Cook Pharmica, LLC
Facility Integration
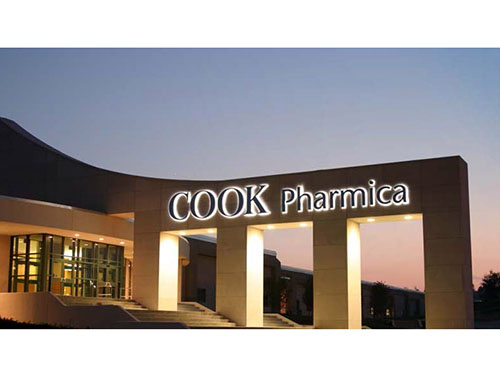
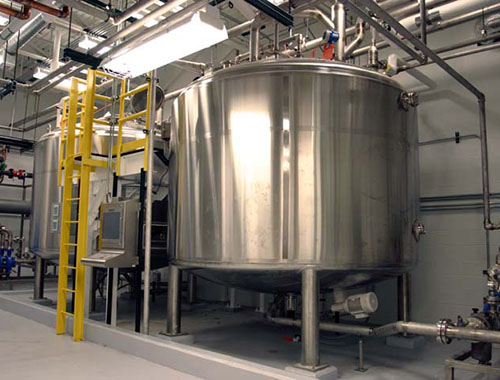
Project: Project Phoenix
Location: Bloomington, Indiana, USA
Size: 124,000 sq ft.
Cost: $70 million USD
Project Information: The growing trend in cell culture-based therapeutics inspired Cook Group, Inc., to transform an abandoned factory into an innovative new contract manufacturing facility. The result was Cook Pharmica's Project Phoenix facility located in Bloomington, Indiana, USA. Cook Pharmica is currently focused on mammalian cell culture-based production of Active Pharmaceutical Ingredients (API). In addition to its manufacturing train offering scale-up capabilities to 5,000L, Cook Pharmica also provides contract development and analytical services.
Product: Contract development and manufacturing services of mammalian cell culture-based API
Key Project Participants:
- Engineering Design Firms:
- Process / Process Utilities: CRB Consulting Engineers, Inc.
- Laboratory Design and Plant Utilities: Mussett Nichols and Associates (MNA)
- Office and Building Exterior: G.S. Ridgway & Associates
- Construction Manager: R.L. Turner Corporation
- Manufacturing Facility Design/Build: AES Clean Technology, Inc.
- Harry J. Kloeppel and Associates, Commissioning Agents, Inc. (CAI), Harrell-fish, Inc. (HFI), Cassady Electrical Contractors, Inc., Project Planning and Delivery (PP&D),Trane, Spriax/UltraPure, Cummins, Inc., the Rovisys Company, Inc. (Emerson Delta V), ESC, Cleaver-Brooks, Inc., YORK, Baltimore Air Coil (BAC), ABEC And Wave Biotech, Westfalia Separator, IPEC, Millipore, Pall Corporation, Mueller and DCI, Cornerstone Flooring and Linings, Siemens Building Technologies, Inc
Timeline:
- Start Date: December 2005
- Target Completion Date: Q4 2006
- Contract Signed: December 2006
Genentech
Project Execution
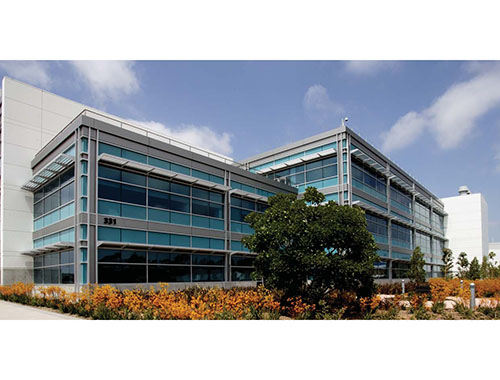
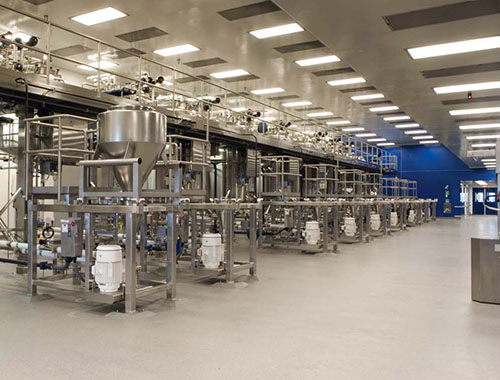
Project: Oceanside Product Operations (NIMO)
Location: Oceanside, California, USA
Size: 500,000 sq. ft.
Budget: $375 million USD Base Project
Project Information: Genentech is a leading biotechnology company that discovers, develops, manufactures and commercializes biotherapeutics for significant unmet medical needs. Upon U.S. Food and Drug Administration (FDA) licensure, which is expected in the first half of 2007, the facility will have 90,000 liters of capacity for the production of Avastin® (bevacizumab), a therapeutic antibody for the treatment of various forms of cancer. The six-building, 500,000-square-foot, master-planned campus features manufacturing, laboratory/office space, a warehouse, central utilities, and a "spine" inter-connecting space. The Oceanside Product Operations facility currently employs approximately 580 people.
Product: Avastin® (bevacizumab)
Key Project Participants:
- Architect/Designer: Ferguson Pape Baldwin Architects
- Engineering: CRB Consulting Engineers, Inc.
- General Contractor: DPR Construction, Inc.
- Other: Emerson Process Management, ITT Pure-Flo, Siemens Building Technologies, Inc.
Timeline:
- Avastin® Qualification lot campaign completion: Third Quarter 2006
Shanghai Roche Pharmaceuticals Limited
Project Execution Regional Excellence
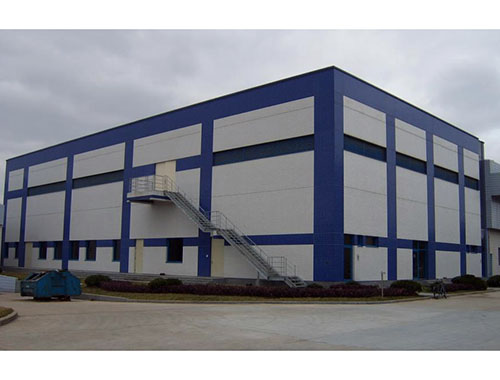
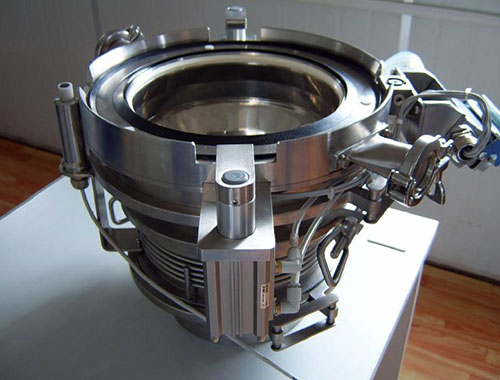
Project: Shanghai High Potent Production Project (SHiP)
Location: Shanghai, China
Size: Total Facility 2,100 sq. m.
Budget: 16.64 million USD
Project Information: The Shanghai High Potent Production Project (SHiP) was based on a modest budget and the entire project comprised construction of a new building for the production of highly active medicines with strict containment. The facility was created to manufacture tablets and capsules for the China market, and export of products for the prevention of organ rejection in transplant recipients and for the treatment of specific forms of cancer.
Products: Cellcept® (Mycophenolate Mofetil), Xeloda® (Capecitabine), and Furtulon® (Doxifluridine)
Key Project Participants:
- Project Management and Start-up: Shanghai Roche Pharmaceuticals Limited
- Architect and Construction Manager: M+W Zander (Shanghai) Co. Ltd
Timeline:
- Schedule: Commenced Detail Design - November 2004; First Validation Batches - April 2006
- Construction: Commenced - April 2005; Completed - October 2005
- Validation: June 2005 - April 2006
Taiyo Pharmaceutical Industry Co., Ltd
Equipment Innovation
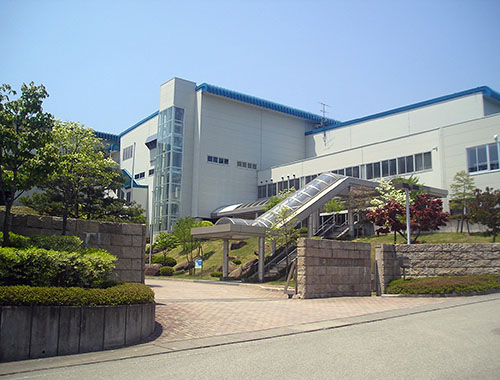
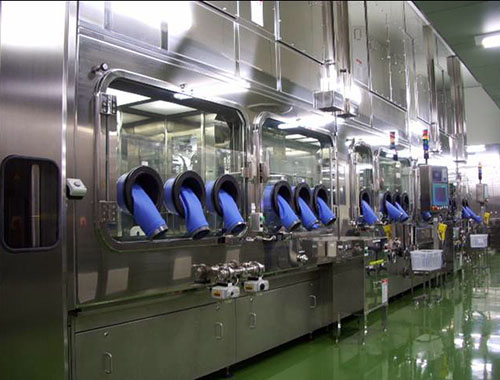
Project: Unit Factory Building PFS Manufacturing Line
Location: Takayama-city, Japan
Size: 11,744 m 2
Budget: Construction Cost: JPY 4,580,000,000; Equipment Cost: Primary Work - JPY 3,290,000,000 and Secondary Work - JPY 4,850,000,000
Project Information: Consistent with its low cost strategy and in accordance with its mid- to long-term management strategy, Taiyo Pharmaceutical Industry Co., Ltd. began the in-house project of manufacturing pre-filled syringes (PFS) at its Unit Factory Building PFS Manufacturing facility. The project currently produces a total of six products, including four plastic syringe containers and two glass syringe containers. In addition to the in-house syringe project, two other manufacturing lines have been successfully completed and produce pre-filled syringes equipped with high-speed type isolators.
Product: PFS Manufacturing Line
- Plastic Syringes Forming (Primary Work); Filling/Packing line for Plastic Syringes PFS (Primary Work)
- Glass Syringes Forming (Secondary Work); Filling/Packing line for Glass Syringes PFS (Secondary Work)
Key Project Participants:
- Designer - Production Facilities: Horiuchi Architectural Associates
- Designer - Production Equipment: Taiyo Pharmaceutical Industry Co., Ltd.
- Construction Management: Kashima Construction K.K.
- Daiichi Jitsugyou K.K., Itochu Foodec K.K., Clean Mechanical K.K., K.K. Airex, Sakura Seiki K.K., Winkler & Co., Ltd., Groninger, K.K. Systech Ushijima, Murata Seiko K.K., Hitachi Information & Control Solutions, Ltd., SIG, IWK, K.K Haginoya Machinery, SPAMI, K.K. Kit
Timeline:
- Start Designing: Primary Work - November 2002 --- Secondary Work - February 2005
- Start Construction: Primary Work - April 2003 --- Secondary Work - July 2005
- Plant Completion: Primary Work - May 2005 --- Secondary Work - March 2006
- Finishing Validation: Primary Work - July 2005 --- Secondary Work - August 2005
- Start Manufacturing: Primary Work - August 2005 --- Secondary Work - December 2006
Vetter Pharma-Fertigung GmbH & Co. KG:
Process Innovation
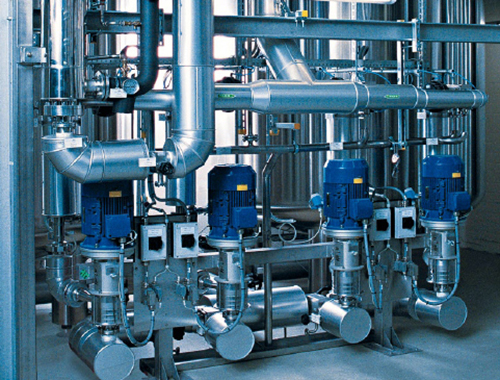
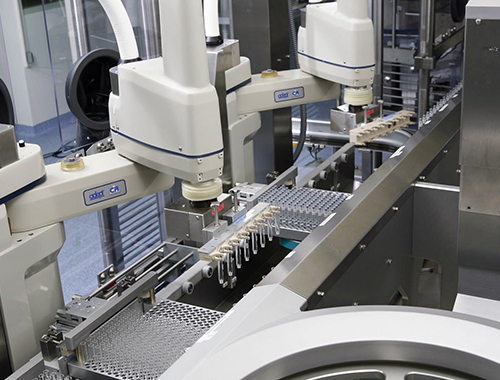
Project: New Facility Ravensburg Vetter South (RVS)
Location: Ravensburg, Germany
Size: Total facility 16,000 m 2 with 2,920 m 2 production area
Budget: 100 million euros
Project Information: The New Facility Ravensburg Vetter South took 36 months from start of detailed design to complete validation. Vetter started operation of the facility in October 2006 and its production site currently has two filling lines, which will be expanded to four in the near future. The facility is the result of more than a quarter of a century of expertise in prefilling. Automation was planned throughout the building, from door openers, to the use of the brand new Restricted Access Barrier System (RABS) on the filling lines. It features maximum automation; high standards of sterility, safety, and quality; self-sufficient production site with its own utility and power supply; unique production lines; and a capacity of 90 million units per year. RVS was designed to meet all of the challenges that technicians and scientists are faced with when aseptically filling syringes, cartridges, and vials.
Products: Contract manufacturing of innovative pharmaceutical products for parenteral administration
- Products produced: Filled dual-chamber syringes and cartridges lyophilized/liquid and liquid/liquid; filled vials lyophilized or liquid; filled cartridges liquid; expandable for two further lines
Key Project Participants:
- Architect: Vetter planning team
- Technical Building Management: Axima GmbH
- Structural Planning: Schneider & Partner Planungsgesellschaft mbH
- SiGeKo (Health and Safety Coordinator), Georg Reisch GmbH & Co., KG; Friedrich Burk GmbH & Co., KG; Dieter Eitle GmbH; Kirchhoff-Heine StraBenbau GmbH & Co.; Manfred Wucher GmbH; Peter Wiedemann GmbH; Johann Engler GmbH; Heinz Müller GmbH & Co. KG; Loos Deutschland GmbH; Ondeo Industrial Solutions GmbH; Stilmas S.p.a.; Atlas Copco Kompressoren und Drucklufttecknik GmbH; Huber & Ranner GmbH; GSA Euro-Diesel GmbH; Elektro Stotz GmbH & Co. KG; Siemens AG/SSG Starkstrom Systeme GmbH; Axima Refrigeration GmbH; Adept Technology Inc.; Robert Bosch GmbH; Binder GmbH; BHT Hygienetechnik GmbH; Belimed GmbH; Gastec GmbH; Föratec GmbH & Co. KG; Hof Sonderanlagenbau GmbH; Inova Pharma Systems GmbH; Montech Deutschland GmbH; Motus Engineering GmbH & Co. KG; Pink GmbH; Manfred Roth Edelstahl-Behälter und Apparatebau; Ruland Engineering & Consulting GmbH; SBM Schoeller-Bleckmann Medizintechnik Ges.m.b.H; Weiss GWE Gmbh
Timeline:
- Detailed design start: November 2003
- Construction start: February 2004
- Construction complete: December 2005
- Validation complete: PQ December 2006