Setting Net-Zero Targets: Tangible Benefits of Sustainability

Many organizations are on the right path to sustainability, but more can still be done— especially for setting and meeting net-zero targets. Although a commitment to net-zero operations is important for all industries, it’s particularly necessary for the pharmaceutical industry, with its high energy consumption, high water demands, and the use of solvents for manufacturing.
According to the United Nations, most scientific estimates indicate that the Earth is already about 1.1 degrees Celsius (°C) warmer than it was in the late 1800s, and emissions continue to rise. To keep global warming to no more than 1.5°C (a limit established in the Paris Agreement), emissions need to be reduced by 45% by 2030, with a goal of reaching net zero by 20501.
As a reminder, net zero is the point at which global greenhouse gases (GHGs) are balanced by real emissions reductions and carbon removal projects. It is an ambitious undertaking. When evaluating what’s being done by businesses on a global scale, there’s good and bad news. Figure 1 shows a comparison of global GHG emissions across sectors.
Net Zero Tracker, an independent group that follows corporate pledges, recently studied 2,000 of the world’s largest publicly traded companies. They determined that half of those companies already have a net-zero target. That’s a 40% increase over 18 months, from 702 in June 2022 to 1,003 in October 2023. Many of these corporations are in a “substantive transitional phase,” meaning they’ve accepted the climate issue and are working to make good on their sustainability goals3.
On the other hand, the pharmaceutical industry still has a lot of work to do regarding the scale of its emissions. A recent study of the biotech and pharma industries by My Green Lab shows that “90% of the 91 public companies analyzed in the sector still do not have targets in the short term (2021-2025) that are aligned with a 1.5 degree Centigrade increase worldwide.” Figure 2 shows the breakdown of GHG emissions for the pharmaceutical sector under scope 1, 2, and 3.
Even when an organization sets a sustainability target that does not necessarily mean its efforts are meeting expectations for that target. Last year, a research highlight in MIT Sloan Management Review determined that sustainability progress is stalled at many US companies. Less than one-third of US employees surveyed said their organizations have practices to ensure sustainability goals in business models and employee roles4.
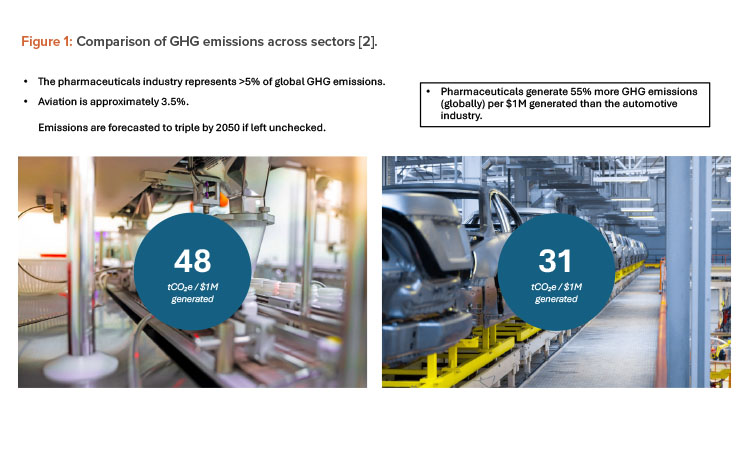
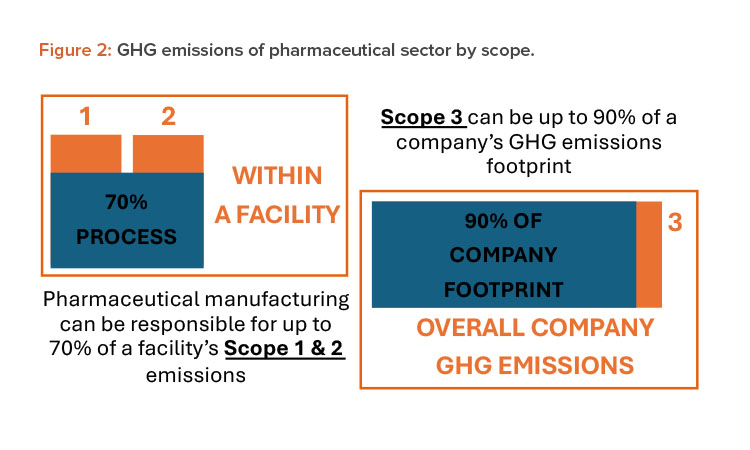
To be successful in achieving a net-zero target, according to the MIT research highlight, a company must have “embedded sustainability into their corporate DNA. This means that they have endowed their employees with a sense of sustainable ownership, spurring them to engage in more sustainability-supporting behaviors. When every employee integrates environmental and social concerns into every business decision, sustainability progress is accelerated” 4.
In many cases, that’s easier said than done because of established business best practices. Projects can start out with ambitious sustainability targets, but once capital costs are calculated, many sustainable features are stripped out because benefits to the bottom line are unclear. If the focus can shift toward the whole life cycle cost analysis of a project, the benefits become clearer, such as reduced costs and more efficient operations.
However, environmental experts are urging business to think differently5: We can and must change behaviors, processes, and equipment (and we should do it in that order). We must find ways to reduce consumption, and then find ways to replace systems and optimize existing processes. Even small incremental changes can add up when considered across the scale of a manufacturing company.
One of the most persuasive ways to change existing attitudes and behavior—and to create a culture of sustainability in manufacturing organizations—is to show that we can move toward a net-zero target while also achieving operational efficiencies. These efficiencies then translate directly to corporate savings. After that, successes in one area of operations can prompt others to make incremental changes in their own areas. Taken together, these small successes can lead to a culture that will more fully embrace sustainability and lead to achievement of net-zero targets.
In this article, we look at several case studies that have yielded not only more sustainable operations for pharmaceutical companies, but that have also contributed to a healthier bottom line. We’ll address progress being made in the pharmaceutical industry in architectural design, process design, and heating, ventilation, and air conditioning (HVAC) systems. Then we’ll examine how an organization can establish its own net-zero targets and move toward companywide integration of sustainability.
ARCHITECTURAL DESIGN
A noteworthy example of how architectural design can embrace sustainability goals is a warehouse designed for a company that manufactures and packages an immuno-suppressant product. This project comprised a 7,358-square meter, state-of-the-art warehouse, production and quality control space, including offices and plant rooms supporting an existing pharmaceutical facility.
The purpose of this warehouse structure is to store finished pharmaceutical products in a controlled environment. The goal of its design was to accommodate the future needs of this and a companion site, reducing transport emissions by 680 metric tons per year. To that end, the project was designed to conform to ISPE guidelines, the Leadership in Energy and Environmental Design (LEED) certification program, and energy-efficient design principles.
Energy-efficient design protocol highlighted the need for high-energy performance building fabric, advanced lighting technology and controls, renewable generation, application of clean technology, and energy considerations on all significant energy users. During construction, every effort was made to reduce environmental impact. A construction environmental management plan provided project-specific measures, with procedures for the scope of both permanent and temporary construction work.
Integrating sustainability into the design had both environmental and financial benefits. To maximize energy generation, the roof was designed with a para-pet edge to protect photovoltaic panels from wind uplift, which removed the requirement for additional steel. To introduce natural light deep into the building, the south and east elevations featured large-scale glazing, and the personnel and material corridors had glazed walls. With this design, more daylight reached into labs, offices, and corridors, reducing artificial lighting and subsequent cooling load (which reduced the energy use of the building) while increasing indoor environmental quality.
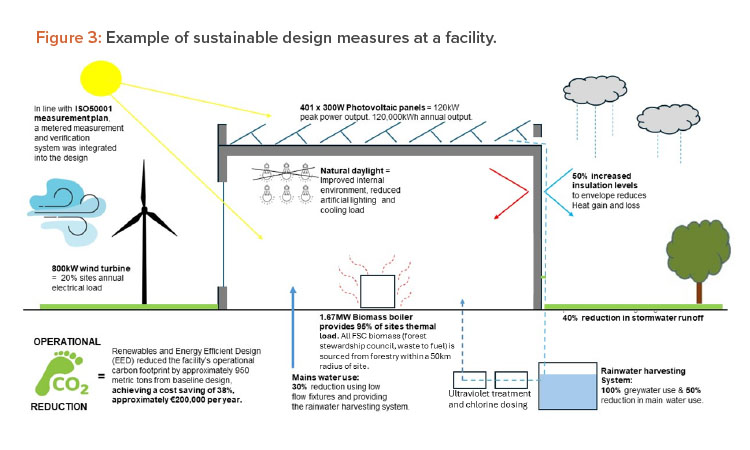
The supply chain was limited during and after the project’s construction. Approximately 33% of materials by cost were to be sourced from within 800 km of the site, including steel, glazing, and insulation panels. This supported the use of indigenous resources, involving local communities and thereby reducing the environmental impacts resulting from transportation.
Energy
A key objective for the design team was to reduce the carbon dioxide (CO2) impact of the facility. Energy-efficient design protocol and best practices were put in place. These practices highlight the need for high energy performance, advanced lighting technology and controls, renewable generation, application of clean technology, and energy considerations on all significant energy users. Figure 3 describes the measures incorporated into the design.
As a result of these efforts, although the site area increased by 50%, the overall site continued to receive 98% of power from renewables (40% from on-site generated renewables and 58% from certified renewable grid import). This effectively created a 98% reduction in CO2 emissions. The operational carbon footprint of the facility reduced by approximately 950 metric tons from the baseline design or €200,000 a year.
This project demonstrates the benefit of integrating sustainability into the design from the project’s outset. It also shows how a business can grow and expand in a sustainable manner when the building and its function, site, and geographical location are viewed as one linked system. When existing facilities are retrofitted, the approach is a little different. It is recommended to perform an audit of the building(s), utilities, and all current and planned activities where the most obvious or biggest energy users can be identified (see Figure 4).
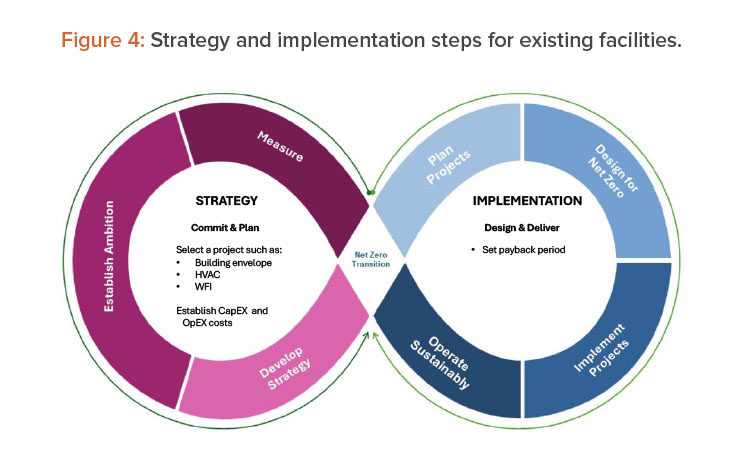
PROCESS DESIGN
Figure 5 provides a high-level summary of opportunities for sustainability in the design of processing facilities. Theoretically speaking, many of these opportunities rely on early implementation for long-term environmental benefit. However, a balance is sought between sustainable chemistry practices and expediting delivery of a medication to a patient. There are many opportunities for introducing sustainability into the design of processing facilities.
This article focuses on two aspects of the opportunities shown in Figure 5: solvent recovery as an element of waste segregation and recovery, and water for injection (WFI) as a part of process utilities. In both cases, the financial impact on an organization, and the industry in general, may be considerable.
A March 2024 report update from the analyst firm Markets and Markets shows that the worldwide market for solvent recovery and recycling was valued at $1.085 billion in 20236. This market is projected to reach $1.38 billion in 2028, growing at 5% compound annual growth rate (CAGR) from 2023 to 2028. The pharmaceutical industry is one of the chief markets for solvent recovery; others include the chemical, automotive, printing, and paint and coating industries6.
According to a December 2023 report from Coherent Market Insights, the overall pharmaceutical water market “is expected to reach $10.66 billion by 2030, from $6.2 billion in 2023, growing at a CAGR of 7.9% during the forecast period”7.
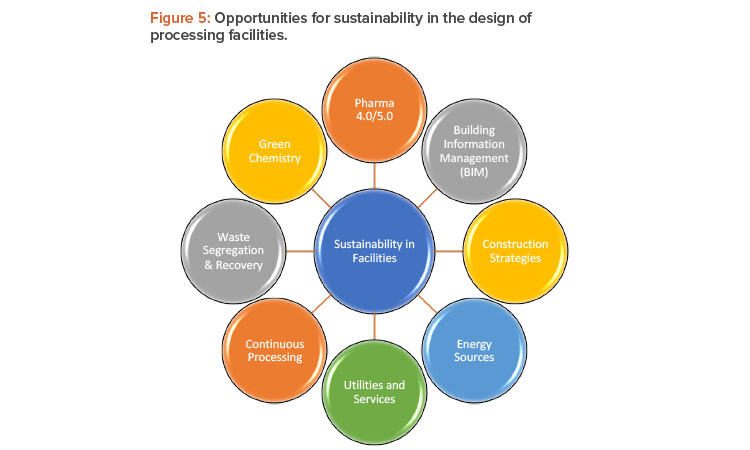
Solvent Recovery
Solvent recovery can be expensive and greatly impacts the environment when processing waste material without using sustainable design and methods. Typically, waste solvents are treated as hazardous waste and sent to an off-site waste handling company. Off-site, the solvents face three fates: be separated; be chemically broken down to smaller, less harmful components; or, more frequently, be incinerated.
One sustainable solution to handling organic wastes incorporates “downcycling.” This involves recovering solvents from a waste stream and reusing them in the facility for an alternative (typically less critical) use. Alternatively, if the recovered solvent meets a particular market need, it may be sold off as a byproduct. In this case, the pursuit of sustainability can result in a company being able to generate income through the sale of the organic solvent resulting from the solvent recovery system. Additionally, any water recovered from solvent recovery can supply the facility’s gray water requirements.
To understand how solvent recovery was addressed in process design, consider the case of a major diagnostics testing supplier. The company had an aqueous-organic blended hazardous waste stream, comprising 65% water and 35% organics with toluene and methanol as primary organic components. This hazardous waste stream was shipped off-site and then incinerated to recover the energy from the organics. As a sustainable design solution, the manufacturer recovered a part of the waste stream and sent it to a recovery process.
The waste solvent flow rate here was approximately 10 gallons per minute, and distillation was used to recover the solvent. The blended waste stream was heated from ambient conditions to distillation operation temperature by heating it with a hot glycol system. By incorporating preheaters into the design, less hot glycol was used in the process, which reduced the amount of energy required for heating and cooling.
The distillation process for this facility resulted in a recovery rate of 95% for organic solvents and more than 99% for water. The organic solvents were sold to a cleaning chemicals supplier, and the recovered water was used to support water usage in the office building. Hence the solvent and water, once spent from the process operations, were both downcycled and used for subsequent applications.
This system has been in operation for two years. The return on investment is anticipated to be reached in four years, which considers the value of the recovered solvents and reduced water demand. The key elements in the process design were waste collection and segregation, as well as how the products were to be distributed. For some sustainability-focused initiatives, longer payback periods (even upward of eight years) are frequently acceptable based on positive environmental impact and the scale of the investment being made.
WFI
Because water is one of the most expensive utilities for pharmaceutical facilities, any improvement in an organization’s WFI process efficiency can have significant financial and operational benefit. Improved energy efficiency in WFI systems reduces the direct utility requirements of the systems and the size of supporting utility equipment, such as boilers and chillers. This reduces the overall energy consumption footprint required and simplifies operations.
Another diagnostics supplier wanted to approach its WFI generation more sustainably. Their existing system used a multiple effect still (MES) system, generating two gallons per minute. The current volume of WFI generation produced using this system has been at capacity for nearly 16 years. The facility, now undergoing an expansion, required generating four gallons per minute. This is why they undertook a design process in which every sustainable option was to be evaluated to address efficiency while also reducing energy consumption.
MES is among the most energy-intensive ways to make WFI. Potable water is fed into the system and must be boiled using low-pressure steam. The system in this particular facility used both a hot loop (operating at 80°C) and an ambient loop (operating at 20°C) that is cooled by a chiller.
A number of options were explored to meet the organization’s goals of doubling the WFI output capacity while reducing energy consumption. One option considered was a membrane-based reverse osmosis system, which typically requires less energy than an MES system. Ozonation for sanitization also reduces the energy consumption, as compared to a conventional heat-based sanitization approach. Because generation rates were to be doubled, other parameters such as line sizing were also evaluated. Further, the facility’s chilled water supply and return temperatures were found to be working at nonoptimal operating points.
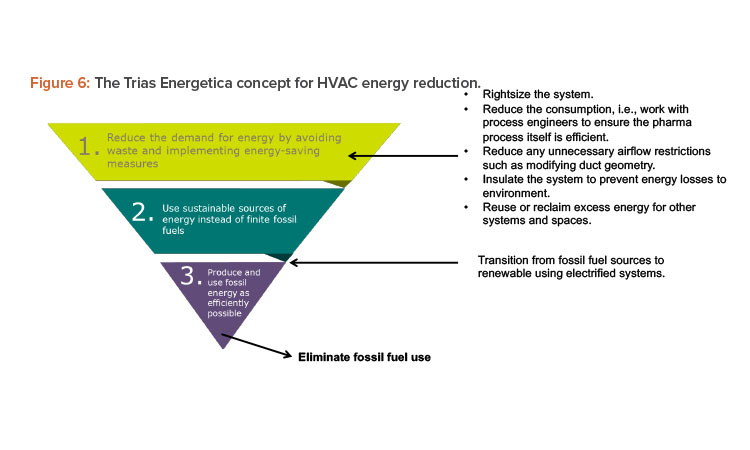
Another consideration was that membrane-based WFI generation systems produce ambient WFI. A new design concept introduced point-of-use electric heaters to heat only the limited users of hot WFI. This, in turn, would allow the entire hot loop to be eliminated, with all users fed off the ambient WFI loop. The return on investment in this larger WFI system was projected to fall within two to six years, depending on how many of the suggested options were implemented.
From a process facility design perspective, the best approach to sustainability is to start small. Evaluate what can be done to make existing systems more sustainable. Starting small and realizing the benefits through practical use of the system helps set up a culture of sustainability that will lead to easier implementation of more sophisticated or involved design changes down the road.
Once that culture and entrepreneurial spirit is established, people in the organization will suggest other ways to address sustainability and reduce energy consumption. At a Parenteral Drug Administration Annual Conference in March 2024, one of the speakers noted that their organization was operating freezers at -70°C (as compared to -80°C). Changing the operating temperature to a higher but still acceptable level reduced their freezer energy consumption by 20%.
Although this example merits further detailed investigation from a risk and quality perspective, and the organization is continuing long-term studies to ensure there are no adverse effects on samples, it shows that small changes in thinking can yield substantial benefits and enhance a sustainability mindset internally. These small changes might also yield a faster return on investment than broader process designs with more ambitious goals. There’s no idea that is too small in a sustainable culture.
HVAC AND MECHANICAL SYSTEMS
HVAC systems, both wet and dry, can account for approximately 70% of energy use in a pharmaceutical facility. Moving toward net-zero design for HVAC could be summarized as shown in Figure 6. When it comes to HVAC and mechanical systems, chilled water and hot water systems are the energy backbone of the building and are related through heat pumps. In pharmaceutical applications, subcooling is typically used to remove moisture and dehumidify air during the summer, which is then reheated to maintain space temperatures. This is due to the high air changes required in the production process.
Although sustainable principles first call for reduced consumption, this can be challenging depending on the type of pharmaceutical process. An example of reducing consumption is to use a closed, rather than an open, processing unit. The overall cleanroom grade can be reduced, which reduces the size of the HVAC and its subsequent energy use. Where this is not possible, the next approach is to consider ways to improve the efficiency of the system and reuse materials and energy.
Reuse
Reuse was done particularly well on a greenfield project for a pharmaceutical company specializing in ribonucleic acid therapies. This company uses a considerable amount of flammable material, with a high demand for outside air. Twenty-five air changes per hour of outside air in the production space were required to maintain the spaces below 25% of the lower explosion limit. This organization’s goals were met by installing an intelligent runaround loop, with a process chilled water system on its own dedicated heat pump system, to generate hot water for the HVAC system.
Most facilities that require energy to be recovered from exhaust air make use of a standard runaround loop, comprised of a coil in the exhaust system, a coil in the supply system, and a pump running either water or water with glycol between the two. At peak conditions, that type of system produces about 10% energy recovery.
By contrast, an intelligent runaround loop uses temperature monitoring on both sides of the system and integrates multiple air handling units and exhaust streams into a single system (provided they’re operating at generally the same temperature). The pump flow will vary, with control valves allowing the system to adjust the flow rate to each coil.
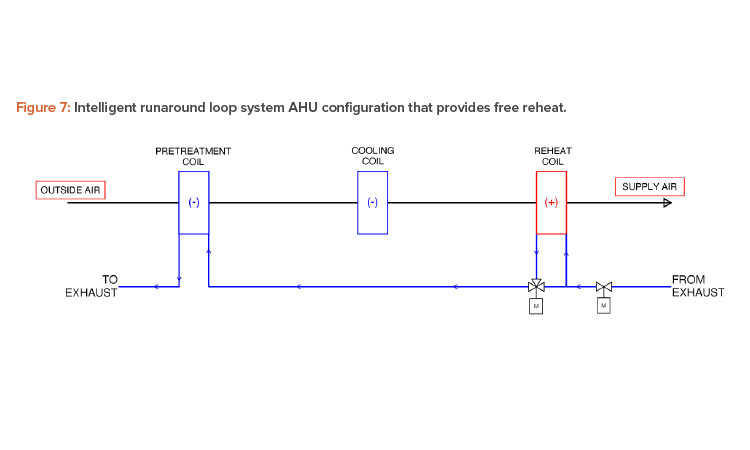
This facility required six large air handlers—approximately 170,000 cubic feet per minute, divided among the handlers, all connected via the intelligent runaround loop system. The system achieves over 25% energy recovery during peak cooling conditions and over 30% heat recovery at peak heating conditions. The system can also provide about 90 refrigeration tons of cooling to electrical and information technology (IT) rooms during the winter and redistribute that heat to other rooms. The free cooling system allows for the shutdown of the cooling towers during the winter.
When designing more sustainable HVAC systems, it’s important to look for any simultaneous loads that will enable systems to transfer energy. In this case, the facility transferred energy between the process chilled water system and building heating hot water systems using heat pumps.
During the summer, water comes from exhaust air in the system and provides the primary source of reheat via the reheat coil in the air handling units (AHU), which allows the system to recover additional cooling capacity. The energy recovery fluid is then run through the pretreatment coil. This configuration provides free reheat and maximizes the amount of cooling recovered (see Figure 7).
Heat recovery from the exhaust air can also be improved by using an intelligent runaround loop system during the winter. The system design is capable of over 35% energy recovery from exhaust air during peak heating demand. In practical use, however, the result was closer to 30% because the spaces are humidified to 30% relative humidity. This limits the heat recovery because of frosting on the heat recovery coils in the exhaust air. Consequently, although greater recovery is theoretically possible, strict humidity requirements in processing limit the energy that may be recovered. High humidity may lead to icing on the coils.
With its intelligent runaround loop system, the company was able to realize nearly 30% energy recovery, as opposed to the 10% that is typical of a standard runaround loop. The intelligent runaround loop system paid for itself in approximately four years with the associated energy savings. Chilled and hot water systems typically have an operational lifespan of about 25 years, which results in significant net savings over the life of the system.
There are specific sustainability challenges to HVAC design for pharmaceutical and hazardous exhaust facilities. Organizations need to make certain they are not cross-contaminating their supply with exhaust. In the runaround loop case detailed here, the supply and exhaust are separated. In other cases, a company must know how tolerant the facility is to cross-contamination as a risk associated with energy recovery that may allow the use of other energy recovery technologies.
The development of energy-efficient systems to reuse the energy available is the first step in achieving net-zero HVAC systems. The concepts presented here are the first steps in the electrification of HVAC systems to achieve net zero.
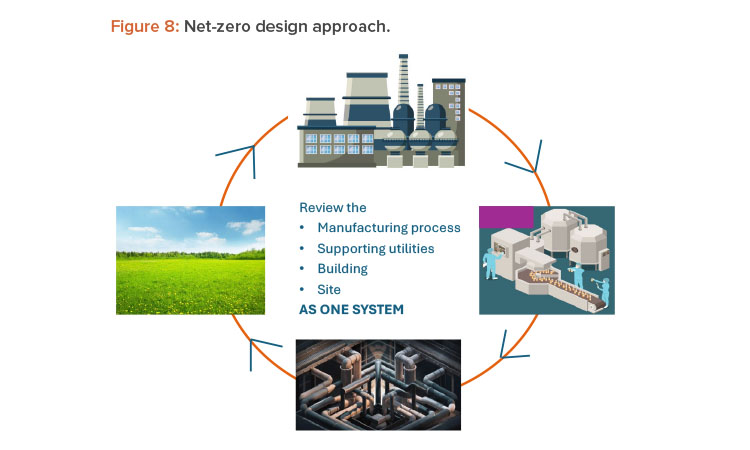
THE NET-ZERO LIFE CYCLE
As seen in the preceding examples, sustainability in operations should not only be considered “nice to have.” In practical and measurable ways, sustainability can create improvements that lower operational costs or even allow some processes to essentially pay for themselves. Reviewing the facility as one linked system (as shown in Figure 8) from the project outset, be it a new facility or retrofit, creates the opportunity to make the most impactful and cost-efficient solutions. One decision will impact another.
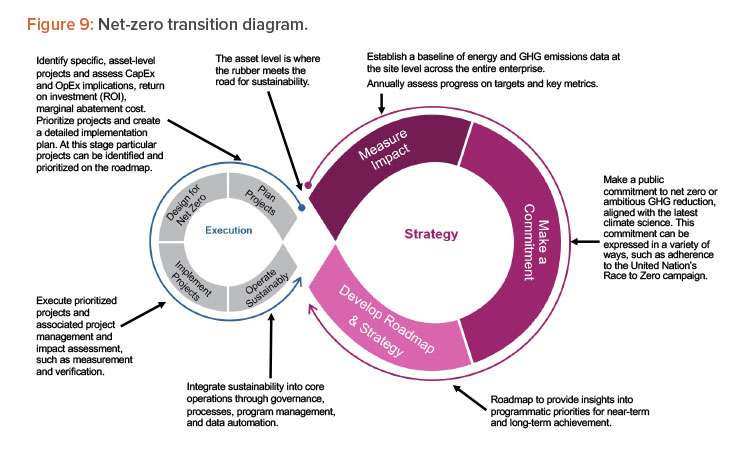
At the same time, forward-looking organizations are even implementing sustainability initiatives that have no return on investment—that is, they are implementing sustainable design elements because they are good for the environment while recognizing that they are expensive to implement. Capital expenditures (CapEx) can increase while operating expenditures (OpEx) decrease.
The net-zero life cycle is a journey undertaken by an organization to embrace improvements to its operations to slow the effects of climate change. It includes both enterprise- and asset-level considerations. Starting at the company level and moving to each site allows organizations to prioritize the most appropriate projects on the roadmap. This process is summarized in Figure 9.
CONCLUSION
Designing future assets with net zero and company commitments in mind should consider circularity, designing out waste, remediation, and land use changes. Planning for net zero can be a challenging undertaking. But as the saying goes, the longest journey begins with a single step. Grants and private and state funding are available globally for decarbonization projects that can support a company’s net-zero journey. Small changes, even at an individual level, can contribute to an organizational culture that understands the value of sustainability in dollars and cents and that provides a vital and lasting legacy to future generations.