Acceptable Discoloration Levels on Pharmaceutical Weld Beads

Welds used in biopharmaceutical manufacturing must meet critical criteria to maintain a defined level of purity and bioburden control. One highly debated area of concern is the level of discoloration allowable on the product contact surfaces in the welded condition and secondary finishing methods. This article addresses the studies commissioned by the American Society for Mechanical Engineers (ASME) to determine the allowed discoloration in the heat affected zone (HAZ) and weld bead.
Discoloration of stainless steel welds and HAZs are visible evidence of various thicknesses and compositions of oxides, hydroxides, and other surface contaminants formed during welding. If these levels of discoloration are significant enough, they have the potential to contaminate the drug product, reduce the corrosion resistance of the metal, and reduce the life cycle of the piping system.
Therefore, appropriate levels of discoloration of welds made in the construction of process equipment and piping systems, such as those used in the manufacture of biopharmaceuticals, are highly debated within the pharmaceutical industry.
Numerous independent studies to determine acceptability of weld and HAZ color have been performed. Although these studies have impacted, improved, and modified published information over the years within manufacturing standards, levels of weld color acceptability remained unanswered. In 2020, the ASME Bioprocessing Equipment (BPE) Subcommittee on Material Joining (MJ) commissioned studies to answer the question and end the debate on discoloration allowed in the HAZ of the weld and any color within the weld bead itself.
BACKGROUND
The ASME BPE Standard addressed weld discoloration by referencing the American Welding Society (AWS) D18.2 color chart 1 in the 2002–2009 editions. In 2004, an additional study was conducted by Ernie Benway and Sunniva Collins of Swagelok Company to identify acceptable discoloration levels on the weld bead and HAZ 2. The test was conducted on type 316L stainless steel tubes using the ASTM G150 critical pitting temperature (CPT) test. At the time, the results of this study were considered proprietary information.
The summary of that report stated: “All samples were visually inspected under a microscope at 10X magnification. CPT results illustrate in both electropolished (EP) and mechanically polished (MP) conditions, that as the oxygen increases, the pitting resistance decreases as measured in 1M [sodium chloride] NaCl. Pitting occurred in most samples in the HAZ, both upstream and downstream of the weld bead”2.
In 2010, another study was performed using representative discoloration levels in the HAZ and was published in Pharmaceutical Engineering® in November 2011 3. In this case, a modified ASTM G61 cyclic polarization test was used to determine the critical pitting potential of each sample. The study concluded:
“ Even with color in the HAZs, enhancements such as passivation, electrochemical cleaning, or electropolishing when performed properly will further improve the corrosion resistance in that area of concern. The passivation process may not completely remove color from the HAZ but will improve the corrosion resistance to acceptable levels. Electrochemical cleaning and electropolishing will not only remove the color from the welds and HAZ, but also improve corrosion resistance to acceptable ranges without requiring welds be ground to remove metal and without further passivation processes. A color chart recognizing the effects of color for electropolished material should be developed and adopted for the pharmaceutical industry showing accurate acceptable levels of color” 3.
Based on these 2004 and 2010 studies, the 2012 edition of the BPE Standard was published with color charts developed by the BPE MJ subcommittee with expanded discoloration levels more focused at lower concentrations of oxygen as needed in that industry, and the reference to AWS D18.2 1 was dropped at that time. The new BPE color chart provided color photographs of welds on both MP and EP interior surfaces of 316L stainless steel tubing 4,5.
Each study had identical results on acceptable color by delineating when and where pitting started to initiate. These studies again centered on the acceptable levels of discoloration in the HAZ and not on the weld bead itself, thus the impetus for the wording on the initial ASME BPE color charts allowing “a light blue to straw color” in the HAZ with “none allowed” on the weld bead itself 2. Since initial publication, the ASME BPE color charts have had some minor revisions to clarify the intended area of view of the weld bead and HAZ on the weld samples and to reflect changes in the acceptance criteria, as shown in the MJ tables, where no color is allowed on the weld bead.
The release of the raw data from the original corrosion tests performed in 2004 indicated that the testing did include the weld bead, as well as the HAZ. The MJ subcommittee’s attention then shifted focus to the amount of allowable discoloration levels not only in the HAZ but also on the weld bead itself. Additional testing was commissioned by MJ representatives, which involved independent laboratories to verify the results of the previous corrosion testing. ASTM G61 cyclic polarization testing evaluates the impact on corrosion resistance caused by residual color from the welding process in the HAZ as well as specifically on the weld bead. A testing protocol was developed and approved by the members of the MJ Subcommittee Task Group.
TESTING PROTOCOL
The purpose of this study is to examine the corrosion resistance effects of weld discoloration on both the weld bead and the HAZ in sanitary process welds. Currently the BPE Standard and industry subject matter experts have stated that any residual color from the welding process ( automatic orbital gas tungsten arc welding [GTAW]) that may be acceptable in the HAZ is not allowed on the weld bead. This study was designed to test sanitary weld samples with color in the HAZ as well as any corresponding color on the weld bead for any impact on corrosion resistance with color in the weld bead.
The testing method used is the ASTM G61 cyclic potation dynamic polarization test, which determines the susceptibility to initiation of localized corrosion given by the potential at which the anodic current increases rapidly due to the initiation of pitting. The solution used in this test program will be identical to the solution used in previous BPE testing for evaluating heat tint. The test area on each specimen will be chosen to evaluate both the HAZ and weld bead areas.
This testing determines the critical pitting potential (CPP) and provides a detailed description of the location of the attack and whether it occurred in the HAZ or weld bead. The coupons of 316L (ASTM A269/A270) stainless steel tubing were welded with automatic welding equipment. Oxygen was introduced into the inside diameter (ID) and monitored with O2 analyzers controlling the O2 levels to match the colors previously documented and illustrated in the ASME BPE color chart.
Both EP and MP coupons were tested using the same protocol and test parameters meeting ASME BPE color chart colors #3 and #4. The inside of the test coupons remain in the as-welded condition. No post-weld treatment or passivation was performed. MJ reviewed the data and added changes to its acceptance criteria to accept corresponding color on the weld bead area as shown in the color charts of the BPE and data from this study. Parts or all the information obtained may be used for inclusion into the BPE Standard, Part MJ, subsequent nonmandatory appendices, and industry white papers.
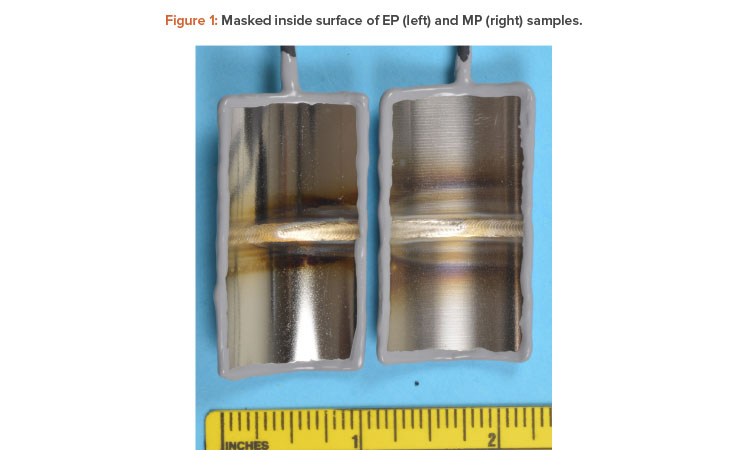
Initial Delay (open circuit monitoring ) : | 1 hour |
initial potential: | 1- hour open circuit potential ( Eco) |
scan rate | 0.167 millivolt per seconds ( mV/S) |
Maximum Potential : | 1 volt (V) |
final potential: | 1- hour Eco |
TESTING
The test samples were approximately a 1-inch segment, 2-inches long, cut from a 2-inch x 0.065-inch wall 316L stainless steel tube containing an orbital weld. The prepared pre-test samples are shown in Figure 1. The ID surface was designated as the test surface. Each sample was prepared by spot welding a 1/16-inch-diameter wire to the backside outside diameter (OD). The wire connection, backside, and edges were masked with silicone paint (see Figure 1). The exposed ID surface was measured to be approximately 11 cm2 A standard three electrode electrochemical cell as described in ASTM
G61 was used with an appropriate verified counter electrode, reference electrode, and the prepared samples as the working electrodes. The solution was deuterated with nitrogen prior to and during the test periods, maintained at 25oC. The immersed electrodes were connected to a calibrated Gamry Instruments potentiated. Each potentiated was programmed to perform the ASTM G61 test with the parameters as listed in Table 1.
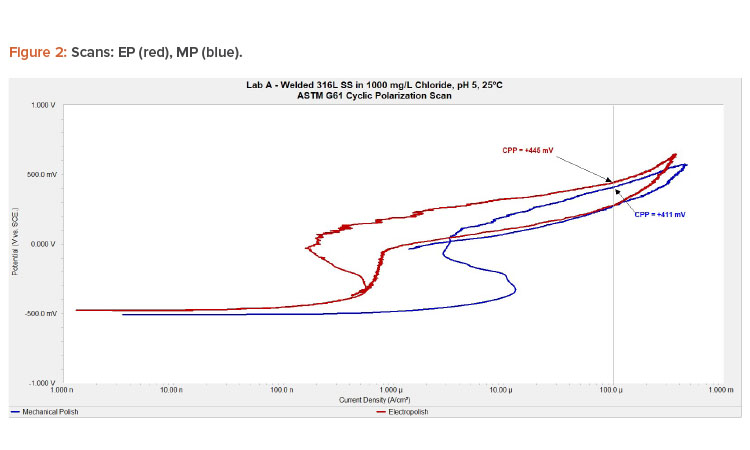
sample | cpp |
---|---|
MP | +411 |
EP | +445 |
The collected potential and current data were plotted using Gamry’s Echem software. All specimens exhibited similar behavior. The CPP was determined as the potential at which the current density exceeds 100 μA/cm2 (see Table 2).
Overlays of the plotted electrochemical data are presented in Figure 2.
Visual examination of the exposed test specimens confirmed the presence of pitting corrosion on each sample primarily in the HAZ of all samples. Little or no pitting occurred on the weld bead and non-HAZ tube area. Individual close-up images of the weld bead and HAZ areas are presented in Figure 3.
SUMMARY
The review of past available data provided results that showed a lower level of color present on the weld bead with a higher level of corrosion resistance based on the CPP data. The location and amount of pitting occurring on the weld bead was much less compared to the HAZ. The testing, earlier described, was then performed to confirm these historical results and suggest changes in the weld acceptance criteria in the MJ tables. This was to allow for color on the weld bead, as shown in the MJ color chart for the weld bead, to be acceptable as in the HAZ.
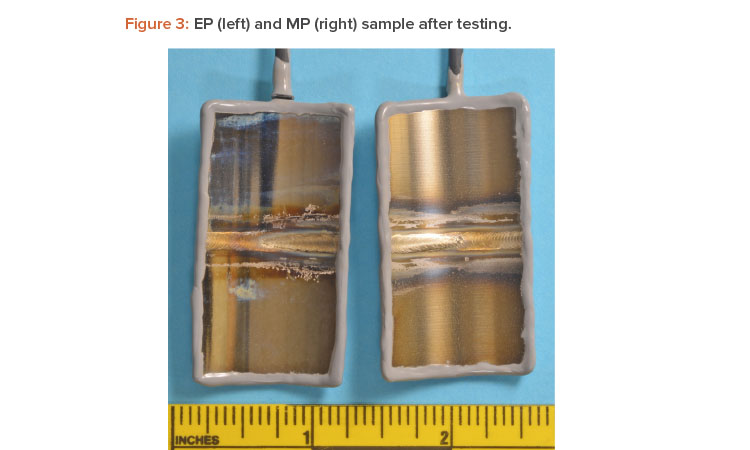
The need for this work was based on two previous studies that evaluated acceptable levels of weld discoloration. This study proved that the light color on the weld bead, as seen in the color charts and in this study, provided little or no pitting corrosion and should be within the acceptance criteria.
The following technical studies provided the basis for observations that some level of discoloration was present on weld beads that otherwise met the BPE weld acceptance criteria in MJ’s tables for the HAZ. They also provided corrosion testing data that could confirm that pitting initiation occurred in the HAZ and not the weld bead itself with a very small amount of pitting occurring on the tubing base metal area outside the weld.
2004 Study (Released in 2020)
This study 2evaluated the CPT of 316L stainless steel (MP and EP) welds made with varying levels of oxygen in the shielding gas. The tests were performed in accordance with ASTM G150 using 1M NaCl as the electrolyte as in this and other BPE studies. The results showed that CPT values decreased with increasing oxygen content, with the EP samples performing better than the MP samples. Post-test visual examination revealed that pitting was primarily in the HAZ with significantly fewer or no pits in the weld bead or base metal.
This study tested 110 coupons within 18 groups comparing EP and MP 316L stainless steel at oxygen exposure limits of 10–500 ppm oxygen. These samples were tested for CPT in accordance with ASTM G150 using 1M NaCl solution and visually inspected for color and pit location.
Interestingly, the results showed that of the 14 samples at 50 ppm oxygen exposure welds, their CPT averaged 11.0°C for EP samples and 6.2°C for MP samples. The pit locations for the 50 ppm oxygen coupons and all other 96 samples showed the weld bead had the lowest number of pits identified in the entire weld area, while the HAZ area was significantly higher (10–50 times more than on the weld bead).
2011 Study
This study 3determined the critical pitting potential (CPP) of 316L stainless steel (MP and EP) welds made with varying levels of oxygen. The purpose of this test program was to relate pitting corrosion resistance to weld discoloration and evaluate the effect post-weld surface treatments may have on corrosion resistance. The tests were performed in accordance with ASTM G61 and modified to use an alternate test solution: 1,000 ppm chloride as NaCl at a pH of 5.0.
The results showed decreasing resistance to pitting corrosion (lower CPP values) with increasing oxygen (discoloration). When performed properly, post weld surface treatments were determined to be effective at increasing the CPP values of discolored welds. The data also indicated that the CPP values of base metal and weld metal were higher than values obtained on the HAZ.
This article 3 contains data showing that welds made at or near 50 ppm oxygen exposure in the purge gas during welding compared to the AWS D 18.2 color chart at level #3. These welds produced test results that this level of weld color “will have no effect on the corrosion resistance recognized in the pharmaceutical industry for EP 316L stainless steel material” 3. The study used 13 samples that were studied at weld conditions from 316L base material with welding shielding gas at 20, 50, and 80 ppm oxygen, with and without electropolishing and passivation treatments.
CONCLUSION
The referenced studies presented facts that were used to guide the current investigation. The current study was undertaken to confirm that the HAZ of a 316L stainless steel weld with discoloration was more susceptible to pitting corrosion than the weld bead with lower amounts of color or surrounding base metal when tested per ASTM G61 using the modified test solution. The results from this study confirm that the weld bead can have corresponding color and be acceptable. The HAZ is the more susceptible area of a discolored weld. This is because observed pitting was predominantly in the HAZ with little or no pitting in the weld bead or base metal.
The results from all four studies demonstrate that the weld HAZ is more prone to pitting corrosion than the weld bead or base metal. The criteria for color acceptance on the weld bead was correctly changed from “no color” to “acknowledged color” from the color charts on the weld bead as confirmed in this study.
Acknowledgements
Corrosion Testing Laboratories, Inc. and Astro Pak Corporation provided the required corrosion testing and financial support for this study, and Cotter Brothers
Corporation provided the welding and sample coupons and financial support in the development of this study. We would also like to acknowledge the following MJ
members for their work in the development of this paper and for serving as the editorial review group.
Ken Kimbrel – ASME BPE Past Chair / VNE Corporation Co-Author
Curtis Elkins – MJ member, Past Vice Chair / CSI Pharmacy
Daryl Roll – MJ contributor / AstroPak Corporation Co-Author
Randolph Cotter – MJ member, Past Chair/ Cotter Brothers
Jim Dvorscek – MJ member, Past Chair / Vessel and Weld Inspection Services, LLC
Ernie Benway – MJ contributing member / Ironwood Specialist Inc.
Jim Fritz – MJ member / JDF Metal Consulting
Cullen Weeks – MJ member / RGD Project Management, Inc.
William Daprile – MJ Member / Eli Lilly & Company