ISPE’s new Good Practice Guide: Equipment Reliability provides practical guidance to help pharmaceutical organizations proactively improve equipment reliability at all stages of the equipment life cycle, from design to decommissioning. This guide focuses on the systematic reduction of equipment performance variation and its operating impact through improved equipment design and management. It addresses the events and consequences of equipment failure, while providing guidance on effective tools and strategies for an effective reliability program.
Produced and reviewed by industry experts, the guide is a must-have reference for anyone who is involved with designing, implementing, operating, or maintaining equipment assets.
“As innovation extends to and transforms the supply chain, equipment life-cycle costs and availability become ever more relevant to maintaining a competitive advantage,” said Michael Berkey, Guide Team Lead, and Associate Director, Merck & Co., Inc., Kenilworth, New Jersey, US. “The strategy and tactics of reliability can help companies maintain the value of their equipment throughout its useful life and mission, and the application of asset management principles can help companies leverage equipment toward a competitive advantage.”
Learn More & Purchase
Meet the ISPE Staff: Linda Walls
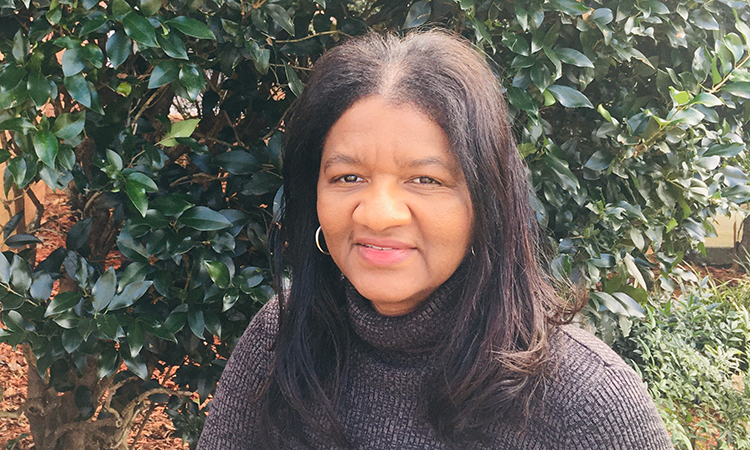
In each issue of Pharmaceutical Engineering®, we introduce a member of the ISPE staff who provides ISPE members with key information and services. Meet Carrie Marina McManus, Manager, Volunteer Engagement and Development, Member Services Department.
Tell us about your role at ISPE: what do you do each day?
I joined ISPE in 2009 as a Data Services Coordinator. In 2013, I was promoted to Manager, Data Production and Analysis, and in 2019 the position moved from the Membership group to IT. This change increased the responsibility of data analysis and reporting from one department to supporting the entire organization.
In addition to data analytics, I troubleshoot association management systems (AMS) issues, test new enhancements, assist with event setup, and manage small projects.
I am a native Floridian (US) and a cum laude graduate of Florida A & M University. I hold a bachelor of science in computer information systems.
What do you love about your job?
To hear these five words from management and colleagues is very rewarding: “The data is very helpful.”
What do you like to do when you are not at work?
I am a caregiver for my 88-year-old mother who has dementia. During the global pandemic, I enjoy reading (the best book ever written is the Bible) and taking walks with my dog, Roscoe.