Learn about the two companies winning the Operational Agility: COVID-19 Impact category for the 2021 Facility of the Year Awards:
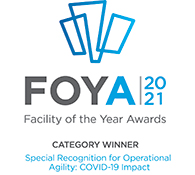
Gilead Sciences, Inc.
Location: Foster City, CA, USA
Project: Gilead Sciences, Inc., Center for Innovative Drug Research (CIDR)
Gilead Sciences, Inc. is a research-based biopharmaceutical company that discovers, develops, and commercializes innovative medicines in areas of unmet medical need. Striving to transform and simplify care for people with life-threatening illnesses, Gilead is headquartered in Foster City, California, with operations in more than 35 countries worldwide. To continue this vital mission and build upon this history of success, Gilead has created a collaborative incubator for tomorrow’s discoveries, incorporating their proven research practices while embracing leading-edge improvements to the research environment.
The new Center for Innovative Drug Research (CIDR) brought together multiple research groups from across Gilead’s Foster City campus into a single, 365,000-square-foot, state-of-the-art facility that supports world-class research, fosters a community of collaboration, and inspires life changing discoveries. Uniquely designed to support a modular way of working, the facility was designed into 3 disparate research wings connected by a shared spine, to allow for greater agility as researchers and development scientists focused on accelerating research. One of the largest pharmaceutical research facilities in California, The CIDR’s patient-focused mission is intrinsically connected to Gilead’s goals, offering an active discovery generator for treatments to existing and emerging conditions worldwide. During the brief period it has been in operation, the facility has already demonstrated its ability to support researchers by stimulating new discoveries and moving vital therapies forward.
Conceived as more than merely a “bricks and mortar building,” the Center creates a distinct home for its community of scientists. Researchers were highly involved in all aspects of the Center’s design and construction, integrating directly into the design team, leading to the deployment of an “agile” laboratory that allows the teams to pivot between different modalities and platforms effortlessly. It is this integrated flexibility (aimed to maximize collaboration and speed) that was built into every aspect of the design and engineering of the facility, that impressed the FOYA judging team and led to the CIDR being awarded a Facility of the Year Special Recognition Award for Operational Agility. In a year where the role of pharmaceutical facilities in enabling research, development, and manufacturing of therapies was more significant than ever, Gilead’s central research building was a great example of how we see engineering and facilities groups catalyzing innovation – by providing flexible, user-defined, technology-enabled facilities to bring therapies to life in a fast and efficient manner.
The judging committee recognized that agility as an engineering value driver is getting increasingly important, and in a year where the promise of therapies provided much-needed hope for the broader community, Gilead’s application of its research facilities within the CIDR was key in bringing forward Remdesivir – the first therapy that was approved to counter the debilitating impact of the COVID-19 virus. The facility design dominated by the overarching principles of interconnectivity between laboratories allows Gilead to expedite promising treatments to be developed without compromising other pipeline projects. In response to the COVID-19 pandemic, Gilead researchers leveraged this flexibility within the facility to further a promising molecule for clinical trials, which required quickly completing complicated development work. The CIDR supported this effort to efficiently and accurately transfer the technology to Gilead’s internal network, enabling it to be scaled to the point where clinical trials could begin in less than three months.
An example of the agility within the CIDR that the judging committee wanted to highlight was the design principle of minimizing time to upgrade aspects of the facility, as research needs changing. For example, one of the virology groups identified the need to upgrade their existing laboratory space with an additional layer of engineering controls to heighten biosafety protocols. – Through clever engineering design, several isolation improvements were able to be easily implemented without compromising space utility or causing significant interruption to room usage. The resulting BSL-2 enhanced space now enables researchers to work with more infectious pathogens and pursue avenues of research not anticipated at the building’s inception.
In addition to the agility aspect of the facility, the judging team also noted the open-space layout of the entire space as being a unique construct within research facilities of this scale. This open-space layout and the thoughtful design of various engineering systems within the building (air filtration, sensors, spatial layouts, flow of process) allowed research teams to continue working on campus during California’s Shelter-in-Place directive, through better distancing, and to still find ways to collaborate in a safe and effective environment.
As we look to reward facilities that catalyze the collective brilliance of our research and development teams in the industry, the FOYA judging team felt this facility merited this award and special recognition for achieving the key imperative of operational agility, while also earning other engineering awards (LEED Gold on sustainability, safety record, budget and schedule adherence, and scientific fit).
Congratulations to Gilead Sciences, the project team and all the partners that supported this project.
Supply Partners
Manufacturer/Owner Name - Gilead Sciences, Inc.
Engineer/Architects (A&E):
- Flad Architects
- EXP
- Rutherford + Chekene
Construction Manager - Gilead Sciences, Inc.
Main/General Contractor - McCarthy Building Companies, Inc.
Piping Subcontractor - Southland Industries
HVAC Subcontractor - Southland Industries
Automation and Control Supplier - Banks Integration Group
Grand River Aseptic Manufacturing
Location: Grand Rapids, MI, USA
Project: Grand River Aseptic Manufacturing Large-Scale Fill-Finish Facility
This project was selected by the ISPE FOYA judging committee as a special recognition award recipient for operational agility, for creating a facility that was able to support a pressing need of the day, response to the COVID-19 pandemic, through careful design, a sense of urgency and collaborative project execution. The project, an ambitious new fill-finish facility, was initially conceived as a facility that could address the need to satisfy product demand that the company was facing. Grand River Aseptic Manufacturing (GRAM) purchased a 1.5-acre lot to build a facility that would have state-of-the-art equipment, a people-friendly workspace, and manufacturing flexibility.
GRAM kicked off the project with strategic site selection and equipment choices. At the time, they had no idea how their focus on flexibility would impact the project’s value and impact during a global pandemic. As a contract development and manufacturing organization (CDMO), they wanted increased capacity to better serve current and future clients, but also designed the facility to provide maximum flexibility to respond to industry needs. This project objective drove every decision: from choice of technology to which vendors would work on the team.
With the COVID-19 pandemic, GRAM launched a rapid response to an evolving public health crisis. GRAM launched into full readiness in response to possible partnerships and doubled down on qualification and validation of the facility. In early 2020, they received a BARDA questionnaire which confirmed that this facility was key to supply issues that were anticipated for vaccines and therapies. GRAM’s new facility was perfectly set up for vaccine production because it was designed for single-use technology. Also, the incredible flexibility that had been built in to serve a wide swathe of clients meant they could accommodate any COVID-19 vaccine processes being developed by various pharmaceutical companies. This delivery of this facility ahead of schedule required the team to accelerate the construction and qualification of the new facility, which they did, and for this achievement which demonstrated tremendous operational agility, the ISPE FOYA judging committee would like to award GRAM a Special Recognition Award.
While 2020 was a year that heralded the role that pharmaceutical facilities played in the pandemic response, this facility stood out for the agility and responsiveness that was demonstrated in becoming available to support supply needs: GRAM created a project execution framework that allowed safe operations while the schedule was being accelerated. This included PPE provisions and, facility inspections that were done before and after the construction day so as to limit exposure and keep the inspection process moving forward. In addition, GRAM started the qualification process in parallel with final construction to get a jump on the schedule. The judging committee recognized that bringing a facility online is stressful under normal circumstances - but doing it during a pandemic with less staff and higher stakes required laser focus on the enormous social impact the facility would offer, and a deep commitment to the patients and our community.
GRAM’s new facility was officially selected to help meet the federal government’s Operation Warp Speed goals to help respond to the demands presented by the COVID-19 pandemic. In early June 2020, GRAM was selected by the U.S. Department of Health and Human Services and the U.S. Department of Defense to support the expansion of the United States’ capacity for manufacturing and distributing vaccines or therapeutics related to the COVID-19 pandemic. On September 14, 2020, GRAM ran its first batch of a COVID-19 vaccine candidate—a full six weeks ahead of the original operational schedule.
The judging committee recognized that agility as an engineering value driver is getting increasingly important, and in a year where the promise of therapies and vaccines provided much-needed hope for the broader community, GRAM’s sense of urgency and, commitment to creative project execution and collaboration are commendable. The facility design reflects the flexibility, the speed, and the operational agility that ISPE believes are critical to continue driving our collective value.
Congratulations to GRAM, the project team and all the partners that supported this project.
Supply Partners
Manufacturer/Owner Name - Grand River Aseptic Manufacturing
Engineer/Architects (A&E) - CRB
Construction Manager - CRB
Piping Subcontractor - Andy J Egan
HVAC Subcontractor - Andy J Egan
Automation and Control Supplier - Rockwell Automation
Major Equipment Suppliers/Contractors:
- Electrical Subcontractor – Buist Electrical
- Architectural – D&D Building