Upcoming Conference
2025 Conferences
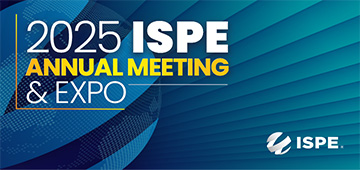
26 - 29 October 2025
Charlotte, NC USA and Virtual
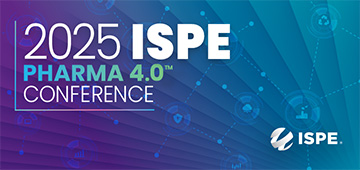
9 - 10 December 2025
Barcelona, Spain and Virtual
2026 Conferences
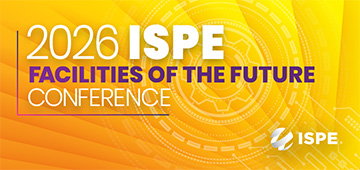
2 - 3 February 2026
San Diego, CA USA and Virtual

23 - 24 March 2026
Washington D.C., USA and Virtual

20 - 22 April 2026
Copenhagen, Denmark and Virtual
Past Conferences
To view past ISPE Conferences or to download presentations and attendee rosters visit the past conferences page.
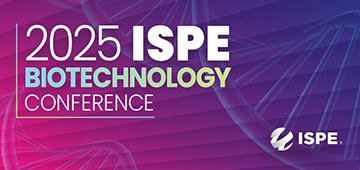
2 - 3 Jun 2025
Boston, MA, USA and Virtual
.jpg)
26 - 27 May 2025
Shanghai, China
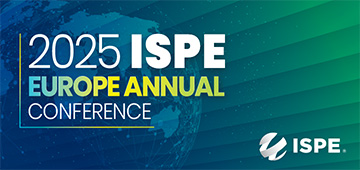
12 - 14 May 2025
London, United Kingdom and Virtual
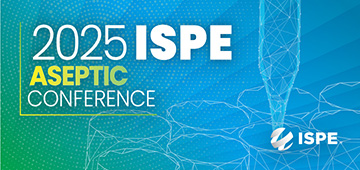
17 - 18 March 2025
Washington D.C., USA and Virtual
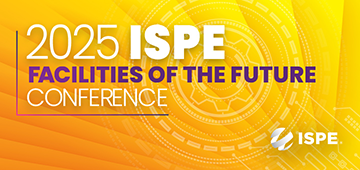
27 - 28 January 2025
San Francisco, CA USA and Virtual
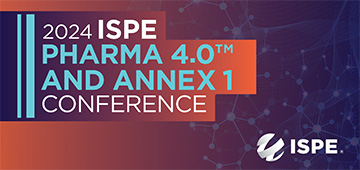
10 - 11 December 2024
Rome, Italy and Virtual
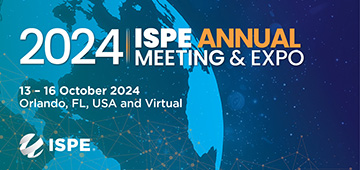
13 - 16 October 2024
Orlando, FL USA and Virtual
View All Past Conferences