How does this negative image impact the future of single-use technologies (SUT) used in the biopharmaceutical industry? The emotional aspect of this subject must be counterbalanced by a more detailed understanding of the situation.
It is then necessary to question our practices, in a scientific and pragmatic approach: what is the contribution of SUT used in biopharmaceutical production within this heavy trend? How do the various stakeholders (producers, suppliers, users and waste management companies) work together to develop solutions to ensure the sustainability and continuity of these technologies while balancing environmental responsibility?
Our industry should also collaborate to elaborate consistent strategy and communication, supporting the statement that SUT remains generally more environmentally friendly than traditional stainless Steel (SSL) equipment, when all the factors for cleaning, steaming and performing maintenance are considered.
Few hard facts to initiate the discussion within our community:
- SUT used in the biopharmaceutical industry are evaluated to account for less than 0.01% of the total plastic waste generated annually worldwide.
- Unlike consumer packaging and plastic products, SUT end-of-life is subject to rigorous collection, decontamination, and treatment procedures. The vast majority are incinerated with or without energy recovery even if the landfill is still a common practice on the American and Asian continents (although it tends to decline). The risk of finding them in the environment is therefore extremely slim as the waste is controlled vs generally used in a non-controlled manner such as home or restaurant applications.
- By their very nature, the raw materials used to make SUT have been carefully selected to minimize their impact on the environment and human health and they are subjected to rigorous extractable studies in order to demonstrate their absence of toxicity. In addition, they must comply with all applicable regulations regarding chemicals considered at risk (REACH, BSE/TSE, Bis A phenol, phthalates, melamine, dioxin, etc.).
- To understand the environmental impact of a SUT, one must consider its entire life cycle, from its production (including its raw materials) to its elimination, through its transport and use.
- On top of the amount of heat, water and chemicals saved by use of SUT instead of SSL in biopharmaceutical industry, the growing tendency to use them to reduce the size and classification of controlled areas (production in functionally enclosed systems, ballroom concept) also results in a significant reduction in the energy consumption needed to maintain classified environments.
While this seems counter-intuitive, SUT is generally more environmentally friendly than traditional solutions. Existing life cycle assessment studies (LCA) have shown that switching from stainless steel systems (reusable after cleaning and sterilization) to single-use systems significantly reduces the carbon footprint and energy & water consumption of an industrial site. The SUT recovery and disposal chain also drastically limit the likelihood of finding them in oceans or rivers.
As illustrated in below graph (coming from GE Healthcare study published in 2017), the end-of-life is a minor contributor to the overall environmental impact of an SUT. The manufacturing process is the first impact factor, followed by transport and use.
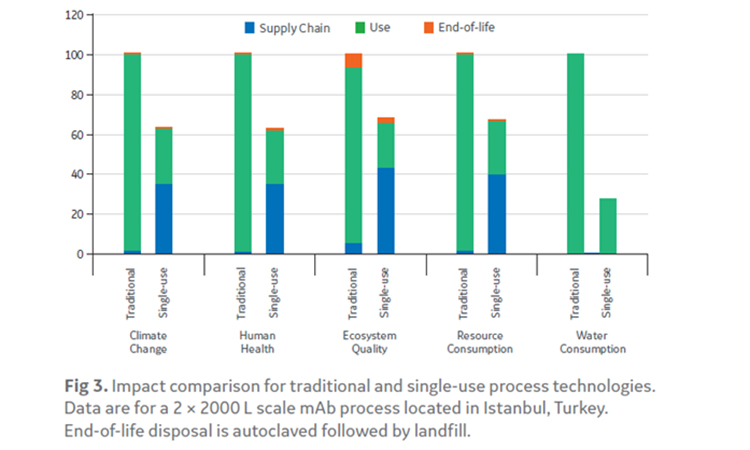
Nevertheless, manufacturers of SUT acknowledge that their increasing deployment in the industry requires them to develop strategies to ensure their long-term sustainability. The implementation of sustainable solutions, however, requires the contribution of all parties involved in the product lifecycle: manufacturers of raw materials and components, manufacturers of single-use systems, carriers, users and waste treatment companies.
SUT used in biopharmaceutical processes presents specific challenges related to their design and use (complexity of materials, regulatory requirements, biological risks, etc.) that makes the implementation of sorting and recycling solutions technically and economically more complex. However, many initiatives are underway within the industry to accurately assess possible pathways and move towards more circularity.
ISPE’s Disposables Community of Practice will work on that topic in coming months and we welcome your contribution to the discussion. We look forward to your comments and thoughts.
Join the Disposables Community Discussion