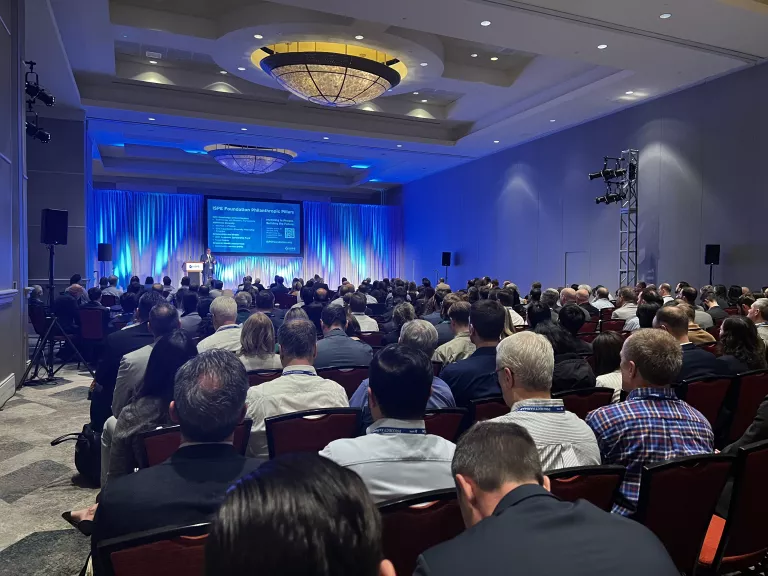
2025 ISPE Aseptic Conference
Thank you to all who made the 2025 ISPE Aseptic Conference such a big success!
Thank you to all who made the 2025 ISPE Aseptic Conference such a big success!
Please Note:
- All full-access registration (virtual & in-person) includes access to speaker presentations, on-demand content, and other conference material.
- NOTE: Material is only available from those speakers/companies that permitted distribution.
- Registrants will receive email notification when the on-demand content is available.
- On-demand content is accessible for 90 days.
Top Industry Thought Leaders at 2025 ISPE Aseptic Conference
The Conference Experience at the 2025 ISPE Aseptic Conference
Why you should attend an ISPE Conference?

Panel Session at Aseptic 2025

Expo Hall

New This Year, Ed Talks

Aseptic 101 Attendees

International Program Committee

Networking at Aseptic 2025
Featured Speakers
Senior Vice President, Indianapolis Parenteral Manufacturing
Eli Lilly and Company
CEO
TAG1 Inc.
Vice President, Xeno and Regenerative Medicine Operations
United Therapeutics Corp.
Your Conference Experience
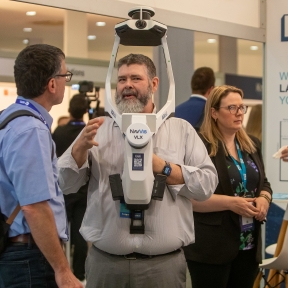
Expo Hall
Expo Hall
Explore groundbreaking innovations and network with industry leaders at our dynamic expo hall.
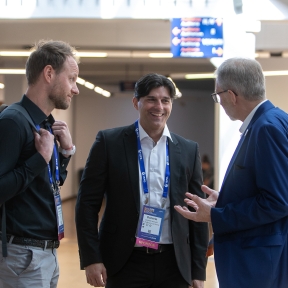
Networking
Networking
Connect with top industry experts and expand your professional network at our exclusive networking sessions.

Live Streams
Live Streams
Experience the conference from anywhere with our interactive live stream.

On-Demand Content
On-Demand Content
Access exclusive conference content anytime with our on-demand library for 90 days.
Conference Highlights
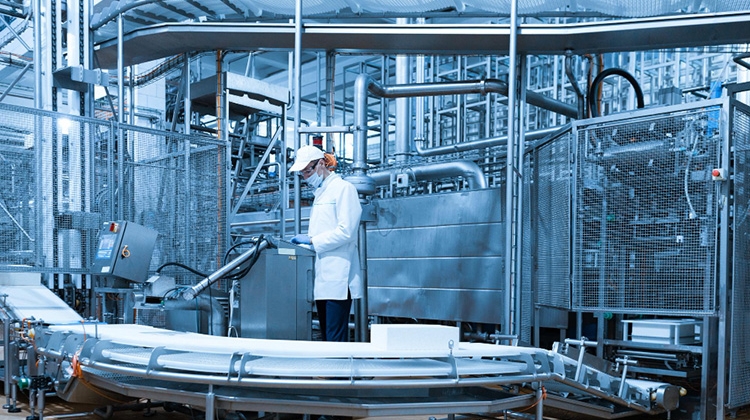
Diverse Case Studies at the 2025 ISPE Aseptic Conference
As aseptic processing evolves rapidly both from technological and regulatory perspectives, the 2025 ISPE Aseptic Conference will feature a full track dedicated to case studies, with six case studies planned for day one of the conference on Monday, 17 March. The case study-centered sessions will be presented by groups that have successfully implemented innovative solutions to the heightened expectations prescribed by Annex 1 and other drivers.

Unlock the Future of Aseptic Processing at the 2025 ISPE Aseptic Conference
The pharmaceutical industry continues to face increasing demands for more efficient and effective manufacturing processes, particularly when it comes to aseptic processing. With an emphasis on safety, sterility, and the quality of biologics and injectables, the field of aseptic processing is critical for delivering life-saving medications. ISPE invites all pharmaceutical professionals to join the 2025 ISPE Aseptic Conference, where industry leaders will gather to share insights, innovations, and solutions that will shape the future of aseptic processing.

Regulation and Pharma 4.0™ at the 2025 ISPE Aseptic Conference
Advances in pharmaceutical regulation and pharmaceutical technology don’t always coincide. Each advancement moves on its own schedule, driven by its own unique forces. But sometimes there is a synergy, when advances in technology can help regulators to achieve their objectives and changes in regulation come at just the right time to enable a technology to be impactful. This interplay between innovation and compliance will take center stage at the 2025 ISPE Aseptic Conference, particularly in the "Regulations and Pharma 4.0" track.
Conference Gallery
International Program Committee
Chair
Sr. Fellow - Aseptic and Sterile Products, Vertical Market Leader
CRB
International Board and Foundation Liaison
President
Genesis AEC
Women in Pharma® Liaison
Senior Director, Value Stream CAR - T Manufacturing Operations
Bristol Myers Squibb
Chapter Board Liaison
Energy Program (Sustainability) Lead
AstraZeneca
Associate Director Process Engineering, Regenerative Medicine
United Therapeutics
Chairman and CEO
Biogenera
Senior Consultant Aseptic Processing & Containment
SKAN AG
Director of Business Development
GBA Life Sciences
Sr. Regulatory Compliance Consultant
Higgins Pharma Consulting Group
Senior Product Manager
Syntegon Technology GmbH
Advisor - Project Management
Eli Lilly & Company
Vice President Vetter Development Service External Affairs
Vetter Pharma Fertigung GmbH & Co KG
Emerging Leader
Mechanical Engineer
3P Innovation
Emerging Leader
Process Engineer II
Genesis AEC
Emerging Leader
Process Engineer III
CRB