Futureproofing US Pharma Manufacturing Jobs
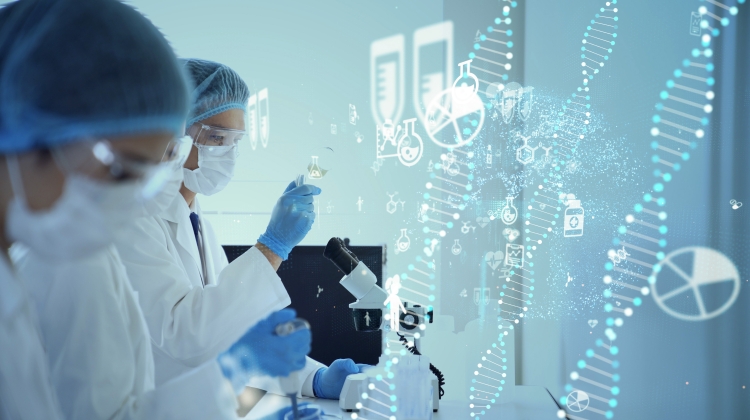
The US pharmaceutical manufacturing sector is preparing for continued, significant growth over the next decade, fueled by robust investments and evolving market demands. At the same time, this growth presents significant challenges—chief among them, the imperative to attract and retain a highly skilled workforce and to integrate advanced technologies that streamline operations and boost overall efficiency.
By 2028, the market is projected to reach $861.67 billion, reflecting a compound annual growth rate (CAGR) of 6.3%. Despite this optimistic outlook, 80% of pharmaceutical manufacturers report a mismatch between existing employee skills and evolving job requirements, exacerbated by rapid digitalization. While the industry's economic outlook is promising, workforce shortages and skills gaps threaten to hinder its trajectory.
Bridging the Skills Gap
By 2025, it is estimated that 30% of new drugs will be discovered using AI, reducing drug discovery timelines and costs by 25-50% in preclinical stages. This shift toward AI-driven innovation will require pharmaceutical companies to improve their workforce in advanced data analysis and machine learning techniques.
The rapid digitalization of the industry is widening the skills gap, with 83% of biopharma supply chain leaders emphasizing the need to upskill or reskill their workforce to support digital transformation. This disconnect highlights the need for aligned strategies between leadership and operational teams to mitigate productivity losses and maintain compliance in highly regulated environments.
A 2024 survey by the UKG Workforce Institute revealed that replacing a single skilled frontline worker can cost $10,000 to $40,000. Despite frontline workers experiencing significant disruptions to their roles—over half report immediate impacts from technological changes—only 10% of executives recognize the magnitude of this shift.
Evolving Skills and Facilities
As manufacturing processes grow more complex and technology-dependent, the pharmaceutical sector requires a workforce adaptation in areas beyond traditional manufacturing. Companies increasingly seek professionals skilled in:
- Data analytics and real-time monitoring to manage smart quality management systems.
- Regulatory information systems, necessitating familiarity with digital compliance processes.
- Artificial intelligence and automation, following the FDA’s guidance on using AI for regulatory decision-making.
The integration of AI, automation, and robotics is revolutionizing pharmaceutical production, enhancing efficiency and minimizing human error. High-precision material handling and consistent batch-to-batch production reduce costs and improve scalability while optimizing space utilization and production flexibility.
Facility design is also evolving, with greenfield and brownfield projects embracing design-build methodologies for faster delivery, better coordination, and reduced costs. These advancements reflect the industry's commitment to innovation in both infrastructure and operations.
Strategies for a Resilient Workforce
To address workforce shortages and the challenges of digital transformation, pharmaceutical manufacturers and members of their supply chain are adopting forward-thinking strategies as well as agile and flexible systems, including:
- Comprehensive plans that outline specific goals, timelines, and resources needed for digital transformation—aligning with the organization's overall objectives and considering the unique challenges of the pharmaceutical industry.
- Change management strategies that communicate the benefits of digital transformation and involve employees in the process.
- Cybersecurity measures, including encryption, access controls, and regular vulnerability assessments to protect sensitive manufacturing data.
- Hybrid work schedules to allow employees to balance on-site responsibilities with remote administrative tasks.
- Collaborations and investments with schools and industry groups to create training programs like apprenticeships and internships.
- Investments in data analytics and AI technologies to help companies improve decision-making, optimize processes, and enhance overall efficiency—this includes using advanced analytics and machine learning approaches to accelerate drug discovery and manufacturing processes.
- Virtual reality (VR) and augmented reality (AR) to provide safe, low-risk hands-on training environments, reducing risks and enhancing precision.
- Personalized growth pathways and robust employer branding to attract and retain top talent in this highly specialized industry.
Construction Industry Workforce Development Case Studies
The construction industry is also facing a growing shortage of skilled workers. As the demand for construction projects continues to rise, companies and organizations are stepping up to address this issue through innovative workforce development initiatives.
Burns & McDonnell established a Construction Academy in Houston, Texas, offering a flexible, hands-on approach to workforce development. The Academy provides training through on-site sessions at the Greater Houston campus, as well as mobile training units deployed to project sites nationwide. Key features include:
- The latest virtual reality (VR) and augmented reality (AR) technologies for immersive, low-risk training.
- Customizable programs designed to meet individual career goals and skill development.
- Industry-recognized credentials that boost employability and career advancement.
- Hands-on assessments that simulate real-world project scenarios, bridging the gap between theory and practice.
START Safety Training developed a mobile training unit that brings on-site safety education directly to construction sites. Key features include:
- Hands-on training stations for fall protection, confined space, and lockout/tagout.
- Air-conditioned classroom setup for 8-10 employees.
- Flexibility to accommodate larger groups at customer facilities.
The Alabama Associated General Contractors (AGC) implemented the Craft Training Act, which provides a stable funding source for construction skills education. This initiative:
- Collects funds from building permits on public works projects.
- Distributes grants for skills training programs statewide.
- Targets both entry-level workers and current employees.
The National Center for Construction Education and Research (NCCER) conducted several research initiatives to address the growing workforce demand gap. Their efforts focused on:
- Providing relevant data on workforce development.
- Creating actionable items for organizations to improve recruitment, training, and retention.
- Addressing the projected shortage of 2.6 million skilled craft professionals by 2028.
From training academies to mobile education units, these case studies showcase the diverse approaches being taken to address the ongoing labor shortages, bridge the current skills gap, and cultivate the next generation of construction professionals.
The Stakes for the Industry
The pharmaceutical manufacturing sector is at a crossroads. Its role in advancing healthcare and driving economic growth proves the urgency of resolving workforce challenges. Left unaddressed, these shortages could stifle innovation, disrupt production, and undermine the industry’s competitiveness.
Conversely, the convergence of cutting-edge technologies, strategic workforce investments, and innovative facility design offers hope for a brighter future. The US pharmaceutical market faces a pivotal moment: invest in human capital and technological infrastructure or risk ceding ground to global competitors.
Looking Ahead
The road ahead for US pharmaceutical manufacturing companies is both challenging and exciting. As the sector evolves, its ability to overcome workforce constraints will determine its trajectory in shaping the future of healthcare and the economy. The most successful companies will be those that see the workforce and technology not as opposing forces, but as mutually reinforcing drivers of innovation.
Disclaimer: iSpeak blog posts provide an opportunity for the dissemination of ideas and opinions on topics impacting the pharmaceutical industry. Ideas and opinions expressed in iSpeak blog posts are those of the author(s) and publication thereof does not imply endorsement by ISPE.