- Speakers

2024 ISPE Pharma 4.0™ and Annex 1 Conference
Thank you to all who made the 2024 ISPE Pharma 4.0™ and Annex 1 Conference such a big success!
Thank you to all who made the 2024 ISPE Pharma 4.0™ and Annex 1 Conference such a big success!
Please Note:
- All full-access registration (virtual & in-person) includes access to speaker presentations, on-demand content, and other conference material.
- NOTE: Material is only available from those speakers/companies that permitted distribution.
- Registrants will receive email notification when the on-demand content is available.
- On-demand content is accessible for 90 days.
Hear From Top Industry Thought Leaders on the Challenges and Solutions Impacting the Pharmaceutical Industry
Conference Topics
Expert Insights
Hear from industry leaders and regulators who will share their perspectives on the future of pharmaceuticals.
Pharma 4.0 Case Studies & Lessons Learned
Gain actionable insights into the latest Annex 1 revisions and their application in pharmaceutical operations. These sessions will explore the intersection of regulatory frameworks such as Eudralex with cutting-edge digital transformation, robotics, and contamination control strategies.
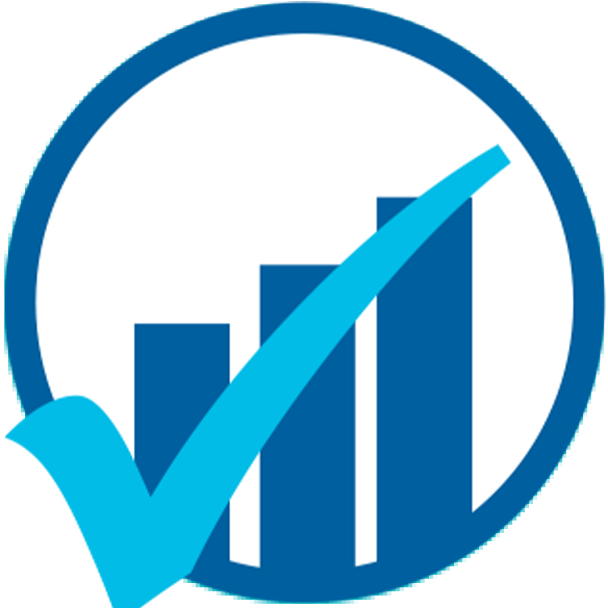
Annex 1 Implementation & Pharma 4.0
Learn strategies for implementing the latest Annex 1 version through real-world case studies, ensuring smooth operational changes and hardware integration.
Pharma 4.0 Interconnected Facility Design & Construction
Gain insight into how 'plug and produce' principles offer opportunities for creating an integrated and interconnected facility, but also come with their challenges.
How ATMPs Manufacturing can be Supported by Annex 1 & Digital Transformation
Discover how the pharmaceutical industry can ensure the delivery of safe products to patients by improving their processes, implementing Annex 1, and utilizing enhanced data management for faster product release.
Featured Speakers
Head of Institute Surveillance
Austrian Agency for Health and Food Safety (AGES)
Independent Senior Advisor Biopharmaceuticals
Former Head of Biopharma Business Unit, Boehringer Ingelheim
Engineering, Maintenance Excellence & Digitalization Lead Garbagnate
Bayer Healthcare Manufacturing SRL
SVP Head of Product Supply Fill & Finish Expansions
Novo Nordisk A/S
Transformation Strategist and Head of Research
IAAE
Executive Pharmaceutical Assessor
HPRA
Senior Scientific Specialist
EMA
GMP Inspector
AGES - Austrian Agency for Health and Food Safety
Your Conference Experience

Expo Hall
Expo Hall
Explore groundbreaking innovations and network with industry leaders at our dynamic expo hall.
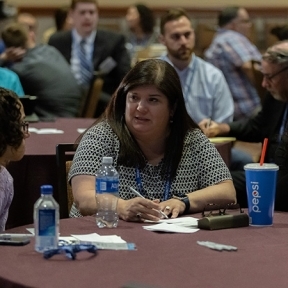
Professional Training
Professional Training
Connect with top industry experts and expand your professional network at our exclusive networking sessions.

Live Streams
Live Streams
Experience the conference from anywhere with our interactive live stream.
Keynote Speakers
Keynote Speakers
Subject matter experts and top leaders in the pharmaceutical industry.
Conference Highlights

Unlock the Future of Pharmaceutical Manufacturing: Learn from Industry Leaders at the 2024 ISPE Pharma 4.0™ and Annex 1 Conference
In an era where technological advancements are reshaping every industry, the pharmaceutical sector is no exception. The 2024 ISPE Pharma 4.0™ and Annex 1 Conference is the gateway to understanding and leveraging digital transformation and artificial intelligence (AI) in pharmaceutical manufacturing. This year, ISPE is bringing together global thought leaders from industry stalwarts like AstraZeneca, Bayer, BioNTech, Boehringer Ingelheim, Johnson & Johnson Innovative Medicines, Merck Serono S.P.A., Novo Nordisk A/S, and Takeda Austria GmbH. They will share their invaluable insights into their digitalization journeys, offering key learnings that can be directly applied to businesses.

Pharma 4.0™ and Annex 1 Implementation: A New Era for Aseptic Manufacturing
The pharmaceutical industry is in the middle of a transformative shift, driven by the dual forces of Pharma 4.0™ and the updated Annex 1 guidelines. These changes are introducing innovations that not only enhance the quality and safety of sterile manufacturing but also leverage new technologies to optimize efficiency and compliance. This track will bring together industry experts to discuss how Pharma 4.0 principles can support the implementation of Annex 1. From contamination control strategies to robotics and data-centric architectures, these sessions will provide attendees with actionable insights and solutions to stay ahead in an evolving regulatory landscape.

Exploring the Future of ATMP Manufacturing from Digitalization to Navigating Regulations
In an era where advanced therapy medicinal products (ATMPs) are revolutionizing healthcare, the 2024 ISPE Pharma 4.0™ and Annex 1 Conference, taking place 10-11 December in Rome, Italy, and virtually, will feature a track titled, "How ATMPs Manufacturing can be Supported by Annex 1 and Digital Transformation." This track will bring together experts from various fields to discuss the integration of digital technologies and regulatory frameworks in the development journey of ATMPs, as well as provide insights into real world implementation data and lessons learned. With a focus on enhancing compliance, efficiency, and accessibility, the track will feature six engaging talks and provide attendees with valuable insights into the future of this rapidly evolving sector.
ISPE Pharma 4.0™ and Annex 1 Conference Gallery
International Program Committee
Annex 1 Co-Chair
Senior Consultant Aseptic Processing & Containment
SKAN AG
Pharma 4.0 Co-Chair
Managing Consultant, Compliance Consulting
NNE
Past Chair
Vice President Vetter Development Service External Affairs
Vetter Pharma Fertigung GmbH & Co KG
International Board Liaison
Senior Director, Global Engineering & Technology
Johnson & Johnson
Women in Pharma Liaison and Affiliate Liaison
Vice President Strategic Development, Marketing & Communication - Partner
PQE Group
Sr.Director- Quality and Compliance
Fujifilm Diosynth Biotechnologies
Director, Head of Novel Modalities Market Development EMEA
Merck KGaA
Fellow - Digital Technology, Associate
CRB
Regulatory Advisor
ISPE
Managing Director
Q-FINITY Quality Management
Senior Industry Advisor and Principal Consultant for Advanced Therapies
Koerber Pharma Software Inc
Founder & CEO
LifeBee | a ProductLifeGroup Company
Vice President QA International
Cencora
Managing Director
Memo3 GmbH
Operation Technology, Digital & Data Associate Director
Merck Serono S.P.A.
Executive Industry Advisor
Körber Pharma Software GmbH
Emerging Leader
Sales Manager
VTU Engineering GmbH
Emerging Leader
Network Technology Robotics Lead
F Hoffmann-La Roche AG
Emerging Leader
Process Engineer MS&T Drug Substance
Takeda
Emerging Leader
Quality Assurance Project Manager
Lonza AG
Emerging Leader
Project Manager
Bayer AG (Supply Center Grenzach)
Emerging Leader
Project Advisor
Aseptic Mind
Emerging Leader
Independent
Zauner Consulting