Case Study: Meeting Manufacturing Needs with a Net Zero Energy Facility

The expected FDA approval for a Treprostinil dry powder inhaler revealed a need for the manufacturer to expand its warehousing and logistics capabilities to support its growing operations. The company’s senior leadership wanted to ensure this expansion came with as minimal an impact on the environment as possible, so a key priority was to provide a net zero energy facility. With a vision for what the project could be, the team named the upcoming endeavor Project Lightyear. To infinity and beyond, indeed.
In anticipation of the expected FDA approval of our new inhalation device for inhaled Treprostinil—and the only dry powder inhaler approved by the FDA for use in pulmonary arterial hypertension and pulmonary hypertension associated with interstitial lung disease—we identified the urgent need to expand warehousing and logistics capabilities to support growing operations. This new warehouse and logistics center would provide the much-needed space for continued growth and be vitally important in delivering critical resiliency for facility and logistical operations.
It was important to senior leadership that this expansion of treatment options and further fortification of the supply chain came with as minimal an impact on the environment as possible. Given the project’s critical nature, it was clear that its success hinged on developing a clear roadmap of project requirements from the onset of conceptual design. The company’s CEO laid out that roadmap succinctly during an early project meeting with the corporate real estate, operations, and manufacturing leadership teams.
The primary priority was to provide a site net zero energy facility to support the manufacture, storage, and distribution of the Treprostinil dry powder inhaler and to do so without the use of fossil fuels onsite. This meant no natural gas, diesel, or propane generators for a critical cGMP facility containing an extensive cold room. From there, the cascading priorities laid out the ultimate project framework.
Identifying an experienced architect, engineer, general contractor, and commissioning agent that could work together in a collaborative design-build environment was critical to the success of such a technical and cutting-edge project.
The facility would need to be designed, constructed, commissioned, and validated for occupancy and use by the summer of 2023, when projected growth would test the capacity of existing facilities. It was to be built and assembled using materials made in the United States to the greatest extent possible, without affecting the net zero mission or schedule requirements. This was pursued with the understanding that the first three priorities held precedence and knowledge that this was the kind of executive-led freedom that would allow the project to be a success. From there, the team was pushed to reduce embodied carbon within the construction of the building, limit ecological impacts within the project’s footprint, and pursue LEED and other sustainable certifications.
Assembling the Team
Identifying an experienced architect, engineer, general contractor, and commissioning agent that could work together in a collaborative design-build environment was critical to the success of such a technical and cutting-edge project. Ultimately, the general contractor was selected based on their extensive experience in developing sustainable projects and history of successfully delivering unique and highly technical projects.
In seeking out a partner architecture and engineering firm, the project benefited from local expertise. An exceptional architecture firm was selected that focused on developing first-in-class facilities for their clients while using creative solutions. A national, industry-leading professional engineering services firm was selected that specialized in consulting, planning, designing, and commissioning dynamic systems for the built environment.
With offices in the Raleigh-Durham, North Carolina, area and around the country, the architecture and engineering firms brought a wide purview on sustainability and extensive portfolios of experience in the life science and biopharmaceutical industry. Their depth of expertise in sustainability and technically complex projects—many of which were the first of their kind and required innovative thinking and persistence—resonated with our team given the task at hand.
Commissioning was procured at the concept design phase to round out a strong team with an integrated design approach. This helped maximize the benefits of having the third-party commissioning provider (CxP) in applying lessons learned from past projects. It also helped ensure that the owner’s project requirements were upheld from the beginning for this complex and unique facility. The chosen CxP focused on finding solutions and resolving issues instead of only documenting problems, which proved beneficial in turning over fully functional and highly integrated facilities for critically complicated projects already within the company’s portfolio.
Other key stakeholders that played a vital role in the project included the Durham city and county building inspection departments, the Research Triangle Foundation, Duke Energy, FM Global, and numerous departments and teams from within the corporate umbrella itself. All groups brought a unique perspective and bought in on a collaborative environment to ensure that all parties not only achieved positive outcomes, but also gained knowledge and solutions that can be applied to future projects. Together, the assembled team was ready to undertake this ambitious and groundbreaking project.
Blocking and Tackling
To minimize the project’s ecological impact, the selected location was an existing underutilized company-owned soccer field and associated field house on our Research Triangle Park campus in Raleigh, North Carolina. The soccer field was adjacent to our new site net zero childcare center. This location provided direct access to TW Alexander, enabled the team to avoid clear-cutting the remaining wooded area on campus, and provided for the adaptive reuse of the existing field house. This adaptive reuse significantly reduced the embodied carbon of the project while creating substantial cost savings due to the overall reduction in newly constructed square footage.
The first step of the building design process was to work with the operations team to determine facility scale, shipping and receiving rates and requirements, and pallet rack position counts required in both ambient and cold room storage. These project requirements were pulled together with the purpose of right-sizing the building to meet capacity needs while optimizing operational efficiencies. The building’s shape and scale was critical to informing the overall design because it impacts everything from rack layout to air circulation to the rooftop area available for solar power generation. Ultimately, it was all guided through close coordination with the commercial operations team to anticipate future sales volume and associated storage requirements.
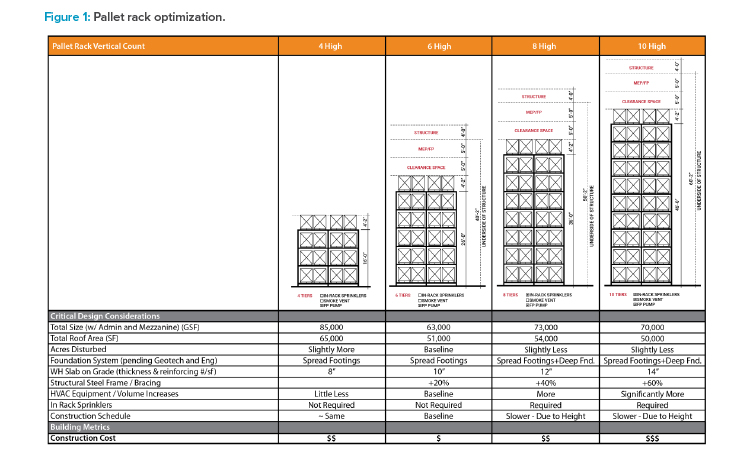
Through these discussions, the team determined that the facility would need to accommodate +/- 2,400 pallet positions within ambient storage and +/- 600 pallet positions within cold room storage. From that base requirement, the building’s shape and footprint was directly informed by a detailed pallet rack height optimization exercise. As illustrated in Figure 1, the design-build team analyzed rack heights ranging from 4 racks high to 10 racks high. The team then analyzed the subsequent impacts on cost, schedule, constructability, technical performance, facility operations, code requirements, and campus integration.
Notably, the differences in building form factor created a delta upward of 15,000 sq. ft. of built area and seven figures of cost implications. These ranges had to be balanced with the needs for a functional net zero energy facility. Ultimately, a six-rack-high ambient storage ratio was determined to provide optimized functionality for the project and would lock in the basis of design. From there, blocking plans ultimately led to a 7,000-sq.-ft. cold room, 27,500 sq. ft. of ambient storage, and facility support spaces that brought the total building to 52,500 sq. ft.
Net Zero Design
Within the sustainable design community there is much discussion and debate over the practical definition of terms like net zero energy and net zero carbon. For clarity of purpose, our project team defined site net zero energy as a “grid-connected facility for which every watt of energy needed to operate and run the facility over a twelve-month period would be covered by onsite renewable generation.” This framing does not allow for offsite production or carbon credits to close the gap. It does allow for the facility to export to the local utility grid or “bank” energy when the facility is operating in a net positive condition (generating more energy than it uses) and to subsequently pull from the local utility grid or “withdraw” the complement of that energy during periods of time when the project is using more electricity than it is generating.
For the design process, it is standard practice to establish an anticipated target goal energy usage intensity (EUI) for the facility. EUI is simply a ratio of energy used by a building divided by its area and provides an important benchmark of energy usage versus its peers. It is generally established through the utilization of baseline expectations from completed and operational projects. From there, the design team’s job is to reduce the EUI to the greatest extent possible and provide for the most feasible energy-efficient facility.
Although this is a rather standard starting point for a typical project, there are not published baseline expected EUIs for hybrid ambient/cold room cGMP warehouses and certainly not for similar facilities pursuing such ambitious and innovative sustainable design goals. This is due in large part to the critical nature of these facilities and an overarching design concept provides comprehensive support of belts and suspenders to ensure the building’s operation conforms with cGMP requirements. Essentially, energy usage is typically considered secondary to building operations.
Once again, Project Lightyear would be blazing its own path forward, as even attempting to establish a baseline from scratch was often met with blank stares and shrugs from many critical trade partners. However, after discussing the project’s goals, those same vendors were excited to get on board and learn with the team. One such example is that energy usage requests to the cold room vendor were answered with “I don’t know” and a litany of follow-up questions digging into the minute details: details such as how often the overhead door into the clean room would be opened in a typical day and how long it would remain open. Such details were vitally important in establishing a meaningful baseline EUI and in turn helping develop a design expected to produce the desired net zero energy goals (Figure 2).
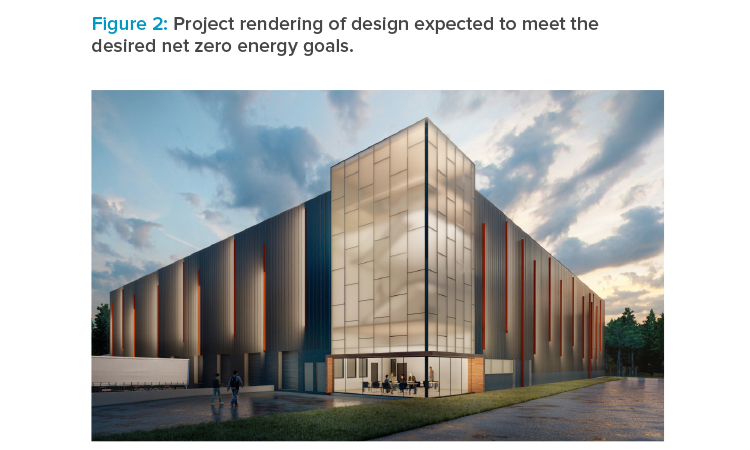
Passive Design Strategies
Once a baseline EUI was fully developed and understood, the design team took their initial step of designing to net zero energy. This first step is typically done by reducing the building’s energy demand by implementing passive design strategies. Something as simple as the facility’s siting, or cardinal orientation, at a chosen location can be very impactful on its ultimate energy usage and photovoltaic (PV) energy production.
An analysis of the site can help ensure that its chosen orientation provides for optimal PV energy production. This is typically done through solar analysis modeling, which models and tracks the sun’s course through the sky at different points in the year. Analyzing that data enables the design team to lay out the site and orient the building to ensure that the planned rooftop PV panels are aligned for peak production values. Beyond that, the project goal of reducing ecological impact was achieved by locating the building to minimize impact to adjacent wetlands, existing tree canopy, and other natural habitats. As noted previously, using the existing soccer field was beneficial in pursuing this goal.
Project Lightyear now had a location and skeleton framework. As was a reoccurring theme, planning for the skin of the building—the façade and roof—would require optimizing often competing priorities. Ensuring the proper level of insulation while providing a cost-effective solution and always with an eye to embodied carbon would prove to be a difficult balancing act. Increasing the insulation values of the roof, walls, and windows was critically important to reducing the facility’s energy usage. Building insulation is directly responsible for reducing the facility’s heat gain or loss during the various seasons but also comes with significant increases to cost and the facility’s embodied carbon. And at a certain point, the amount of insulation hits a level of diminishing returns.
The design team worked hard to balance these issues and right-size the facility’s insulation requirements. Ultimately, the roof was insulated to R-42, the façade walls to R-21, and the windows with a U-value of 0.35. These requirements would directly impact and ultimately reduce the sizing of major HVAC equipment and drive down the facility’s energy usage by greatly reducing wasted energy.
Further reduction of wasted energy was accomplished through operational design direction. Light occupancy sensors were included to maintain minimum code-mandated lighting levels in unoccupied areas. This allows for lighting to automatically dim and even turn off when not in use. Temperature setbacks and demand control ventilation in administrative spaces ensured that operational noncritical areas were not working hard to heat and cool overnight, over weekends, and generally when not in use.
Energy-Star-certified computer and office equipment would help reduce plug loads and eliminate vampire drain of electronics when not in use. Regenerative charging electric lift trucks would capture the kinetic energy of lift trucks in motion when slowing or stopping to recharge the electric batteries, reducing the energy pull and timing when they are plugged in to recharge. By themselves, these passive design strategies would combine to reduce the expected building EUI by more than 8%—amounting to significant energy savings over the life of the project and would be critical to getting closer to the site net zero project goal.
Active Design Strategies
From there, the designers needed to provide for the optimized implementation of efficient systems and equipment through active design strategies. These design choices typically focus on the major energy draws within a building with a specific focus on HVAC systems, which contribute the most significant driver of building energy use in a cGMP facility.
To provide the most energy-efficient HVAC system for this project, the design team used a closed-loop geothermal exchange system as the basis of design. Geothermal HVAC systems work by using the Earth’s temperature as a thermal battery. Fluid is pumped through a series of pipes deep into the Earth and heat is either absorbed or rejected based on current air temperature. Acting as an extremely high-efficiency heat pump, the geothermal HVAC system achieves its efficiency by using the steady-state temperature of the Earth rather than the highly variable outside air temperature to condition the building.
The specific design of a given geothermal HVAC system is dependent on the building requirements and the local subsurface geophysical properties. The building requirements help establish the annual heating and cooling loads as well as the peak heating and cooling loads. The local geophysical properties define how attuned the ground is to accept a geothermal system in a given location, which informs the design depth and number of vertical geothermal bores required.
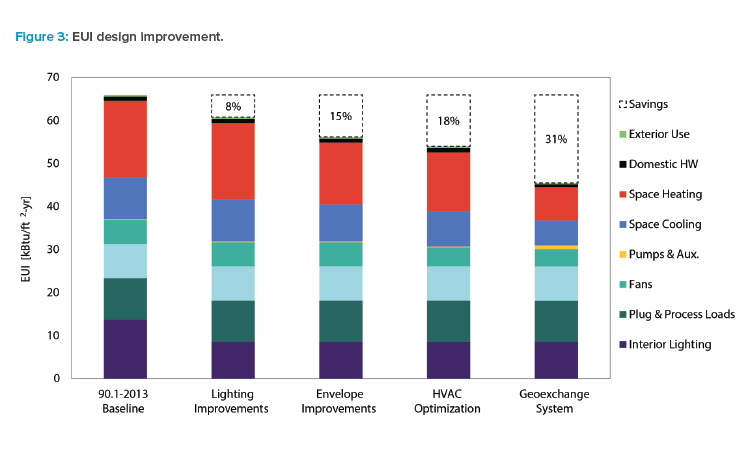
Ideally, the annual and peak heating and cooling loads would be well balanced, providing for an equally well-balanced geothermal system. Being too unbalanced in either direction can lead to long-term losses of efficiency in the system. Project Lightyear’s design loads led to an annual heating load nearly 10% over cooling and a peak cooling load more than double the peak heating load. This added significant complexity to the system to ensure that the bore field and system was properly sized.
To account for those requirements, the geothermal system was sized with 40 individual bores—each 500 feet deep into the Earth—on a total of three independent loops. This system is coupled with six pipe heat recovery chillers and a 20-ton fluid cooler to balance the loads and optimize the efficiency of the design. A dedicated outdoor air system is used to provide dedicated ventilation to the space and meet the cGMP requirements of the ambient storage area. Recirculating air rotation units then use that ventilation to ensure a consistent steady-state temperature profile throughout the entirety of the ambient storage space.
The cold room itself has dedicated air-cooled direct expansion (DX) condensing units and a desiccant makeup air handler unit sized to the specific expectations on temperature and humidity needs as well as anticipated operational use profiles. The connected field house is optimized through the use of a dedicated air-source variable refrigerant flow (VRF) system.
The design team further utilized LED lighting, variable speed fans and pumps, premium efficiency motors, and high-efficiency cold storage equipment to fully reduce the expected EUI for the building by 31%. This progressive improvement is illustrated in Figure 3.
Renewable Energy Generation
These sustainable design elements are a feat in and of themselves for a project of this caliber, but they alone do not make for a net zero energy facility. The final element entails a renewable clean energy supply. The team accomplished this by introducing an extensive rooftop PV array. The design of solar PV systems requires careful consideration of the remaining EUI to offset, building massing and orientation, expected PV panel degradation, solar yield variability, future capacity needs, and panel, inverter, and racking system availability.
A probabilistic approach to this design is typically used in concert with the previously mentioned modeling to project theoretical system output over time. In this case, an industry-leading tool called Helioscope was used to assess performance over time. Designing simply to be net zero on day one does not account for the yearly solar variability and annual panel degradation. To ignore these considerations would be shortsighted and likely lead to a facility incapable of reaching its goals.
Conversely, designing for worst-case scenarios and an unlimited timeframe would not be economically nor operationally viable. Nor would it take into consideration local utility requirements for on grid-connected PV system sizing. Rather the array must be sized appropriately with the EUI offset needs and a conservative but realistic eye to the future production.
Based on our experience on previous projects, we have traditionally adopted a PV system sizing baseline of P50 at 10 years. This means simply that we can expect the facility to be operationally site net zero at 50% confidence on solar variability for any given year, even with panel output degradation, recognizing that there are annual variations on the amount of sun the site will receive based on weather conditions.
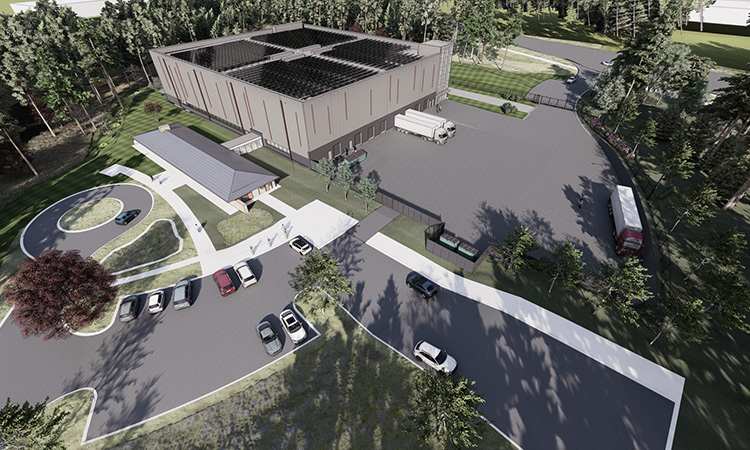
To help work through the complicated design process, the project team brought a third-party PV integrator onboard. They were able to review the basis of design information and verify through their usage of PVSyst Modeling Software and the National Renewable Energy Laboratory’s (NREL) regional solar yield dataset. Combined with the project design, the third-party integrator ultimately designed the system to include seven 62 kW Sunny Tripower inverters powered by 1,186 SunPower Maxeon 475-watt panels expected to generate 767 MWh per year. This array will cover nearly the entirety of the facility’s roof, making use of every available square foot and providing critical renewable energy generation to make the facility site net zero.
Once operational, it will be important for the project team to validate the design EUI with operational monitoring and metering. To exceed the design EUI would mean the entire project would be at risk of not achieving its site net zero goals. To this end, the design-build team intentionally scaled and sized the PV system to allow for future expansion capabilities (see Figure 4). The invertors as designed have spare capacity to allow for future installation of an added ground mounted array without impacting building operations. While the plan is that the project will exceed expectations, having the ability to correct course ensures that the project will ultimately meet its stated goals.
Resiliency and the Microgrid
Although the design to this point is expected to meet the requirements that the project be site net zero energy, it would be negligent to leave a cGMP facility of this scale and magnitude without ensuring its critical resiliency. The project priority of eliminating the ability to implement traditional emergency backup systems like diesel or natural gas generators pushed the team to explore lithium-ion battery backup systems. Unlike a traditional generator, which has a theoretical endless supply of backup power, batteries are a finite resource and must be sized specifically for the application. They can be connected to the solar PV systems through a microgrid to be able to recharge when the array is producing a surplus of energy but that is not guaranteed.
A cGMP warehouse and logistics facility like Project Lightyear cannot rely on the expectation that the sun will shine bright to power the PVs and recharge the battery during an extended electrical outage. Consequently, the design-build team worked with operations to determine the worst-case scenario emergency battery backup requirements. Essentially it boiled down to how long the operations team would need to react and reallocate resources if the power went out and the batteries were not able to be recharged from their full charge state.
Simultaneously, the design-build team reached out to the local permitting officials and fire marshal to introduce them to the concept and understand local compliance requirements. Together it was determined that a priority list would be established. The entire building needed to be able to run for 24 hours post outage. From there, loads would be shed for the ambient warehouse, support, and office spaces, allowing only the cold room to remain online for an additional 24 hours. Finally, the team was required to hold an eight-hour tranche of battery power to provide support for the fire pump that feeds the facility, ensuring that in any situation the fire sprinkler system would remain active and operational. Taken together, the loads resulted in a minimum required battery size of 5,310 kWH with 1 MW of peak demand and the ability to operate in “island mode” without utility power.
As had become routine, the team discovered in their research of various battery applications that there was a dearth of potentially applicable systems. The residential-scale market had begun to boom as more homeowners were installing solar panels on their roofs and were looking for energy resiliency in markets that encountered regular outages. But residential scale of installation was well below the requirements of Project Lightyear—typically on an order of magnitude of 100 times smaller than required. Similarly, utility scale installations were growing rapidly.
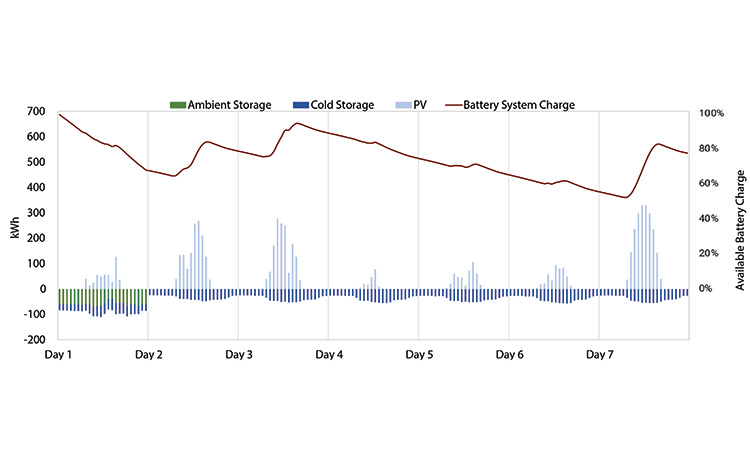
It would be negligent to leave a cGMP facility of this scale and magnitude without ensuring its critical resiliency.
This was particularly so in areas with significant time-of-use penalties or peak-usage charges where utility rate arbitrage is profitable, though these often don’t have microgrid capabilities to allow islanding from the grid during an outage. It has also started to become more common as utilities themselves develop significant solar production capabilities and have the need for on-grid storage during times of low or no solar production. The scale of these systems is typically 10 times or larger than Project Lightyear required.
Ultimately, the Project Lightyear team partnered with Tesla to utilize their Megapacks. Each individual Megapack is a self-enclosed modular battery pack that allows for flexibility and resilience and provides 3.1 MWH and 770 kW of capacity. Pairing two provided the required emergency backup for Project Lightyear. The Megapack system was attractive to the project team due to its next-gen lithium iron phosphate chemistry, which greatly reduces the potential for thermal runaway which then reduces potential risk for the project. It comes integrated with an internal cooling system, module inverters connected to an internal 480V AC bus, and independent operation that allows either to support the building load individually. Being a self-enclosed unit, the team was able to locate the system on the exterior of the building, which provided critical code/UL separation requirements and eliminated the need for supplemental fire alarm and sprinkler systems.
The Tesla Megapack is designed to be connected and controlled through a Schneider microgrid control system, allowing it to power the building and recharge when needed. The microgrid switchboard is connected directly to the battery system, rooftop PV inverters, emergency lighting inverter, and building electrical distribution system. Through a detailed building automation system, it is set up to automatically control the potential electrical distribution throughout the facility depending on required use case and battery charge level. As noted previously, it is programmed to shed noncritical loads on demand and as needed to maintain the more critical facilities.
Although the facility was designed for a worst-case scenario of no solar recharge, the design team anticipated that under normal conditions with the fully operational microgrid that the entire facility should stay online for weeks if not months while disconnected from the electrical grid or during an extended outage. Once such example of typical solar production following an extended power outage is shown in Figure 5, with varying amounts of solar production allowing the battery system to recharge fully or partially during the daytime. We are hopeful that such a use case is never fully realized and tested but are confident in the ultimate resiliency of this critical facility.
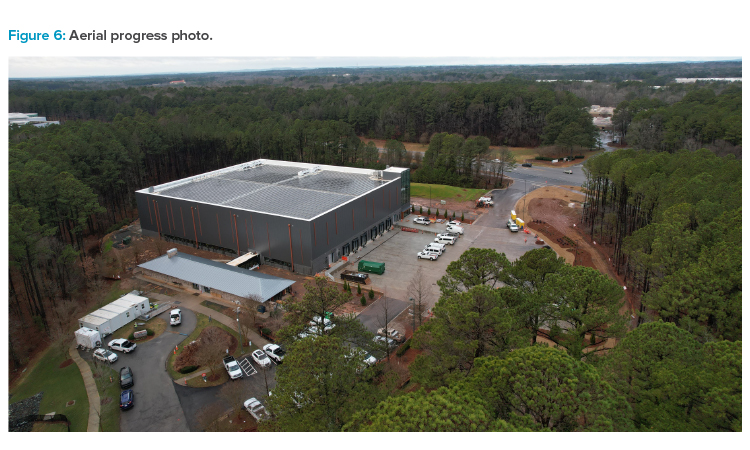
Going Live
Following design and permitting, project construction began October 2021 and is now nearing completion in spring 2023 (see Figure 6). The long path to this point was marked by many challenges, but through close coordination between all project partners, Project Lightyear is expected to be delivered on time, on budget, and fully site net zero. The project team even reached out to our adjacent site net zero energy childcare center to involve the young children in the project in exciting ways. From “touch a truck” days during the heavy civil construction phase to inviting the kids to leave their literal handprints on the final installed crossbeam during the topping out ceremony, this project truly proved to be a learning experience for all.
As on any such groundbreaking project, the lessons learned to take forward are numerous. The most significant lessons learned were based around the microgrid implementation, notably ensuring to design for flexibility in design and having a full understanding of processes during a load shedding scenario.
It is easy to say that only the cold room should be operational if the battery charge drops to a certain level but understanding the operational needs of the cold room widens that boundary. Shipping and receiving must remain operational. Building automation and monitoring systems must remain operational per FDA requirements. Printers and computers need to remain powered on. You cannot just draw a circle around a functional object without understanding the full associated process and cascading affects.
Similarly, we also discovered that the battery backup system did not work as an uninterruptable power source as originally expected but rather responded similarly to a traditional generator. This meant that building systems that needed to remain permanently online required an additional whole-building uninterrupted power supply to cover the few seconds between a power outage and the Megapacks coming online. The late discovery of this issue led to some last-minute design and construction changes that were critical in making sure that the project would be successful.
Working through bleeding-edge sustainable design and integration—most notably with the battery storage and microgrid—would not have been possible without a design team with a clear vision and a local jurisdiction and utility willing to learn along with the project team. Similarly, lingering pandemic-era cost inflation and supply chain issues were mitigated through early subcontractor involvement, critical equipment early release packages, and a design team willing to explore creative and sometimes custom-built solutions when all else failed. Ultimately, the projected is expected to received LEED Gold, LEED Zero Energy, and LEED Zero Carbon certifications.
Our team is eagerly awaiting completing the commissioning and validation of Project Lightyear in the coming months and taking final occupancy of the building to begin using this groundbreaking facility. To infinity and beyond!