of the machines and the degree of product handling, as well as biological and toxicity levels for hazardous products such as flammable corrosives. In case of ATEX (explosive atmospheres) considerations, the type of finishes and the layout for the room should be carefully considered, especially if these rooms occur in a classified production area.
Design Process
The design process could be described as follows:
- Collect user requirements (URS)
- Establish context
- Complete adjacency diagrams
- Define project scope
- Develop options
- Finalize the selected option
- Develop the layout
- Determine equipment allocation and ergonomics
- Determine classes
- Verify personnel and material flows
- Ensure spatial interdisciplinary coordination
The design process of a laboratory is similar, but flows are different and could not be required in a GMP assessment.
Modernization and Renovation
The process architect often works in the modernization of existing plants. Modifications and renovations represent a different set of challenges. These include feasibility studies and constructability reviews, aiming to define move in/out of equipment, and definitions of temporary partitions for process segregation. This is to guarantee the functionalities of the existing department for client sustainability goals (an increasingly significant factor).
In some case studies, process architects evaluate the flexibility of layout with respect to scale-up considerations. For example, if the clients evaluate to proceed with a 600/900-liter bioreactor, the layout should incorporate enough wide corridors, big doors, and proper ceiling height to allow the bioreactor in and out. Further, operational space for maintenance on top of the bioreactor should be considered by the process architect by designing a ceiling with enough height in certain areas of the room.
Sustainability
In the context of a facility design, sustainability could be addressed in many ways; for example through the box-in-box approach and modular design; closed process and ballroom layout, the use of disposable equipment instead of stainless steel; integrating a plug and play approach; reduced rooms segregation and areas classification (e.g., heating, ventilation, and air conditioning [HVAC]); and risk analysis and Lean design.
Product Considerations
The facility is designed and built to ensure and test the product and, ultimately, to provide a safe, effective product. Multiple decisions impact facility design. These include decisions made regarding filling format, technology, regulations, and batch size, among many other things. For example, deciding between using a restricted access barrier systems (RABS) or isolator is probably the single largest decision that can be made regarding facility design.
Another example is the final product format (e.g., vials, cartridges, or syringes; liquid or lyophilized; aseptic or terminally sterilized; single or multi-product). Moreover, commercial decisions determine the reason for the facility. For example:
- Who is the customer?
- Will it involve clinical trials?
- Is it a commercial product?
- Is it liquid or lyophilized? Aseptic or terminally sterilized?
- Is it a single or multi-product?
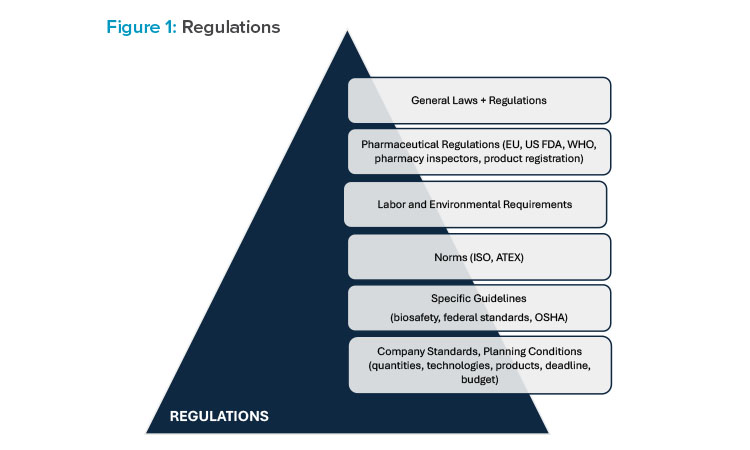
General |
|
---|---|
Flows |
|
Finishes |
|
Coordination with Technical Disciplines |
|
Maximum Personnel Requirements |
|
Tools |
|
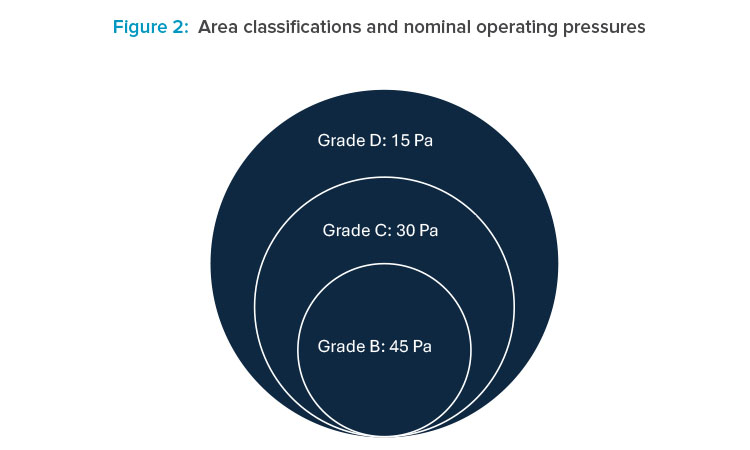
Process Architect Knowledge
The process architect is responsible for understanding, defining, and prioritizing the needs and expectations of the customer. This includes considering how format and batch size decisions impact facility design, as well as the specific requirements of different customer markets (e.g., EU, Japan, US). Therefore, the process architect must possess a specific set of skills and knowledge. It is helpful to propose a checklist of the required knowledge (see Table 1).
Project User Requirement Specifications
The layout of a pharmaceutical manufacturing plant should be designed based on the needs of the facility. The needs of the structure are identified during the planning phase, where the company must clearly define its actual needs. It is essential that we separate “must have” objectives from non-strategic objectives, which may require conducting a formal decision analysis. This is often a very time-consuming endeavor, since each department needs to weigh what is truly necessary for their business versus those items that are not essential to operations. A facility should be designed to anticipate its needs in two-, five-, and ten-year increments.
The architectural design must consider optimal room finishes, client standards, local customs, environmental and safety considerations, and compliance with building and fire regulations. Additionally, the external structure and finishes of buildings should account for the internal environment, minimizing the use of columns and expansion joints within in clean areas of production facilities. The layout must be an integrated project meeting the following requirements:
- Project cost and schedule
- Compliance with GMP
- User requirements
- Equipment layout and equipment requirements
- Personnel and material flows (product, component, and raw material)
- Operational access requirements
- Maintenance access requirements
- Cost considerations in layout design
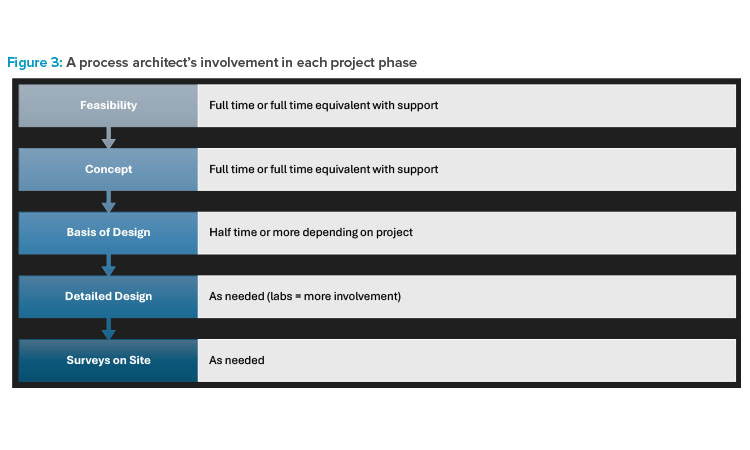
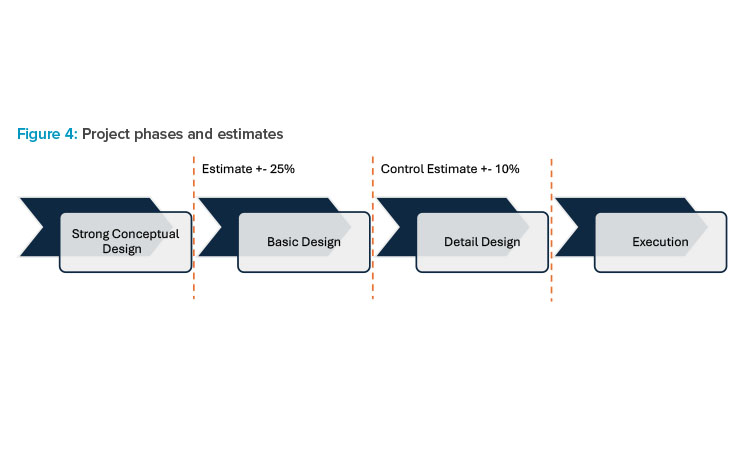
User Requirements
The designer must first understand the requirements of the product and the process, precisely clarifying the number and dimensions of the rooms that will be required; relationships between the groups of rooms; finishes, equipment, and furniture suitable for carrying out the various functions; and the environmental conditions (temperature, humidity, air movement, sound insulation, etc.).
The process architect has a role in defining the layout, particularly during the initial phases. This involves privileged interactions with the customer and various disciplines, as well as overseeing the spatial coordination of structures, equipment, and systems.
Equipment Layout and Requirements
Equipment layouts, also called logic diagrams, and equipment requirements ensure the optimum flow of materials and personnel. They should define all the areas that can influence the operations necessary for production, as well as the relationships between them. These are derived from program and equipment sizing needs and can be developed once the process is known. Equipment sizes are indicated using blocks and room groups are assembled based on necessary adjacencies and process requirements.
Dressing Requirements
Dressing rooms play a fundamental role in layout. Locker rooms have two grades (or, levels) of changing rooms. Low standard, which includes normal (civilian) clothes to factory (clean) clothes. High standard includes clean clothing to full coverage coveralls.
Project Phases
It is extremely important not to skip design levels. The strategic decision to invest in a strong conceptual design leads to the following advantages:
- Low initial costs
- Feasibility study
- Advance clarification of the main project themes
- Stronger decision-making tool
- Possibility to develop alternatives/brainstorming
- Customer orientation
Based on the process outlined in the workflow diagram (see Figure 5), the project engineer interfaces directly with the technical disciplines, responding to the pharmacy manager for the correct flow of project information.
The process architect has a role in defining the layout, particularly during the initial phases. This involves privileged interactions with the customer and various disciplines, as well as overseeing the spatial coordination of structures, equipment, and systems (i.e., space management).
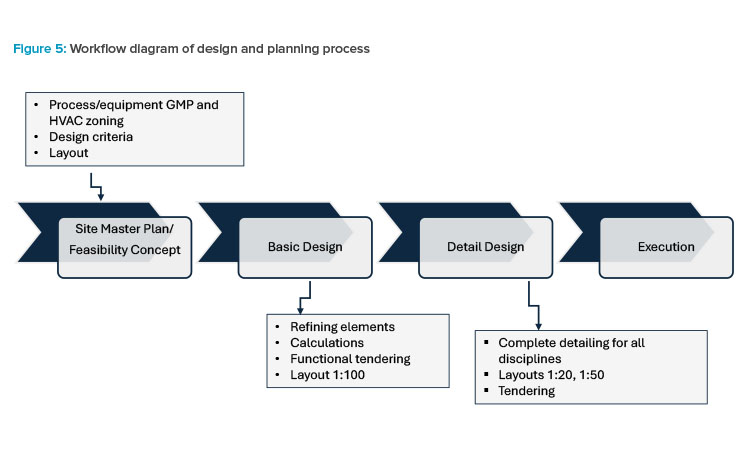
Final Considerations
It is worth focusing on the current state of the process architect profession and on future market trends in the field of industrial production, especially sustainability goals. The evolution of the life science sector is driving the need for new manufacturing paradigms based on advanced technologies. As a result, process architects must transform themselves into systems integrators to best meet customer needs for fast manufacturing facilities.
For example, the constant introduction of new and innovative modular manufacturing solutions is creating significant opportunities for the lifespan and costs of future manufacturing facilities. Today, process architects are expanding their role as systems engineers and integrators focused on finding the best way to execute a project using modular and pre-engineered systems, through the design of the structure with the clear objective of improving quality while reducing costs and time needed to deliver a project. The demand for this enhanced role is highlighted by requests from numerous companies asking for modular platform and system designs that take advantage of modular, pre-engineered components.
The evolution of the life science sector is driving the need for new manufacturing paradigms based on advanced technologies. As a result, process architects must transform themselves into systems integrators to best meet customer needs for fast manufacturing facilities.
A modern pharmaceutical production plant must be flexible and adaptable, not only to have the ability to scale up inventories to meet growing market demands, but also to have the flexibility needed to accommodate changes in production machinery needs. Process architects should come to understand clients corporate culture and their short- and long-term goals, whether a new facility is being designed or an existing facility is expanded or updated. In fact, design often takes place while production processes are still in the development phase. Thanks to this knowledge, process architects can act as true technical coordinators.