The Future of Pharma Supply Chains: Modern Value Chain Networks
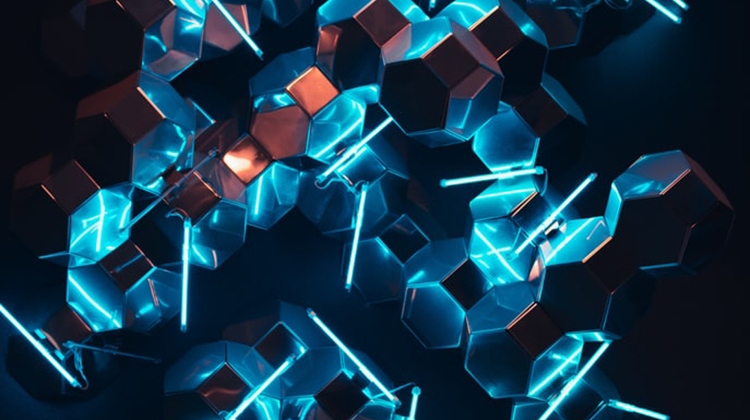
Expectations have never been higher for the pharmaceutical industry.
In 2020, the industry was under intense pressure to develop vaccines that would save lives and slow the spread of COVID-19. The industry succeeded, and the impact that high-speed vaccine manufacture has had on global health has been profound.
The last 18 months shed light on industry shortfalls, as well as opportunities. Market disruption reinforced the need to transform the supply chain for greater agility and resiliency during periods of volatility. Going forward, speed to market for high-efficacy pharmaceuticals will be a top priority for manufacturers, which means they must find a way to contend with typical supply chain roadblocks. Incidents like pandemics, natural disasters and dependence on single-sourced suppliers all threaten their ability to deliver drugs in a timely manner.
For pharma manufacturers that rise to the challenge, their supply chain will look much different than it has in the past. It won’t resemble a chain at all. Instead, modern value chain networks, built upon the Pharma 4.0™ concept coined by ISPE, will digitally connect pharma companies to the businesses they are intertwined with, from R&D to manufacturing and distribution. It will allow access to the data generated at every location.
With end-to-end data access and visibility, there is more opportunity to analyze, monitor and optimize using Industrial AI and integrated software applications. Pharma manufacturers will drive a greater impact at every stage of production. In the future, the challenges of getting better at feedback loops, measuring results with more complete data, and tying results to real-world impact will be more easily addressed. Pharma companies will measure the efficacy of therapies using richer contextual data that assesses how pharmaceuticals are distributed, ingested, and disposed of by augmenting clinical trial data with real-world outcomes and distribution data. Using COVID-19 and vaccine manufacture as an example, the optimization process for efficacy would mean having constant access to data regarding whether a vaccine meets storage temperature requirements, thus eliminating manual data recording and other obstacles.
Turning Modern Value Chain Networks into a Reality
According to a survey by AspenTech and Longitude of 300 decision makers in the pharmaceutical industry, nearly half (48%) rate their organization as either poor or ineffective at using data to predict and resolve supply shortages. The need for change is apparent but transforming their supply chain is an intimidating task for pharma manufacturers. Therefore, progress should be hyper-focused on specific outcomes and prioritized use cases, which can be done in four steps that are implemented in cycles:
- Assess digital maturity – emphasis should be put on the most significant opportunities for improvement. Start by gaining a holistic view of all data with an overarching digital reference architecture that can unify and integrate data from existing systems for complete visibility. Connecting suppliers should be considered in the context of data governance, access, and security precautions.
- Convert paper processes to digital – manual processes for things like planning, scheduling and batch records are error prone and costly. Using advanced software applications instead not only improves data aggregation and access, but also provides valuable data that can be collected, analyzed, and used to improve outcomes.
- Determine cloud strategies early – moving to the cloud doesn’t have to happen all at once. The cloud can augment on-premises solutions that often create data silos and may be getting crushed by data volume. Additionally, the cloud makes it easier to extract data for machine learning and implement advanced digital solutions in remote locations with limited IT support.
- Consider industrial AI capabilities – artificial intelligence (AI) can be integrated into workflows and empower industrial systems to operate semi-autonomously to improve patient care and maximize profit.
With these steps, which are described and supported by ISPE GAMP® Guidance Documents and ongoing GAMP® Special Interest Group activities, pharmaceutical manufacturers will begin to fully embrace process automation with closed-loop systems. Armed with knowledge, data and insights, workers at the operational level will be empowered to make recommendations and decisions that drive operational excellence. It will become much easier for pharma companies to gain a widespread view of their entire supply network, including where supply sits, which supplier has capacity, and which supplier will deliver the highest quality. In other words, potential problems can be spotted far in advance, and sidestepped as needed.
Pharmaceutical manufacturers will begin to see other benefits as well, such as faster time to market, quality assurance and outcomes-driven decision making. The data access unlocked from digital transformation allows for business continuity and optimization, including mitigating asset downtime, monitoring for critical quality and performance attributes, and improving results based on modeling outcomes against different scenarios.
Undoubtedly, pharma manufacturers have been slower to embrace digital transformation than other process industries. However, the bar is now far too high for the industry to ignore the opportunities brought forth with initiatives like modern value chain networks and ubiquitous data access. In the future, market volatility will be more of a supply chain blip, rather than a major obstacle that disarms operations and slows vaccine and drug manufacture. Digital transformation benefits will be endless for both the pharmaceutical industry and ultimately, the patients it serves.